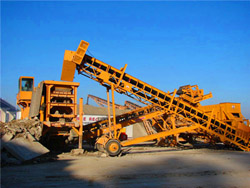
(PDF) Performance optimization of an industrial ball mill
In this investigation, we optimize the grinding circuit of a typical chromite beneficiation plant in India. The run-of-mine ore is Staurk Machinery. Ball mill is the key machine in the grinding stage,how to improve its efficiency is very important. 1. Change the grindability of raw ore. The 9 ways tell you how to improve ball mill efficiency China staurk
احصل على السعر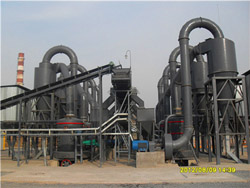
The energy efficiency of ball milling in comminution
Schellinger's calculated ball mill efficiency, in dry or wet ball mill grinding, ranges between 10% and 19%, with the higher figure occurring at the optimal Improving the grinding efficiency in tumbling mills is essential to minimising comminution energy consumption. Over the years, fundamental insights gained from ball mill Rethinking Grinding Efficiency in Ball Mills CEEC (Coalition for
احصل على السعر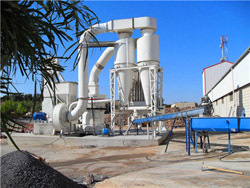
Effect of grinding media on the milling efficiency of a ball mill
The size of grinding media is the primary factor that affects the overall milling efficiency of a ball mill (e.g. power consumption and particle size breakage). To improve the efficiency of grinding in ball mills closed circuit is proposed in the separation system to introduce fresh air. It is proposed to discharge excess separation air into a high(PDF) Analysis of the efficiency of the grinding process
احصل على السعر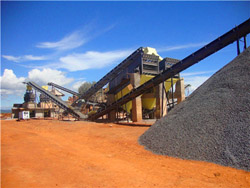
Addition of pebbles to a ball-mill to improve grinding efficiency
This paper compares the performance of a 25/75 pebble/ball (volume ratio) composite charge to ball-milling, under conditions typical for a ball-mill in SABC circuits, Given the important role of grinding operation, to develop large-scale grinding equipment, improve grinding efficiency, and optimize mill structure parameter An innovative approach for determining the grinding
احصل على السعر
Energy and exergy analyses for a cement ball mill of a new
Ghalandari and Iranmanesh [20] analyzed the energy and exergy of a cement ball mill to improve the grinding efficiency. According to Katsioti et al. [21] [22],One of the important problems for ball mills is the problem of reducing the efficiency of grinding material. The degree of grinding of materials in ball mills ensures the quality of the product. That is why this work is aimed at choosing a way to improve the design of the ball mill in order to increase the efficiency of grinding material.Improvement of the structure of a ball mill with the purpose of
احصل على السعر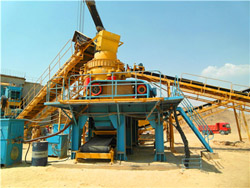
How to improve working efficiency of ball mill
If too much feeding will cause the ball mill to rise, the rising belly will reduce the efficiency of the steel ball inside the ball mill, and the qualified materials can not be discharged, reducing the output. Therefore, it should be uniformly fed during the feeding process. Improve Material of Liner and Effective Volume of CylinderAccording to Swart et al. [9], ball mills are mostly used because of their very high size reduction ratio, although they have a very low energy efficiency of about 20%. According to Conger et al. [10], many factors affecting ball mill effi-ciency include mill design, liner design, mill speed, charge ratio, and grinding media properties.Grinding Media in Ball Mills-A Review Preprints
احصل على السعر
Improvement of the structure of a ball mill with the purpose of
When grinding cement, ferrous and non-ferrous metals is commonly used drum ball mills. For example, the share of cement in grinding mill consumes more than 60% of the energy used to manufacture it.Ball mills for fine grinding cement clinker and additives are widely used around the world. To improve the efficiency of a ball grinding the ball mills are transferred in closed circuit with air(PDF) Analysis of the efficiency of the grinding process in closed
احصل على السعر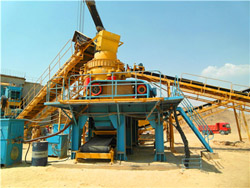
Addition of pebbles to a ball-mill to improve grinding efficiency
Improvements in the grinding efficiency of a secondary ball- reduce ball addition to the primary mill and the power drawn mill, by the addition of small pebbles from the primary circuit. In: Proceedings of the XXV International Mineral Processing Congress (IMPC 2010), Brisbane, 6– by the primary mill will then decrease.Ball mill is the key machine in the grinding stage,how to improve its efficiency is very important. 1. Change the grindability of raw ore. The hardness, toughness, dissociation and structural defects of the raw ore determine the difficulty of grinding. In production, if you encounter more difficult ores or require fine grinding, you can9 ways tell you how to improve ball mill efficiency China staurk
