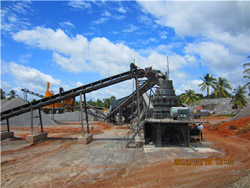
Modelling and optimization of material flows in the wood pellet
To address the knowledge gap in the short-term planning of biomass SCs, this paper develops a two-stage decomposition procedure for optimizing raw material The research material consisted of uncontaminated oak (Quercus spp.) wood particles. The tested material had a moisture content ranging from 8.8% to 11.4% and a density of 210.7 ± 1.79 kg/m3.Typical pelleting process flow for wood and baled
احصل على السعر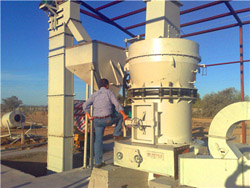
Pellet mill design Feed Strategy
When considering at pellet mill design, there are some important aspects to study to achieve maximum efficiency of the machine. Maximum efficiency is defined as the ideal The flow of materials and interdependency between the processes inside the pellet mill are modeled using the discrete-rate approach [27]. The model verification A simulation model for the design and analysis of wood
احصل على السعر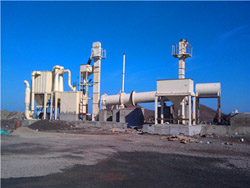
From wood chips to pellets to milled pellets: The
The process flow for pelletizing wood at the pellet plant is the same as shown in Fig. 1. First, the fresh wood chips underwent coarse milling in a semi-industrial The raw material used generated pellets with eucalyptus and soybean wastes mixed in different proportions, as well was done for sugarcane bagasse and soybean wastes.Wood pellet production process flow and energy
احصل على السعر
Wood pellet milling tests in a suspension-fired power plant
This paper investigates the milling behavior of two industrial wood pellet qualities (designated I1 and I2 as per ISO 17225-2:2014) in large-scale coal roller mills, Abstract. In this chapter the essential equipment in pellet production is reviewed step by step. A general scheme is represented and detailed discussion about Wood Pellet Production Process SpringerLink
احصل على السعر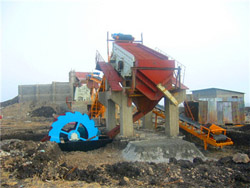
Production and utilization of fuel pellets from biomass: A
The paper presents a state-of-the-art review on production and utilization of fuel pellets from biomass. This includes different aspects of pellet making process usually fitted with a flow switch which turns the pellet mill off if there is no flow to the bearings. There is also a pressure-relief device in the system that is normally set to operate at approximately 4 Bar. Figure 3-2. Circuit lube system in a gear-driven pellet mill. Lubrication Gear-driven pellet mills are now fitted withPellet mill design Feed Strategy
احصل على السعر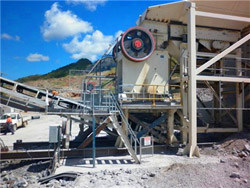
Comparative Study of the Properties of Wood Flour
Similarly, the other application of mill residues can be as a source of raw material for manufacturing pellets. Sources of raw materials for wood pellets include fallen branches, thinning and broken stems A pellet mill is a forming device. It has to be robust, take a beating, and densify what’s presented to it. It’s not magic. That’s the concept of the engineered biofuel.”. Biomass Pellet. Plugging the press is a line that is approached at virtually all times when making wood pellets, Kessler says. “You need to generate enoughIn-depth Knowledge Mining of Biomass Pellet Production Line
احصل على السعر
Modelling and optimization of material flows in the wood pellet
Pellet producers are forced to optimize the material flows along the whole supply chain (SC) to keep their products competitive against traditional energy sources. The SC concept is widely used as an effective approach in decision-making and planning for highly complex industries [7]. The efficient management of material flows across any SCSimilarly, the other application of mill residues can be as a source of raw material for manufacturing pellets. Sources of raw materials for wood pellets include fallen branches, thinning and broken stems from the forest, and residues generated in sawmills such as sawdust, chips, etc. Wood pellets are 0.5–3 cm long and cylindrical Comparative Study of the Properties of Wood Flour and Wood Pellets
احصل على السعر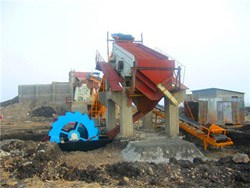
Working Principle of Pellet Mill and Pellet Plant
Pellets will leave the pellet mill at temperatures as high as 80 to 90 degrees centigrade and moisture contents are high as 17-18%. For proper storage and handling of the pellets, their moisture content must be reduced to 10-12% and their temperature to about 5 degrees higher than the atmospheric temperature.Slower speeds, however, may be necessitated by quality concerns with cubes or from high die discharge rates resulting in pellet collision with the interior walls of the pellet mill chamber. Leaver (1988) suggested a peripheral die speed of 610 m/min as the optimum speed for pellets ranging from 3.2 to 6.4 mm in diameter, while reduced Effects of conditioning temperature and pellet mill die speed on pellet
احصل على السعر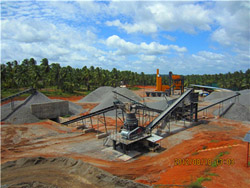
Wood Pellet Production Process SpringerLink
