
Mill Critical Speed Formula Derivation Grinding & Classification
The formula to calculate critical speed is given below. N c = 42.305 /sqt(D-d) N c = critical speed of the mill. D = mill diameter specified in meters. d = diameter of the ball. In This work elucidates the efficient and low-cost approach for mass production of high-quality graphene (50g scale batch) through dual-drive planetary ball milling of graphite with the RSC Advances RSC Publishing
احصل على السعر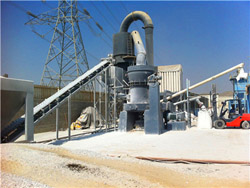
Efficient preparation and characterization of graphene
The optimum process and material composition of graphene prepared by ball milling are: flake graphite (50 mesh) 20 g, ball milling time 5 h, ball milling speed 410 r/min, aluminum particle diameter To examine the dependence of critical rotation speed on ball-containing fraction, we measured critical speeds at various ball-containing fractions from 0.3 to Critical rotation speed for ball-milling ScienceDirect
احصل على السعر
Effects of Ball Size Distribution and Mill Speed and Their
Read this article. A comprehensive investigation was conducted to delineate the effect of ball size distribution, mill speed, and their interactions on power draw, The critical rotation speed was re-examined at first in our previous paper, we showed experimentally that the critical rotation speed depends on ball-containing Critical rotation speed for ball-milling ScienceDirect
احصل على السعر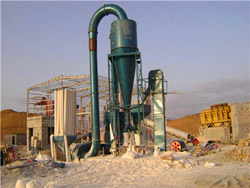
Recommended Ball Mill Speed & Liner
Nc = 42.3/√D (meters) or Nc = 76.63/√D (feet) In practical terms, one must assume some mill diameter, usually about 150 mm (6 inches) less than the mill inside shell or nominal diameter, that allows for The raw materials were ground from the big particle size to the smallest possible by using multistep grinding. In the laboratory, the common method to be used as the ball mill. This work aims to design a simple horizontal ball mill. Calcium carbonate material from limestone and eggshells powder was ground using the developed ball mill.The design and optimization process of ball mill to reduce particle
احصل على السعر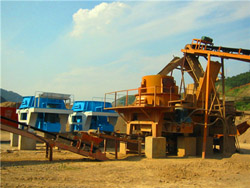
Efficient preparation and characterization of graphene based on ball
The prepared products were characterized by X-ray diffractometer, automatic specific surface area and porosity analyzer, and laser confocal Raman spectrometer. The results indicate that using aluminum powder as a grinding aid can significantly improve the efficiency of ball milling, the specific surface area of graphene A Slice Mill is the same diameter as the production mill but shorter in length. Request Price Quote. Click to request a ball mill quote online or call 630-350-3012 to speak with an expert at Paul O. Abbe® to help you determine which design and size ball mill would be best for your process. See our Size Reduction Options.Variables in Ball Mill Operation Paul O. Abbe®
احصل على السعر
Assessment of the Performance of Grinding Circuit for Buzwagi Gold Mine
The ball mill performance was poor and could be indicated by only 5-9 Assessment of the Performance of Grinding Circuit for Buzwagi Gold Mine. 145. Critical speed in % 75. 75. Ball size inCritical Speed and a Grinding Ball. For the ball mill to work properly, it must reach critical speed. This is the speed at which the grinding balls start to spin along the ball mills’ interior walls. If the ball mill does not reach critical speed, the grinding balls will stay at the bottom. They won’t be able to grind the material properly.Grinding ball Magotteaux
احصل على السعر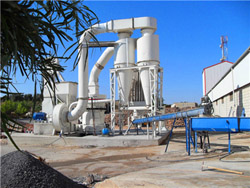
Ball Mill Working Principle, Construction, Application and
The length of the mill is approximately equal to its diameter. Principle of Ball Mill : Ball Mill Diagram. • The balls occupy about 30 to 50 percent of the volume of the mill. The diameter of ball used is/lies in between 12 mm and 125 mm. The optimum diameter is approximately proportional to the square root of the size of the feed.In this research, in order to find a suitable range for the number of lifters in the liner of ball mills, the DEM method is utilized. Initially, a pilot-scale ball mill with dimensions of 2.0 m ×Industrial SAG mill dimensions and speeds. ResearchGate
