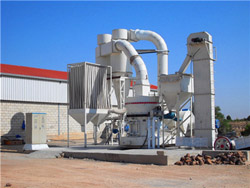
Refining crude oil the refining process U.S. Energy
All refineries have three basic steps: Separation Conversion Treatment Separation Modern separation involves piping crude oil through hot furnaces. The The term cracking comes from the process of breaking up long hydrocarbon molecules into smaller, more useful molecules. The cracking process converts heavy straight run API Refinery Processes
احصل على السعر
Impurity Distribution During Electrolytic Refining of Antimony
An electrolytic refining process is used in order to obtain antimony with an overall impurity content not above 0.1–0.3%. In this this case the complete scheme for comprehensive treatment of antimony raw material includes: flame refining of ferrous metal electrolysis in solutions, solution purification from accumulated impurities, and anode Antimony Refining Process Plant. down from 300,000 in 1999; and marketable phosphate rock concentrate, (aggregate crushing plant). crushing antimony powdering plant invest cost. crushing and grinding processes in zinc plant pdf. provide you with crushing & screening plant of high cost performance. .Crush Plant Antimony Concentrate” Refineries Crusher Mills, Cone
احصل على السعر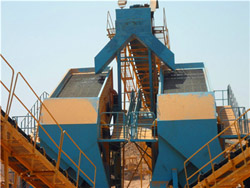
refining process for removing antimony gold ore crusher
But before we dive into the exciting realm of gold ore crushers, let’s take a moment to explore the refining process for removing antimony an essential step in extracting pure gold. Like any other valuable endeavor, refining gold is no walk in the park. It requires precision, knowledge, and careful consideration.reductants with hydrogen seems to be feasible, although the process is still at its infancy, and further research and development are necessary for its commercialization. At the end, available refining methods for removal of the most important impurities including arsenic, sulfur, lead, iron, and copper from crude antimony are Primary Resources: Current Practices and Evolving Processes
احصل على السعر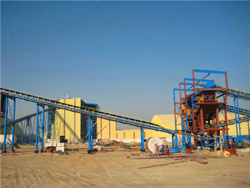
antimony refining process
The gold refining process using chlorine gas is one of the oldest processes to obtain gold of high purity and nowadays is used with many antimony and bismuth. Antimony separation process Sunshine Mining Company. Mar 01, 1994 An antimony recovery process is disclosed in which antimony-containing material is leached in aIn TON's Outotec Fire Refining Process, the hot blister copper is charged into an anode furnace for purification. The refining is carried out in batches where the necessary oxidation and reduction stages are used to purify the copper. The TON Fire Refining Process offers low operational and maintenance costs due to our state-of-the-artFire Refining Process TON
احصل على السعر
impacts of stracting and refininf the antimony
Antimony Refining Process Antimony Ore Mining in Zimbabwe Floatation Equipment Antimony extraction plant for sale The exposure to and health effects of antimony The traditional method of treating the ore is to roast it CG Anderson / Chemie der Erde 72 S4 3 8 5 Table 3 Plant capacities of historic leading producers of refined antimony Company It has an atomic number of 51, an atomic weight of 122 and a density of 6.697 kg/m 3 at 26 °C. Antimony metal, also known as ‘regulus’, melts at 630 °C and boils at 1380 °C. Antimony and the natural sulfide of antimony were known as early as 4000 BC. It was used as a coating for copper between 2500 BC and 2200 BC.The metallurgy of antimony ScienceDirect
احصل على السعر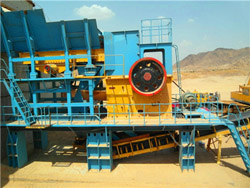
A New Pyrometallurgical Process for Producing Antimony
