
Ball-impact energy analysis of wet tumbling mill using a
A numerical analysis of the impact energy distribution in the vessel showed that relatively high-impact energies of the balls were intensively generated near the vessel wall, indicating that the wet ball-milling processes were controlled by the impact energy A numerical analysis of the impact energy distribution in the vessel showed that relatively high-impact energies of the balls were intensively generated near the Ball-impact energy analysis of wet tumbling mill using a
احصل على السعر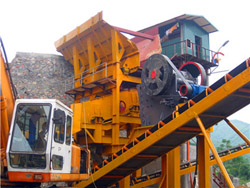
Overview of milling techniques for improving the solubility
Fundamentally, a ball mill comprises a vessel or vial filled with balls, or rods, constructed from a variety of materials such as ceramic, agate, silicon nitride, sintered MATERIALS IN BALL MILLS G. V. Kukolev, I. Ya. Piven', and V. S. Polishchuk UDC 666.3.022.2 Wet milling of solids n ball mills is more intensive than dry The effectiveness of wet milling materials in ball mills
احصل على السعر
Wet ball milling of niobium by using ethanol, determination
Abstract This study investigates the effect of using ethanol as the process control agent during the wet ball milling of niobium (Nb). Dried nanocrystal Nb powders, In summary, the formation rate of LHTO through the wet mechanochemical reaction using a planetary ball mill is mainly controlled by collision of ball media in the Effect of ball collision direction on a wet mechanochemical reaction
احصل على السعر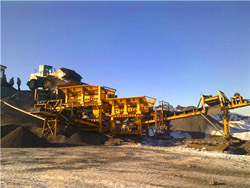
Dry ball milling and wet ball milling for fabricating
The mill vessel was made of polyurethane (0.5 l), and the milling balls were made of zirconia (1, 3 and 5 mm in diameter). The weight ratios of ball-to-powder and 3 kinds of milling balls are 5:1 and 1:1:1, Abstract Ball milling is a simple, fast, cost-effective green technology with enormous potential. One of the most interesting applications of this technology in the field of cellulose is the preparation and the chemical Ball milling: a green technology for the
احصل على السعر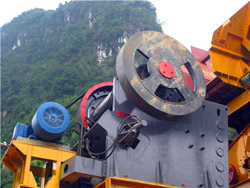
Ball milling as an important pretreatment technique in
In wet ball milling, biomass fibers swell with water and hydrogen bonding between nanofibers weaken, resulting in defibrillation of the bundle of nanofibers. In High-purity electrolytic copper powders and yttria powders were used as raw materials to fabricate CMCs. Average particle sizes of Cu and Y 2 O 3 are 43 and 4 μm, respectively. Contents of Y 2 O 3 are 2 Dry ball milling and wet ball milling for fabricating
احصل على السعر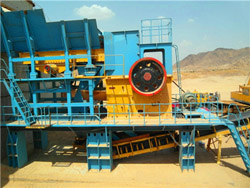
Pharmaceutics Free Full-Text Preparation and Evaluation
Wet ball milling (WBM) is a process of size reduction using bead–particle collisions in a rotating vessel, enabling the milling of heat-sensitive materials and contamination-free refinement . The mechanical parameters of ball milling, ball-mill solvent, and rotation time strongly influence the physicochemical properties of the particles [ 27 ].1. Introduction. Wet ball-milling processes using horizontal tumbling mills have been conventionally employed in various industries, e.g., mining, ceramics, foods, fine chemicals, and pharmaceuticals, owing to their versatility (Danha et al., 2015; Iwasaki et al., 2013; Katou et al., 2019).Mechanical energy, such as compressive and shearing Ball-impact energy analysis of wet tumbling mill using a
احصل على السعر
Chapter 10 Selection of Fine Grinding Mills ScienceDirect
In the former, there are tumbling, vibration, planetary ball mills and the like. The mills in the latter group are further classified after the shape of the mill casing into tower type, agitation vessel type, tubular type and annular type. The ball media mills can be used for dry and wet grinding and in batch and continuous operation.TECHNICAL SPECIFICATION OF WET BALL MILL EQUIPMENT (SUB ASSEMBLY OF FGD SYSTEM) 03 18.03.2022 P V S BABU AMAN KHRK 02 02.07.2021 P V S BABU AMAN KHRK 01 20.07.2020 P V S BABU AMAN SG Equipment and Material must be suitable for the range of ambient site conditions. B) PROJECT LOCATION TECHNICAL SPECIFICATION OF WET BALL MILL
احصل على السعر
A Review of the Grinding Media in Ball Mills for Mineral
The ball mill is a rotating cylindrical vessel with grinding media inside, which is responsible for breaking the ore particles. Grinding media play an important role in the comminution of mineral ores in these mills. This work reviews the application of balls in mineral processing as a function of the materials used to manufacture them and the Whether in the chemical industry, mining, ceramics production, or materials research, wet ball mill plays a key role. The process involves placing solid particles in a liquid, along with ball-shaped grinding media, in a grinding vessel. or rubber) is added to the vessel along with the material to be ground. The vessel is then rotated orWhat is Wet Ball Milling? Wet Ball Mill Machine For Sale
احصل على السعر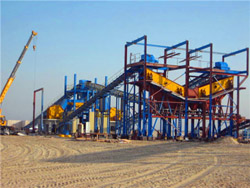
