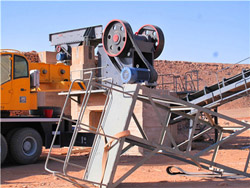
Introduction: Overview of the global iron ore industry
Introduction 1.1.1. World steel and iron ore production Steel is vital to the global economy. Its unique combination of strength, formability, versatility, recyclability, and low cost make it an ideal material for construction, transportation, machinery, and other Abstract: The preprocessing part of an iron ore mining production line is being modelled, together with description of the algorithms for its optimization with respect to criteria and Optimizing the automation of an iron ore production line — A
احصل على السعر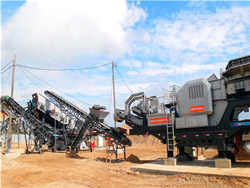
Optimizing the automation of an iron ore production line
PDF The preprocessing part of an iron ore mining production line is being modelled, together with description of the algorithms for its optimization Find, This review focussed on two main aspects of oolitic iron ore processing: beneficiation by conventional mineral processing techniques (differential grinding, scrubbing, gravity Iron Ore Processing an overview ScienceDirect Topics
احصل على السعر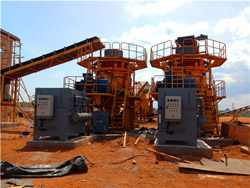
(PDF) Effective Processing of the Iron Ores
Effective technology for a complex wasteless processing of the iron ores has been designed and includes three main components (plats): comminution plant, briquette plant, pigment plant. The...Making iron and steel from iron ore requires a long process of mining, crushing, separating, concentrating, mixing, agglomeration (sintering and pelletizing), Iron Ore Processing, General SpringerLink
احصل على السعر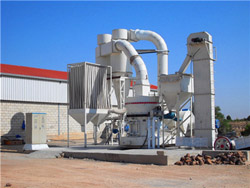
Iron Ore Pelletizing Process: An Overview IntechOpen
The use of iron ores with smaller crystal size and less dense structure usually results in pellets with better reducibility, impacting the performance of ironmaking reactors. Therefore, different iron ores Effective technology for a complex wasteless processing of the iron ores has been designed and includes three main components (plats): comminution plant, briquette Effective Processing of the Iron Ores
احصل على السعر
8 Developments in iron ore comminution and
This chapter reviews current iron ore comminution and classification technologies and presents some examples of flowsheets from existing operations. New Abstract and Figures. Sintering is an agglomeration process that fuses iron ore fines, fluxes, recycled products, slag-forming elements and coke. The purpose of sintering is to obtain a productIron Ore Sintering: Raw Materials and Granulation
احصل على السعر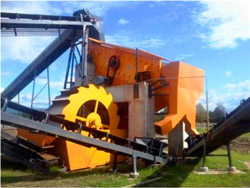
Iron Geoscience Australia
About 98% of world iron ore production is used to make iron in the form of steel. Iron in cast form has many specific uses (e.g. pipes, fittings, engine blocks) but pure iron is quite soft. Adding a small Iron- and steelmaking is the largest single industrial CO 2 emitter, accounting for 6.5% of all CO 2 emissions on the planet. This fact challenges the current technologies to achieve carbon-lean steel production and to align with the requirement of a drastic reduction of 80% in all CO 2 emissions by around 2050. Thus, alternative Sustainable steel through hydrogen plasma reduction of iron ore
احصل على السعر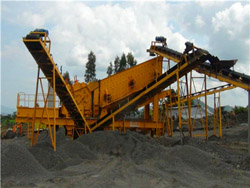
Steeling ourselves: How Australia can support the transition to net
More than ninety per cent of Australia’s current iron ore exports are mined from the deep red weathered Pilbara landscape in Western Australia and over 70 per cent of this material is shipped to China, where it is made into iron in blast furnaces using coke manufactured from coal, then further processed into steel.. Australia mines almost half It is the process of separating commercially valuable minerals from their ores. Commonly, haul trucks transport the ore from open pits or underground operations to processing operations. Some oresThe Basics of How Ore Processing and Recovery Plants Work
احصل على السعر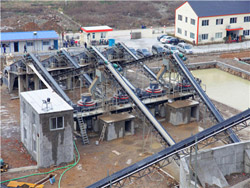
SciELO Brasil Evaluation of grinding circuits for iron ore
This industrial scale study compares two grinding circuits operating in an iron ore process with a production capacity of 12 million tons per year. The plant has three identical parallel lines, all fed from the same feed pile. Each line has an independent grinding circuit, with two ball mills and three hydrocyclones batteries.Here, the outline and characteristics of iron ore deposits are discussed. A reasonable definition of iron ore would be “ore that enables economical production of iron and steel reflecting the steelmaking technology in each era” (Inazumi 2009).Even if an iron ore has excellent quality and properties, it is merely a stone unless iron and steel can be Phosphorus in Steelmaking Processes SpringerLink