In pellet mill raw material is fed into the die through a hopper and feed distributors are responsible for uniform distribution of the material across the face of the die. The rolls force the material through holes in the die and a series of cut-off knives, equipped on the swing cover, cut the pellets as they are coming out from the die and finally the Rough sieve (30 mm square holes) + metal trap, 3) Rough sieve bypass flow, 4) Hammer mill (Miller 20), 5) wood-based pellets, when raw material was aged at least 3 months,Additives in wood pellet production ResearchGate
احصل على السعر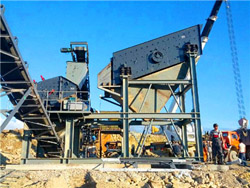
Comparative Study of the Properties of Wood Flour and Wood Pellets
The moisture content of the mill residues, hammer mill grindings and screened wood flour, as well as of the wood pellets, was determined for each species. The American Society of Testing and Materials (ASTM) Standard D4442–20 Standard Test Methods for Direct Moisture Content Measurement of Wood and Wood-Based Materials I’ve always been fascinated by the process of creating things from scratch. There’s a certain satisfaction that comes from taking raw materials and transforming them into something useful and efficient. That’s why I decided to delve into the world of wood pellet mills. In this article, I’ll guide you through the step-by-step process of making []How to Make Wood Pellet Mill Best Small Wood Stoves
احصل على السعر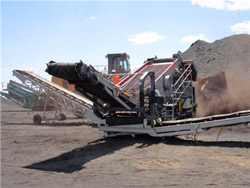
From wood chips to pellets to milled pellets: The mechanical
Section snippets Wood chip preparation. About 50-year-old European beech (Fagus sylvatica) trees and ca. 40-year-old Austrian pine (Pinus nigra) trees from Central Zealand (Denmark) were used in this work.The composition of the raw lignocellulosic materials was analyzed according to the standard analytical procedures provided by the large pellet production line. Large pellet production line refers to a complete biomass pellet mill plant with a production capacity of more than 1ton/h.GEMCO, with at least 20 years of experiences in biomass Large Pellet Production Line for Biomass, Wood, EFB, etc
احصل على السعر
Size, shape and flow characterization of ground wood chip
@article{osti_1328338, title = {Size, shape and flow characterization of ground wood chip and ground wood pellet particles}, author = {Rezaei, Hamid and Lim, C. Jim and Lau, Anthony and Sokhansanj, Shahab}, abstractNote = {Size, shape and density of biomass particles influence their transportation, fluidization, rates of drying and thermal pellet mill production facilities. For these reasons, the export market for wood pellets does not currently look as promising as the domestic market. Challenges Forces competing with pellet mill development The wood pellet industry in rural Washington faces a variety of competitive forces, including: • Cheap and plentiful oil and natural gas,Developing a Wood Pellet/ Densified Biomass Industry in
احصل على السعر
How To Make Wood Pellets --- Wood Pellet Manufacture Steps
Grinding. Grinding is also a size reduction step to make wood pellet, it is a necessary step for both large and small pellet plants. During the grinding process, the raw materials will be fed into a hammer mill which will grind the raw materials into smaller pieces with a diameter under 5mm.But the hammer mill can only process the wood raw @article{osti_1328338, title = {Size, shape and flow characterization of ground wood chip and ground wood pellet particles}, author = {Rezaei, Hamid and Lim, C. Jim and Lau, Anthony and Sokhansanj, Shahab}, abstractNote = {Size, shape and density of biomass particles influence their transportation, fluidization, rates of drying and thermal Size, shape and flow characterization of ground wood chip
احصل على السعر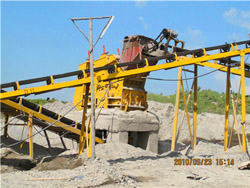
Process control variables, instrumentation and automation of
through the compression of the pellet mill die. The process holds or binds the ingredients together, and as the feed is cooled and dried, the softened materials harden in the pellet. The amount of steam added to the feed is typically controlled by monitoring the temperature of the conditioned mash just before it enters the pellet millIn this study, the technoeconomic feasibility of bioenergy production from sawdust under four different case scenarios is simulated and compared. These scenarios include: (1) heat and electricity generation from raw sawdust; (2) pellet production from sawdust; (3) and (4) integrated biorefinery approach for the simultaneous manufacturing Technoeconomic Feasibility of Bioenergy Production from Wood
احصل على السعر
Design and Construction of a Feeding System for a Pellet Mill
Figure 1. Diagram of Pellet Mill Operation (Hara, 2004). The goal of this project is to develop a surge hopper for material entering the pellet mill along with looking at possible ways to load it. In order to figure out the hopper design certain flow properties of chicken litter must be examined.
احصل على السعر