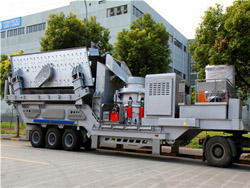
CO2 Emission Reduction in Blast Furnaces
The blast furnace is a countercurrent reactor in which the reducing gas is produced by coke carbon gasification with the oxygen of In a blast furnace process, this means a cohesive zone located higher in the vertical direction when using fluxed pellets; this leads to a lower amount of direct Effect of adding limestone on the metallurgical
احصل على السعر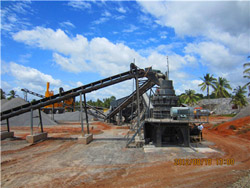
On the use of caustic lime, instead of limestone, in blast furnaces
The quantity of coke thus uselessly consumed is very considerable, as the following calculation, deduced from the actual present working at Ougree, will plainly show : - A First Online: 14 May 2023 184 Accesses Part of the Lecture Notes in Mechanical Engineering book series (LNME) Abstract The higher production of steel lead to increase Blast Furnace Slag Cement Clinker Production Using Limestone-Hot Blast
احصل على السعر
Environmental impact analysis of blast furnace slag applied
Sensitivity analysis showed that the environmental impact of slag-based cement was sensitive to the consumption of limestone and energy, as well as allocation Iron ores, sinter or pellets, coke, and lime are introduced into the blast furnace from the top; the hot compressed air is fluxed from tuyeres at the lower section Chapter 4 Blast Furnace: Most Ef cient Technologies for
احصل على السعر
Production and High-Ratio Application of Iron Ore Pellets in
The proportion of pellets in the three 5500 m 3 blast furnaces has increased from 28 to 55%, the blast furnace slag volume has been reduced from 280 to Wang et al. (2021) observed that the consumption of CH in cements with blast furnace slag and limestone filler occurred mainly between 28 and 91 days, which explains the long-term strength development. The Frontiers Environmental and Mechanical
احصل على السعر
Effect of Finely Ground Limestone and Dolomite on
Pellets, as one of the iron-bearing burdens of blast furnaces, present many advantages, including excellent metallurgical performance, low energy consumption in the production The reducibility of the pellets under unconstrained conditions was tested with a hightemperature furnace called a BFS (Blast Furnace Simulator), which has been previously used to investigate theEffect of Adding Limestone on the Metallurgical
احصل على السعر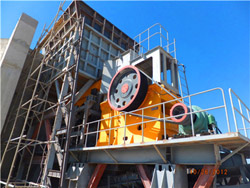
Modeling and Optimization of Biochar Injection
Most modern blast furnaces (BFs) operate with Pulverized Coal Injection (PCI), but renewable and carbon neutral biochar could be applied to reduce the fossil CO2 emission in the short term. In the 4 Blast furnace fuel consumption data for most countries in the post-World War II period is summarized in the British Iron and Steel Federation, Statistical Handbook, 1964, volumes I and II. Earlier data is readily available in the statistical year book or mineral statistics of the country concerned. 32 In general, limestone consumption wasThe Peculiar Productivity History of American Blast Furnaces,
احصل على السعر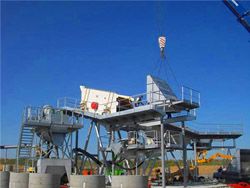
(PDF) Sintering and Briquetting Synergy in Blast Furnace
In blast-furnace smelting, the yield of low-sulfur (<0.02%) hot metal is increased from 65–70 to 85.1% and the furnace productivity from 2.17–2.20 to 2.27 t/(m3 day); coke consumption isThe article describes the concept of partially replacing the sinter in a blast furnace charge with extrusion briquettes to form the basis for sintering and briquetting synergy. The comparability criteria for sinter and extrusion briquette (brex) properties and production parameters were analyzed along with a substantiation of the fundamental Sintering and Briquetting Synergy in Blast Furnace Smelting
احصل على السعر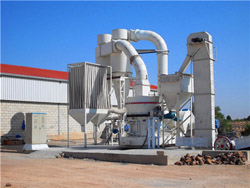
Software for the Raw-Materials Management System in Blast-Furnace
A description is presented of an information-modeling system developed to help optimize the composition of the charge materials and fluxes in sintering and blast-furnace smelting. The system is based on models that provide for end-to-end accounting of the sintering-machine and blast-furnace charges, calculate the technical-economic The calculation was carried out for blast-furnace production with a total furnace volume of 4520 m 3 at the same air-blast temperature (1100°С), oxygen concentration in the blast (24.96%) and blast furnace gas pressure (0.93 GA); natural gas consumption and slag losses were also taken equal in all cases.Improvement of Technical and Economic Performance of Blast-Furnace
احصل على السعر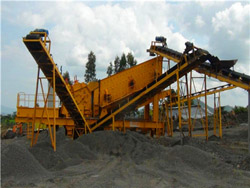