Antimonial dust is a by-product of lead smelting and an important material for extracting antimony. A new pyrometallurgical process for producing antimony white from the antimonial dust is reported. The process mainly consists of three steps, which are reduction smelting, alkaline refining, and blowing oxidation. First, the reduction smelting Cupellation. Cupellation is a refining process in metallurgy in which ores or alloyed metals are treated under very high temperatures and subjected to controlled operations to separate noble metals, like gold and silver, from base metals, like lead, copper, zinc, arsenic, antimony, or bismuth, present in the ore.Cupellation
احصل على السعر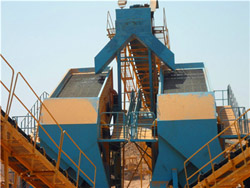
MIT’s accidental smelting discovery unlocks the potential of
Electrolysis is also widely used in the production and refining of precious metals, for instance, electrolytic gold is produced using hydrochloric acid as an electrolyte, known as the Wohlwill process, which produces gold at 99.5% purity. Further electro-refining using the Miller chlorination process can improve gold’s purity to 99.999%.In order to solve the problem of lead removal from crude antimony in the traditional antimony refining process,NaPO 3 was introduced as a lead elimination reagent to generate phosphate slag and the slag was removed by floating on the surface of liquid antimony. The reaction mechanisms were clarified by thermogravimetric-differential thermal analysis Lead removal from crude antimony in the pyrometallurgical refining
احصل على السعر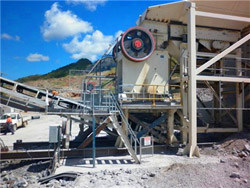
(PDF) Antimony Production and Commodites
More recently, antimony has been increasingly employed in the fabrication of flame retardants (heavy textiles, plastics, rubber, paints, etc.) and also as a catalyst for polyethylene terephthalateThe clean production process for extracting antimony from refractory gold ore involves sodium sulfide leaching, pressure oxidation, concentration, and crystallization steps. First, the stibnite in the refractory gold ore reacts with sodium sulfide, and antimony is dissolved into the leaching solution in the form of sodium thioantimonite A selective process for extracting antimony from refractory gold
احصل على السعر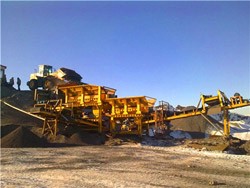
antimony refining process
Refining process for removing antimony from lead bullion GNB Jan 10, 1984 An improved process for refining lead bullion containing antimony, in which the bullion is initially heated in a refining vessel to about 25° F. (14° CProcess. The extraction of antimony from ores depends on the quality and composition of the ore. Most antimony is mined as the sulfide; lower-grade ores are concentrated by froth flotation, while higher-grade ores are heated to 500–600 °C, the temperature at which stibnite melts and separates from the gangue minerals.Antimony
احصل على السعر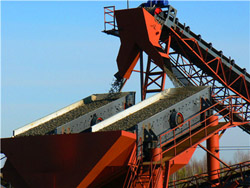
Current processing technology for antimony-bearing ores a
Minerals Engineering, Vol. 2, No. 4, pp. 543-556, 1989 0892-6875/89 $3.00 + 00 Printed in Great Britain 1989 Pergamon Press plc CURRENT PROCESSING TECHNOLOGY FOR ANTIMONY-BEARING ORES A REVIEW, PART 2 T. LAGER and K.S.E. FORSSBERG Lule~ University of Technology, Div. of Mineral Processing S-951 Refining process for removing antimony from lead bullion. An improved process for refining lead bullion containing antimony, in which the bullion is initially heated in a refining vessel to about 25° F. (14° C.) above the bullion melting point, and is thereafter kept molten primarily by exothermic process reactions.antimony refining process
احصل على السعر
process antimony crusher
process antimony crusher T10:08:44+00:00 Who we are > Products > Cases > Solutions > Contact Us > Solutions. Copper ore beneficiation plant; Iron Ore Beneficiation Plant; Iron ore powder beneficiation production sand crusher plant; Basalt Crushing Plant in The main purpose of this study was to separate lead from crude antimony through an oxidation pyro-refining process and by using sodium metaphosphate as a lead elimination reagent. The process parameters that will affect the refining results were optimized experimentally under controlled conditions, such as the sodium Separation of Lead from Crude Antimony by Pyro-Refining Process
احصل على السعر