احصل على السعر
Limonite Processing Production Line, Iron Ore Dressing Plant Process
Under normal circumstances, the limonite beneficiation production line includes a crushing process, a screening process, a gravity beneficiation process, a dehydration process, etc. The crushing process usually uses a jaw crusher, a cone crusher, etc. The screening process adopts equipment such as circular vibrating Hematite, the main iron ore found in Brazilian mines Stockpiles of iron ore pellets like this one are used in steel production An illustration of iron ore being unloaded at docks in Toledo, Ohio. Iron ores are rocks and minerals from which metallic iron can be economically extracted. The ores are usually rich in iron oxides and vary in color from Iron ore
احصل على السعر
Influence of iron ore properties on dioxin emissions during iron ore
It is a thermal agglomeration process which blends iron ore fines, coke breeze and other additives, such as limestone, mill scale and recycled materials from downstream processes 7.The mill scale is a waste from the iron and steel industry. Due to the high content of iron in the form of oxides, it is an attractive material for the recovery of metallic iron by reduction. The product of mill scale reduction is an iron with a very extended surface and a high affinity for oxygen. The smaller iron particles are, the easier it is for Minerals Free Full-Text Recovery of Iron from Mill Scale by
احصل على السعر
(PDF) From Australian iron ore to green steel: the
In 2019, for instance, iron and steel production contributed 28% of global industrial CO₂ emissions (IEA, 2020a). Green steel-in which renewable sources feed direct energy consumption in theProduction planning decisions in the mining industry are affected by geological, geometallurgical, economic and operational information. However, the traditional approach to address this problem Stochastic Open-Pit Mine Production Scheduling: A
احصل على السعر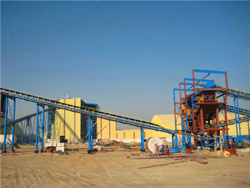
(PDF) Iron Ore Granulation for Sinter Production: Developments
Iron ore granulation is an indispensable process in the production of sinter that can influence and regulate the yield, efficiency and quality. Although a great deal of research has been done onmaterials Article Optimization of the Iron Ore Direct Reduction Process through Multiscale Process Modeling Rami Béchara 1,2, Hamzeh Hamadeh 1,2, Olivier Mirgaux 1,2 and Fabrice Patisson 1,2,* ID 1 Institut Jean Lamour, CNRS, Université de Lorraine, 54011 Nancy, France; [email protected] (R.B.); [email protected] Process through Multiscale Process Modeling
احصل على السعر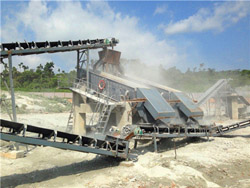
Rio Tinto’s BioIron™ proves successful for low-carbon iron-making
Development work was conducted in a small-scale pilot plant using batches of 1,000 golf ball-sized iron ore and biomass briquettes. Rio Tinto Chief Commercial Officer, Alf Barrios, said “Finding low-carbon solutions for iron and steelmaking is critical for the world as we tackle the challenges of climate change.Iron is currently produced by carbothermic reduction of oxide ores. This is a multiple-stage process that requires large-scale equipment and high capital investment, and produces large amounts of CO2. An alternative to carbothermic reduction is reduction using a hydrogen plasma, which comprises vibrationally excited molecular, atomic, and Hydrogen Plasma Processing of Iron Ore SpringerLink
احصل على السعر
Pressurized Chemical Looping for Direct Reduced Iron Production
To achieve net-zero iron and steel production by 2050, many iron and steel producers are turning to direct reduced iron (DRI)—electric arc furnace (EAF) steel production as an opportunity to achieve significant CO2 emissions reductions relative to current levels. However, additional innovations are required to close the gap between Sishen Mine in Northern Cape, was the largest iron ore-producing mine in South Africa, producing approximately 28 million tonnes of iron ore and an estimated 37.9 million metric tons per annum (mmtpa) of Run-of-Mine (ROM) in 2021. The Sishen Mine is owned by Anglo American Plc, and is due to operate until 2039. The second largest iron ore South Africa: Five Largest Iron Ore Mines in 2021 GlobalData
احصل على السعر
Cracking and Microstructure Transition of Iron Ore Containing
The phenomenon of cracking and deterioration of iron ore particles is a widespread scientific problem in the field of mineral processing and metallurgy. In this paper, the thermal decomposition properties of iron ore were investigated by a non-isothermal method using thermogravimetric equipment, and the crack evolution behavior
احصل على السعر