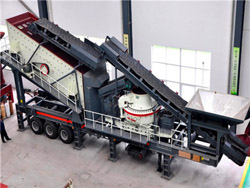
(PDF) Grinding in Ball Mills: Modeling and Process
The paper presents an overview of the current methodology and practice in modeling and control of the grinding process in industrial Despite the fact that ball milling is an efficient operation, it is energy intensive, and its modeling is a great challenge. In the present experimental study, efforts Modeling of Bauxite Ore Wet Milling for the Improvement of
احصل على السعر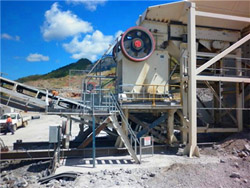
A method to identify wet ball mill’s load based on
A ball mill is a type of heavy mechanical equipment that relies on its own rotation to drive the steel balls inside to impact and grind materials with high reliability. Tumbling ball mills or ball mills are most widely used in both wet and dry systems, in batch and continuous operations, and on small and large scales. Grinding elements in ball mills Ball Mill an overview ScienceDirect Topics
احصل على السعر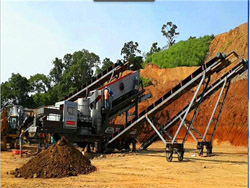
Ball Grinding Process SpringerLink
Ball grinding can be carried out in either dry-operation or wet-operation. The former is widely used in coal-fired power plants and cement industry, and the latter is of the impact of a ball during the "cascade" condition of operating a ball mill by the dry and wet methods. Calculations were made for a ball mill with a diameter of The effectiveness of wet milling materials in ball mills
احصل على السعر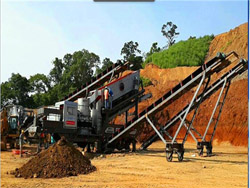
AMIT 135: Lesson 7 Ball Mills & Circuits Mining
Explain the role of ball mill in mineral industry and why it is extensively used. Describe different types of ball mill design. Describe the components of ball mill. Explain their understanding of ball mill operation. Explain the role of Kotake et al. [33] demonstrated that the product size and width of a quartz particle size distribution produced by ball milling were minimal in wet grinding with small Wet and dry grinding of coal in a laboratory-scale ball mill: Particle
احصل على السعر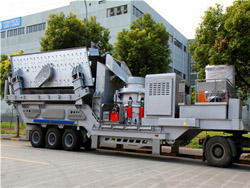
Wet ball milling of niobium by using ethanol, determination
Abstract This study investigates the effect of using ethanol as the process control agent during the wet ball milling of niobium (Nb). Dried nanocrystal Nb powders, The effect of ball mill on the morphological and structural features of cellulose has been described by Okajima and co-workers. 20 They treated microcrystalline cellulose derived from cotton linters in a planetary ball Ball milling: a green technology for the
احصل على السعر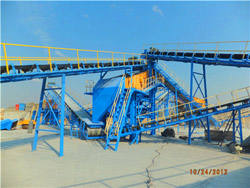
Ball Milling in Organic Synthesis: Solutions and Challanges
Type of ball mill: • There is no fundamental restriction to the type of ball mill used for organic synthesis (planetary ball mill, mixer ball mill, vibration ball mill, ). • The scale of reaction determines the size and the type of ball mill. • Vessels for laboratory vibration ball mills are normally restricted to a volume of 50 cm3.The balls occupied 28% of the mill volume. The mill was rotated at 65% of the critical speed. The work index of the ore was 11.3 kWh/t. Estimate the size of the mill required. 7.7. A wet overflow ball mill of dimensions 3.05 m × 3.05 m was charged with nickel ore (pentlandite) of density 4.2 having a F 80 value of 2.2 mm. The mass of ballsTubular Ball Mills ScienceDirect
احصل على السعر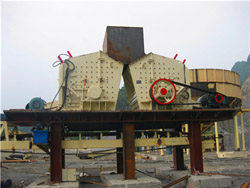
Effects of filling degree and viscosity of slurry on mill load
A transparent mill (552 × 180 mm), made of Perspex material and filled with 10 mm balls, was used for the tests. Ball filling and mill fractional speed were kept constant respectively at 20% and 60% while slurry filling was varied from 0% to 300%. Using a high speed video camera, the motion of the charge was captured.Despite the fact that ball milling is an efficient operation, it is energy intensive, and its modeling is a great challenge. In the present experimental study, efforts are made to model wet milling of bauxite ores and identify the optimum material filling volume in the ball mill.Modeling of Bauxite Ore Wet Milling for the Improvement of
احصل على السعر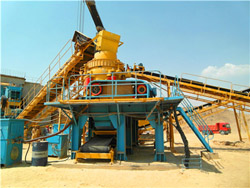
Ball Mill Operation -Grinding Circuit Startup & Shutdown Procedure
Normal Shutdown Sequence of Ball Mill and Grinding Circuit. Shut off cyanide metering pump. Put weight controller into MANUAL mode and turn controller output to 0%. Run the ball mill for 15-30 minutes. Put density controller into MANUAL mode, set output to 0%. Put flow controller into MANUAL mode and set output to 0%.A ball mill is important grinding equipment in a concentrator, and the accurate detection of the load status ensures that the ball mill runs in the best state, which helps optimize the grinding process, ensure the stable operation of the ball mill equipment, and save energy. The current mainstream detection methods cannot easily detect the Ball mill load status identification method based on the
احصل على السعر