احصل على السعر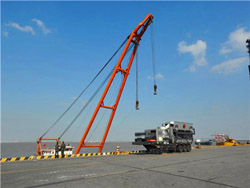
(PDF) Grinding Media in Ball Mills-A Review ResearchGate
One of the most used tumbling mills is the ball mill. This paper reviews different types of grinding media that have been developed and improved over the years and their properties. Also reviewedThe optimization of processing plants is one of the main concerns in the mining industry, since the comminution stage, a fundamental operation, accounts for up to 70% of total energy consumption. The aim Kinetics of Dry-Batch Grinding in a Laboratory-Scale
احصل على السعر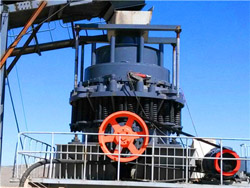
Autogenous and Semi-Autogenous Mills ScienceDirect
With time, as the hardness of the ore increases with depth in the mine, a second-stage ball mill is added. For larger sizes of ore (in excess of 10 mm), the breakage rate was lower for mills rotating at 55% of the critical speed than for mills running at 70% of the critical speed.D—the inner diameter of the ball mill, M; N0 critical speed of revolutions, r /min. When the non-smooth ball mill liner is used, the grinding ball filling ratio is 40-50%, and the grinding concentration is relatively large, the calculation result of the formula is relatively close to the actual one.The Ultimate Guide to Ball Mills Mining-pedia
احصل على السعر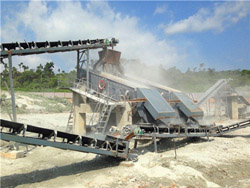
Study on Preparation and Characterization of Graphene Based on Ball
A graphene preparation method was proposed that considered vibration frequency, static filling rate, material-to-ball volume ratio, and the void percentages of media. Flake graphite, aluminumThe minus 152 mm (-6 in) product is conveyed onto a 29,940 Mt (33,000 st) crushed ore stockpile, reclaimed by three vibrating feeders, and then conveyed to the SAG feed chute at a targeted rate of 136 Mt/hr (150 st/hr). The control strategy for the SAG mill is fairly basic. Parameters which can be adjusted are feed tons per hour and mill Variable Speed SAG Mill 911 Metallurgist
احصل على السعر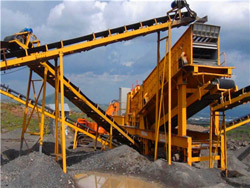
A Review of Alternative Procedures to the Bond Ball Mill Standard
Over the years, alternative procedures to the Bond grindability test have been proposed aiming to avoid the need for the standard mill or to reduce and simplify the grinding procedure. Some of them use the standard mill, while others are based on a non-standard mill or computation techniques. Therefore, papers targeting to propose a better A total of 120 t of Cristalino ore was prepared and sent to CIMM, where it was crushed and screened prior to grinding tests. The processing equipment included a 1.83 m (8′) diameter by 0.61 m (2′) length AG/SAG mill equipped with a 20 kW motor, a cone crusher, a 0.91 m (3′) diameter by 1.22 m (4′) length ball mill equipped with a 15 kWPre-Processing to Increase the Capacity of SAG Mill Circuits
احصل على السعر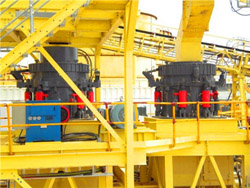
Energy Curve Enhancement Blog 7: Including grinding media
Different types of mills were contained in this dataset including: run of mine ball mills, rod mills, pebble mills, composite (ball and pebble) mills and ball mills. Figure 3 shows the distribution of media consumption in the modern Energy Curve database is shown alongside the historical data from ball mills alone.Northern Graphite, for example, has owned Bissett Creek since 2012, and the mine is not yet operational. Wilkinson said the average mining project typically takes around 12 to 15 years but "that'sCanada is sitting on a critical minerals mother lode. But is it ready
احصل على السعر
AMIT 135: Lesson 8 Rod Mills Mining Mill Operator Training
Typically R = 8. Rod Mill Charge: Typically 45% of internal volume; 35% 65% range. Bed porosity typically 40%. Height of bed measured in the same way as ball mills. Bulk density of rods = 6.25 tons/m3. In wet grinding, the solids concentration 1s typically 60% 75% by mass. A rod in situ and a cutaway of a rod mill interior.
احصل على السعر