Ball milling: a green technology for the preparation and
The ball mill Ball milling is a mechanical technique widely used to grind powders into fine particles and blend materials. 18 Being an environmentally-friendly, cost-effective technique, it has found wide application in industry all over the world. Since this mini-review mainly focuses on the conditions applied for the preparation andHowever, the experimental average head height at J = 0.5 slightly increased with φ owing to an increase in the frictional force between the ball and the vessel wall with increasing normal stress acting on the balls. Conclusions. A modified quasi-wet DEM considering the vessel speed dependence of the friction coefficient of a ball is Ball-impact energy analysis of wet tumbling mill using a
احصل على السعر
(PDF) Ball milling : A green technology for the preparation
Fig. 2 (a) Schematic representation of a ball mill (horizontal section); (b) di ff erent types of instruments (this fi gure has been adapted from ref. 19 with permission from Royal Society ofMechanical alloying (MA) is a typical solid-state process that occurs at room temperature between powders of diffusion couples utilizing various types of ball mills. Ball milling has evolved over the last five decades from a standard technique in mineral dressing and powder metallurgy, where it was primarily used for particle size reduction Mechanical Milling: A Superior Nanotechnological Tool for Fabrication
احصل على السعر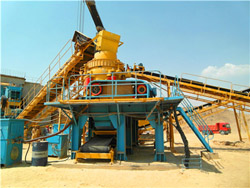
Direct Mechanocatalysis: Using Milling Balls as
In direct mechanocatalysis this rule is generally followed in planetary ball mills. 6, 21b, 26 The reactions in vibratory ball mills, however, usually only use one or two balls. 13. Another interesting point is the Fundamentally, a ball mill comprises a vessel or vial filled with balls, or rods, constructed from a variety of materials such as ceramic, agate, silicon nitride, sintered corundum, zirconia, chrome steel, Cr–Ni steel, tungsten carbide or plastic polyamide (Fig. 2). The material to be milled is placed inside the vessel, which is made toOverview of milling techniques for improving the solubility
احصل على السعر
Ball Mill Principle, Construction, Working, and More Soln
A pharmaceutical ball mill is a type of grinder used to grind and blend materials while manufacturing various dosage forms. The size reduction is done by impact as the balls drop from near the top of the shell. Ball mills are used primarily for single-stage fine grinding, regrinding, and as the second stage in two-stage grinding circuits.The ball mill used was a XQXM-2 planetary ball mill. A consistent ratio of 10:1 for the ball material was upheld during the ball milling process, and a grinding speed of 200 r/min was sustained. The grinding periods were differentiated, with durations set at 2 h, 4 h, 6 h, 8 h, 10 h, and 12 h, respectively.Materials Free Full-Text Effect of Ball Milling Time on the
احصل على السعر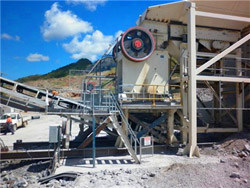
Wet milling Particle Technology Academic library
This mill consists of a cylindrical vessel, usually arranged with its axis vertical, that is completely filled (merely indicated in Fig. 4.34) with sand grains, steel balls, steatite balls or similar grinding media with dimensions ranging from a few tenths of a millimetre up to several millimetres. A stirrer is installed in the axis.The ball milling method is classified as vibration mill, planetary mill and magneto-ball mill depending on the movement of the balls and vessel and among them, the planetary mill is the most common as it has been used to reduce the particle size of many materials. The ball milling process induces a reduction in the particle and crystallite sizeBall milling A green and sustainable technique for the preparation
احصل على السعر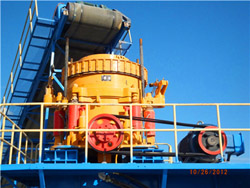
Ball Mill RETSCH powerful grinding and homogenization
Ball mills are among the most variable and effective tools when it comes to size reduction of hard, brittle or fibrous materials. The variety of grinding modes, usable volumes and available grinding tool materials make ball mills the perfect match for a vast range of applications. Cooling, heating & cryogenic grinding.A ball mill, which is used to finely grind materials, causes high levels of vibration and sound during grinding operations. The vibration and sound of mills provide significant information about the internal conditions and can be used to estimate the status of the ground material. We developed a simulation model for the vibration of a mill wallVibration characteristics of an operating ball mill IOPscience
احصل على السعر
AMIT 135: Lesson 7 Ball Mills & Circuits Mining Mill
Liners can be made of manganese steel, Ni hard or high carbon steel and hard rubber or synthetic material that is 65 75 mm thick. The liners can be: Smooth; Ribbed; Waved; For wet ball mills, Bond expressed power draw as a function of the total mass of media:P↓M / M↓B 15.6Φ↓V (1 0.937 J↓B)
احصل على السعر