Predicting the effect of operating and design variables in
The clearance between the stirrer and mill floor was set to 8 mm to prevent media locking during mill operation. The base-case mill diameter (D t) was 380 mm. Download : Download high-res image (188KB) Download : Download full-size image; Fig. 1. 3-D geometric representation of a laboratory-scale stirred mill used as the base case in The process parameters used for these experiments of a typical industrial wet ball mill is specified in the Table 1. (a) (b) Fig. 1(a), (b); Position of accelerometer sensors on industrial Ball mill 219 Satish Mohanty et al. / Procedia Computer Science 58 ( 2015 ) 217 – 224 Table 1.Vibration Feature Extraction and Analysis of Industrial Ball Mill
احصل على السعر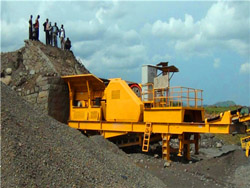
What is a wet overflow ball mill and its applications LinkedIn
A wet ball mill is a type of grinder used to grind and blend materials for use in mineral dressing processes, paints, pyrotechnics, ceramics, and selective laser sintering.1. Introduction. Grinding operation is used extensively in the industry of beneficiation, metallurgy, chemical engineering, and electric power. Assisted by the impact and abrasion between media (steel ball, steel rod, gravel, ceramic ball) and ore, the grinding operation reduces the particle size in the mill [[1], [2], [3]].To produce the qualified size An innovative approach for determining the grinding
احصل على السعر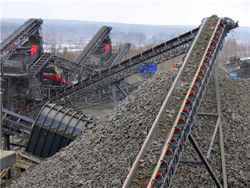
Experimental investigations and modelling of the ball
Planetary ball mills feature attractive properties, like the possibility of dry or wet operation, straightforward handling, cleanability and moderate costs. Consequently they are very well suited for lab scale process development in diverse industries, including pharmaceuticals and new materials. A number of questions still remain unansweredBall grinding can be carried out in either dry-operation or wet-operation. The former is widely used in coal-fired power plants and cement industry, and the latter is widely used in metal and nonmetal mines. There are three types of mills used: grate ball mill, overflow ball mill, and peripheral discharge ball mill.Ball Grinding Process SpringerLink
احصل على السعر
Rod Mill SpringerLink
The rod mill can be used for both dry and wet operation, and peripheral discharge can also be used for wet grinding. Overflow Rod Mill. Ore discharge refers to the rod mill that the ore is discharged by the ore pulp itself. Unlike the overflow ball mill, which has no neck of hollow shaft at the discharge port, instead, it has a wide apertureMilling is used across a number of different industries and can be broadly divided into two types: wet milling and dry milling. When it comes to the manufacturing of pharmaceuticals, the particle size of ingredients is critical to a drug’s performance and efficacy, so the stakes are much higher than when milling foods or other consumer Wet Milling vs. Dry Milling in the Pharmaceutical Industry
احصل على السعر
The working principle of ball mill Meetyou Carbide
22 May, 2019. The ball mill consists of a metal cylinder and a ball. The working principle is that when the cylinder is rotated, the grinding body (ball) and the object to be polished (material) installed in the cylinder are rotated by the cylinder under the action of friction and centrifugal force. At a certain height, it will automaticallyIn the continuous mode of wet grinding operation, the amount of the particulate material present in the mill, commonly known as the hold-up weight, varies with the breakage properties, feed rate, and size distribution of the particulate material, the solid-water ratio in the feed, particle shape and surface charge, viscosity of the slurry present Slurry density effects on ball milling in a laboratory ball mill
احصل على السعر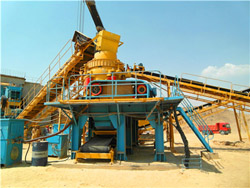
Optimization of continuous ball mills used for finish-grinding
The mill discharge had a fineness of about 1800 cm 2 /g and the material which enters the second compartment had only a. Description of the plant. The flow-sheet of the semi-industrial plant is shown in Fig. 2. Fresh feed and separator grits were combined and fed to the mill. The ball mill has an inside diameter (inside liners) of 0.72 m.This study investigates the effect of using ethanol as the process control agent during the wet ball milling of niobium (Nb). Dried nanocrystal Nb powders, of high purity, with particle sizesWet ball milling of niobium by using ethanol, determination
احصل على السعر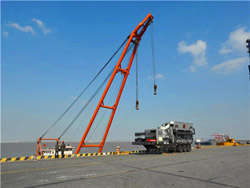
Grinding in Ball Mills: Modeling and Process Control
• speed of rotation of the mill; • slurry density in case of wet grinding operation. Quantitative estimations of these parameters can be found in [4, 5, 23]. An important characteristic of an industrial ball mill is its production capacity which is measured in tons of production per hour. The production capacity depends
احصل على السعر