Role of Ferrous Raw Materials in the Energy Efficiency of
Steelmaking accounts for circa 7% of anthropogenic CO 2 emissions worldwide. 1) The integrated steelmaking route (blast furnace, BF basic oxygen furnace, BOF) is the dominate production method. It is energy intensive with typical energy consumption figures on the order of 16–21 GJ/t crude steel with the value highly depend on system boundary However, human toxicity potential increased by 9%, mainly due to the poor grindability of blast furnace slag that resulted in an increase of electricity consumption in cement grinding process. Blast furnace slag utilization can also prevent a series of environmental problems caused by its storage and reduced land use area by 22% Environmental impact analysis of blast furnace slag applied
احصل على السعر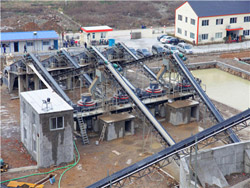
Coke Consumption an overview ScienceDirect Topics
Consumption of reducing agents and fuel in German blast furnace ironmaking [ 35 ]. It can be seen that in 1950s only coke was used for blast furnace process, and coke consumption was as high as 950 kg/THM. Along the technology development, the coke consumption has been reduced to 500–550 kg/THM during 1970s.The comparatively low blast consumption is associated with optimum pressure drop and stabIe furnace operation. Operational indices of blast furnace No. 1 are presented in the table. Foundry iron is smelted solely on the basis of self-fluxing sinter almost without any addition of limestone to the blast furnace burden. As early as 1955Operation of blast furnaces at high top pressure Springer
احصل على السعر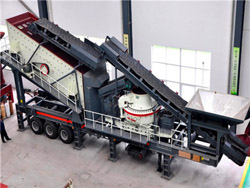
Ladle-Furnace-Slag Reprocessing at Evraz Nizhnii Tagil Iron
Ladle furnaces at Evraz Nizhnii Tagil Iron and Steel Works OJSC produce over 90,000 metric tons of slag per year. As this slag cools, it turns into a fine-grained powder; if the powder cannot be sold, it is temporarily stored until it can be disposed of [1]. We have considered producing easily used flux sinter from the slag generated during A high share of gaseous reduction leads to less FeO in the primary slag melt and to lower direct reduction rates, resulting in decreased coke consumption in the blast furnace process. In addition to high softening and melting temperatures, good high-temperature properties of iron-bearing burden materials can be specified as a narrow Effect of adding limestone on the metallurgical
احصل على السعر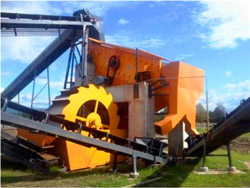
Steel Production American Iron and Steel Institute
The blast furnace is the first step in producing steel from iron oxides. The first blast furnaces appeared in the 14th century and produced one ton per day. Even though equipment is improved and higher production rates can be achieved, the processes inside the blast furnace remain the same. The blast furnace uses coke, iron ore and limestone toThe input requirements for 16th century blast furnaces were large. Though fuel consumption had fallen to roughly the level of the bloomery furnace (initially it used much more fuel than a bloomery), producing a ton of pig iron still required roughly 4.5-5 tons of charcoal, and 5.5-7 tons of iron ore.The Blast Furnace: 800 Years of Technology Improvement
احصل على السعر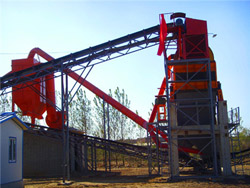
Chapter 4 Blast Furnace: Most Ef cient Technologies for
Iron oxides are reduced in the blast furnace (Fig. 4.1), and the resulting material is melted. Blast furnaces capacity is 100–5000 m3 covering the 70% of the global steel production. Iron ores, sinter or pellets, coke, and lime are introduced into the blast furnace from the top; the hot compressed air is fluxed from tuyeres at the lowerThese are substituting or mixing limestone with coal fly ash and blast furnace slag and, secondly, employing carbon capture and storage (Shah, 2021) or CO2 Looping and Recovery (Jiang, et alAn environment-friendly process for limestone
احصل على السعر
Study on the Appropriate Production Parameters of a Gas-injection Blast
The change regulations of the smelting parameters in a gas-injection blast furnace are investigated using theoretical calculations. The results show that when the volume of gas injected, the oxygen enrichment rate and the theoretical combustion temperature of tuyere are 600 m 3 /tHM, 10% and 1950~2200 ∘ C, respectively, the conditions meet the Abstract. As a promising method to strengthen the blast furnace smelting and to realize reduced fuel operation, high-proportion pellet charging has become the practice of BF ironmaking. Use of(PDF) Blast Furnace Performance Under Varying Pellet Proportion
احصل على السعر