احصل على السعر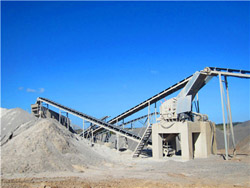
The energy efficiency of ball milling in comminution
In terms of this concept, the energy efficiency of the tumbling mill is as low as 1%, or less. For example, Lowrison (1974) reported that for a ball mill, the theoretical energy for size reduction (the free energy of the new surface produced during grinding) is 0.6% of the total energy supplied to the mill setup.Ball-mills are used widely for secondary grinding. Loveday (2010) reported on laboratory tests in which small pebbles (7–25 mm) were used in various proportions with balls. The optimum proportion of pebbles, by volume, was found to be about 25%. Substantial savings in power and ball consumption were achieved, with no loss in Addition of pebbles to a ball-mill to improve grinding efficiency
احصل على السعر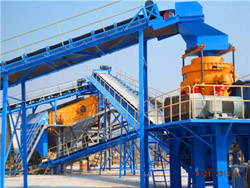
(PDF) Performance optimization of an industrial ball
An increase of over 10% in mill throughput was achieved by removing the ball scats from a single -stage SAG mill. These scats are non- spherical ball fragments resulting from uneven wear of ballsOptimizing the critical speed of a ball mill can improve grinding efficiency and product quality by ensuring the grinding balls are effectively lifted and distributed for optimal grinding. Application of Ball Ball Mill- Principle, Application, Uses, Critical Speed,
احصل على السعر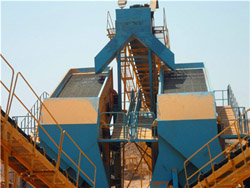
Optimization and transformation of 300MV units steel ball coal mill
Abstract and Figures. Comprehensive treatment,we should have a test on the 300 MV unit steel ball coal mill pulverizing system.At the same time,analyze the main operating parameters beforeThe problem of high temperatures in ball mills is a prevalent problem that needs to be addressed to improve their performance and efficiency. By implementing the solutions discussed in this article, such as proper lubrication, regular maintenance, and the use of cooling devices, the temperature of a ball mill can be effectively controlled.Four Ways To Improve The High Temperature Problem Of Ball Mill
احصل على السعر
Analysis of the efficiency of the process in closed circuit ball mills
Ball mills for fine grinding cement clinker and additives are widely used around the world. To improve the efficiency of a ball grinding the ball mills are transferred in closed circuit with air-separators of various designs. In the article the analysis of existing grinding circuits on the basis of closed circuit ball mills made.In terms of this concept, the energy efficiency of the tumbling mill is as low as 1%, or less. For example, Lowrison (1974) reported that for a ball mill, the theoretical energy for size reduction (the free energy of the new surface produced during grinding) is 0.6% of the total energy supplied to the mill setup.The energy efficiency of ball milling in comminution
احصل على السعر
Addition of pebbles to a ball-mill to improve grinding efficiency
Abstract. Nkwanyana and Loveday (2017) used batch grinding experiments in a 0.6 m diameter mill to test partial replacement of steel balls (37.5 mm) for secondary grinding, by partly rounded pebbles (19–75 mm) from a SAG mill. At the optimum pebble content of 25% by volume, a 25% saving in steel ball consumption and a 15% The equation below shows the relationship between ball mill grinding efficiency and material fineness: Kd = G2/G1 = (d1/d2) X (1) *Note. Kd: the relative productivity of the mill; G1 & G2: respectively represent the mill output (T / h) when the feed particle size is d1 and d2; X: the index, which is related to material characteristics, productHow to Improve Cement Ball Mill Performance
احصل على السعر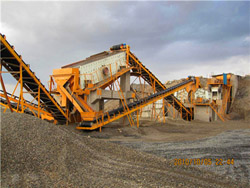
The energy efficiency of ball milling in comminution
Comminution represents up to 50% of the total energy consumption in the mineral production process [2]. Moreover, comminution using ball milling is highly inefficient due to heat and mechanical4. Sampling inside mill (mill test) Sampling of material. Take ~1 kg sample every 1 m along mill axis. Each sample collected from 3 point in the same cross section. Removed some balls and taken sample. -First and last sample in each compartment should be taken. from 0.5 m off the wall or diaphragms. 4.Cement Separator & Ball Mill Optimization
احصل على السعر