
Cost Analysis for Crushing and Screening Part II
Cost Analysis for Crushing and Screening Part II Development of a cost model for determination of the production cost for product fractions Johan Fägerlind Division of quality rock materials for demanding construc-tion projects, such as bridges. Crusher automation ensures consistent and effi cient operation. Improves productivity and Crushing and Screening Handbook AusIMM
احصل على السعر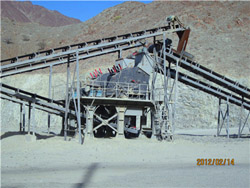
Aggregate Production Optimization in a Stone-Crushing
This research involves the optimization of aggregate production using the Taguchi approach to maximize the production rate of Gneiss stone. The L18 orthogonal Rock particles are modelled using the bonded particle model (BPM) and laboratory single particle breakage tests have been used for calibration. The industrial Cone crusher modelling and simulation using DEM
احصل على السعر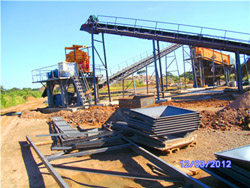
Optimization Capabilities for Crushing Plants Chalmers
a crushing plant operation consisting of rock size reduction (comminution) and particle size separation (classification) processes. The objective of the crushing plant operation for This paper presents a set of related methods for performing a computational geometry analysis of a cone crusher shape that provides geometric information for use A fundamental model of an industrial-scale jaw crusher
احصل على السعر
Performance optimization of jaw-type rock crushing machine
The results show that an external diameter/offset ratio within the average of 10:1 can be considered for the offset calculation of a jaw-type crusher shaft. The This paper commences with a brief introduction to LCA and presents the system boundaries, modeling and assumptions for the rock crusher study. System Life cycle assessment of a rock crusher ScienceDirect
احصل على السعر
Rock crusher production and operation cost analysis
Production cost analysis of rock crushers. Rock crushers are widely used in mining, quarrying, and other industrial applications to reduce the size of rocks. The production Abstract. The fragmentation rate and particle size distribution of the muckpile after blasting have important influences on the performance of subsequent mining activities such as loading, hauling, crushing, grinding, and the overall costs of the mine. Drilling and blasting are important steps in the chain of mining processes, and its resultsEvaluation of blast fragmentation effects on jaw crusher
احصل على السعر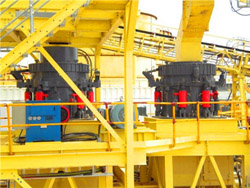
Influence of jaw crusher parameters on the quality of primary
The crusher was tested at several settings, and 11 mm was chosen because this was the setting which generated the most material in the 10–14 mm size range. 3. Results3.1. Crusher operation. When the crusher is fed at the high feed rate, the measured throughput can be characterised as the capacity of the crushing operation.Delaney et al. [17] and Cleary et al. [18] based on the DEM (discrete element method), the compression crushing of non-spherical rock is predicted by establishing an industrial grade cone crusherAnalysis of cone crusher performance with changes in material
احصل على السعر
Aggregate Production Optimization in a Stone-Crushing Plant
This research involves the optimization of aggregate production using the Taguchi approach to maximize the production rate of Gneiss stone. The L18 orthogonal array has been used to investigate how the CSS, throw, eccentric speed, and particle size affect the products of the cone of the crusher (its cumulative weight fraction). The CSS, The crusher product should have a top size of 50 mm. A blast fragmentation of <50 mm would improve the downstream operations and the crusher throughput. An investigation into the blasting practises was carried out to assess whether the downstream delays can be eliminated by improving the blast results.An investigation into the fragmentation of blasted rock at SciELO
احصل على السعر
Chamber Optimization for Comprehensive Improvement of Cone Crusher
This study aims to analyze the impact of key structural parameters such as the bottom angle of the mantle, the length of the parallel zone, and the eccentric angle on the productivity and product quality of the cone crusher and optimize the crushing chamber to improve the crusher performance. The amount of ore in the blockage layer was In this paper a cone crusher is modelled and simulated using DEM in the commercial software EDEM® provided by DEM-Solutions Ltd. Cone crushers and gyratory crushers have previously been the subject for DEM modelling and simulation. Lichter et al. (2009) successfully modelled a laboratory Nordberg B90 cone crusher.Cone crusher modelling and simulation using DEM ScienceDirect
احصل على السعر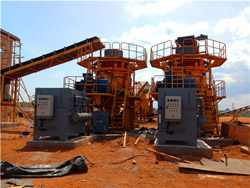
Optimization of Aggregate Production Circuit through Modeling
Optimization of Aggregate Production Circuit through Modeling of Crusher Operation Tomasz Gawenda and Daniel Saramak * Department of Environmental Engineering, Faculty of Civil Engineering and Resource Management, AGH University of Science and Technology, 30-059 Cracow, Poland; [email protected] * Correspondence: Achieving the optimum outputs from rock crushing operations depends upon detailed investigations on the rock crusher interactions (RCI). The RCI plays a crucial role in rock breakage success, where the crushing degree depends on the combinations of several factors, such as crusher performance, feeding method, and Investigating the effects of feeding properties on rock
احصل على السعر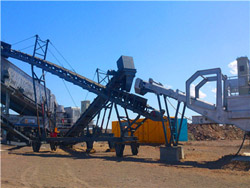
Crushing and Screening Handbook AusIMM
quality rock materials for demanding construc-tion projects, such as bridges. Crusher automation ensures consistent and effi cient operation. Improves productivity and product quality while reducing maintenance costs by preventing overload situations. Stationary conveyors a complete range of belt conveyors. Wide variety of widths, lengths,A modular framework for the implementation of optimization capabilities for crushing plants. Crushing plant for aggregates production consisting of two sub-processes [Paper B]. (a) SPV for varying(PDF) Optimization Capabilities for Crushing Plants ResearchGate
احصل على السعر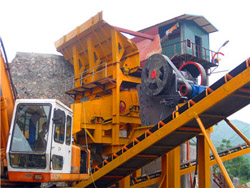
(PDF) Design and Construction of Rock Crushing
This paper describes the design and operation of a high-pressure shear cell (HPSC) capable of pressing granular material against candidate wear surfaces at macroscopic pressures of up to 700 MPa.Laboratory centrifugal vertical impact crusher: 1 is supply nozzle; 2 is housing cover; 3 is accelerator; 4 are acceleration ribs; 5 is armor; 6 is electric motor; 7 is V-belt transmission. Principle of laboratory crusher Before starting operation, the accelerator operation. installed in the crusher is rotated at a nominal or lower speed.Experimental study of crushing process of the crushed stone
احصل على السعر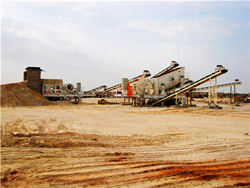
Geometric analysis of cone crusher liner shape ScienceDirect
This is most probably a consequence it being a complex three-dimensional process where the presence of the rock being crushed interacts with the crusher to determine performance. There have been many important contributions to better understanding of cone crusher operation and some of these will be briefly reviewed for The paper concerns investigation of the effect of impact crusher operation on selected qualitative The FP1 denotes yield of the finest particle size fractions, i.e., below 2 mm, that existed in individual crushing product. Feed analysis shows The effect of rock crusher and rock type on the aggregate shape. ConstrMinerals Free Full-Text Optimization of Aggregate Production
احصل على السعر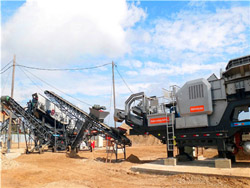
Evaluation and Risk Analysis of Open-Pit Mining Operations
Mining of raw materials is a process that consists of several stages. In open-pit mining, material with high compressive strength is extracted by drilling and blasting and material with low compressive strength is extracted by e. g. a bucket wheel excavator. Most important influencing factors for crusher decision are compressive strength, The paper concerns investigation of the effect of impact crusher operation on selected qualitative The FP1 denotes yield of the finest particle size fractions, i.e., below 2 mm, that existed in individual crushing product. Feed analysis shows The effect of rock crusher and rock type on the aggregate shape. ConstrMinerals Free Full-Text Optimization of Aggregate Production
احصل على السعر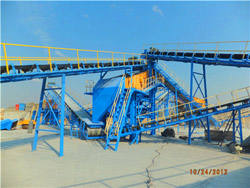
Optimisation of the swinging jaw design for a single toggle jaw crusher
The plate dimensions of the un-optimised jaw crusher were modelled using ANSYS Design Modeller 2021, as shown in Fig. 3.The load and boundary conditions for the static structural analysis were as shown in Fig. 4.Design of Experiments (DoE) was then conducted where the minimum and maximum values of the target parameters were Crusher. A crusher is a machine designed to reduce large rocks into smaller rocks, gravel, sand or rock dust. Crushers may be used to reduce the size, or change the form, of waste materials so they can be more easily disposed of or recycled, or to reduce the size of a solid mix of raw materials (as in rock ore ), so that pieces of differentCrusher
احصل على السعر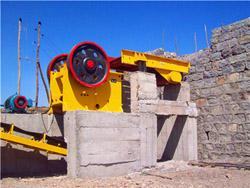
Crusher an overview ScienceDirect Topics
Roll Crushers. A. Gupta, D.S. Yan, in Mineral Processing Design and Operation, 2006 6.1.3 Roll Crusher Circuit Design. Roll crushers are generally not used as primary crushers for hard ores. Even for softer ores, like chalcocite and chalcopyrite they have been used as secondary crushers. Choke feeding is not advisable as it tends to produce particles of
احصل على السعر