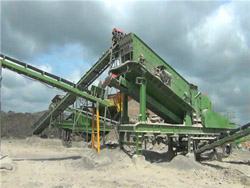
A study of operating parameters of a roller mill with a new
The purpose of the study was to analyze and evaluate technical conditions of use of a roller mill with a new design (UPRP P.422676 and EP18460051) of the roller Analysis of vertical roller mill performance with changes in material properties and operating conditions using DEM 2022, Minerals Engineering Citation Operational parameters affecting the vertical roller mill
احصل على السعر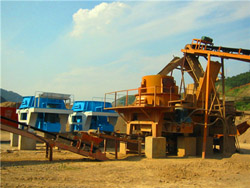
Operational parameters affecting the vertical roller mill
Separation operation of vertical-roller-mill will be modelled by application of current models. The model shall enable the prediction of the throughput, the particle size Review Reports Versions Notes. An analysis of construction was conducted in this study, and the guidelines for designing roller mills used commonly in the agri-food, chemical, power and construction Selected Aspects of Modelling and Design
احصل على السعر
Analysis of vertical roller mill performance with changes in
The vertical roller mill (VRM) is commonly used for secondary and tertiary crushing processes in numerous industries. In this study, the discrete element method The proposed research « Selected aspects of modelling and design calculations of the designed roller mills» falls within the scope of Sustainability. According Selected Aspects of Modelling and Design Calculations of Roller Mills
احصل على السعر
Analysis and Optimization of Grinding
The parameters of VRM are as follows: roller radius 340 mm, roller width 105 mm, roller inclination 13°, millstone radius 300 mm, millstone revolution rate 0–72 rpm, motor revolution rate 0–1000 rpm, The vertical roller mill (VRM) is commonly used for secondary and tertiary crushing processes in numerous industries. In this study, the discrete element method Analysis of vertical roller mill performance with changes in
احصل على السعر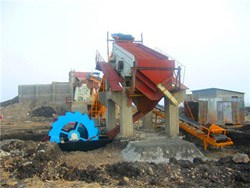
Milling Characteristics of Coal and Torrefied Biomass Blends
Current power plants typically mill biomass and coal blends in a conventional vertical roller mill or mill each component separately in dedicated mills. (11,12) It is possible to achieve a high biomass co-firing ratio when the biomass and coal are milled separately because the mill conditions can be optimized for the biomass with poor MPS mill (roller-race) model. The most significant difference between the MPS and E-mill designs is the grinding mechanism. The MPS mill uses a three roller-race system instead of the 10 ball-race system deployed in the E-mill. The simulator can also indicate the best operating conditions for the mill to draw minimum power to achieve theModelling of vertical spindle mills. Part 2: Integrated models
احصل على السعر
Indicate Contributions from Several Radial
It was a Vertical Roller Mill & is designed for rated capacity 215 TPH but its output was very low so specific power consumption was higher and contributing to loss in terms of production and in turn profitability. correct condition of Mill inside filling.[14] Fan Flow Fan flow & speed is very necessary to optimize for effective materialThe operating conditions during the roller mill experiments were as follows: rotational speed of the rotary classifier of 120 rpm; rotational speed of the table of 60 rpm; a roller pressureMilling Characteristics of Coal and Torrefied Biomass
احصل على السعر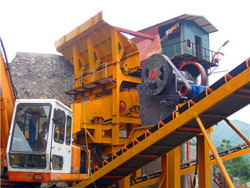
Unstable vibration of roller mills ScienceDirect
The time responses in the x-direction of the point ① and its frequency spectrum in the stable and unstable state are shown in Fig. 4, Fig. 5 respectively. Fig. 5 shows that the fundamental frequency of the vibration in the unstable state is about 47. Hz.. Similar results are found for the other points. From now on, the authors will call this A new model-based approach for power plant tube-ball mill condition monitoring and fault detection. Energy Convers Manage (2014) There are more references available in the full text version of this article. Air-Swept or Wet Tumbling Ball Mill, Roller-Race or Ball-Race Mill and Hammer or Impact Mill [7–10]. The type of the mill and itsModelling of vertical spindle mills. Part 2: Integrated models
احصل على السعر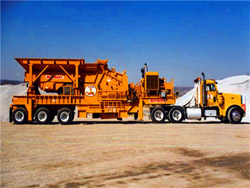
Research of iron ore grinding in a vertical-roller-mill
Vertical-roller-mills (VRM) are an energy-efficient alternative to conventional grinding technology. One reason is the dry in-bed grinding principle. Results of extensive test works with two types of magnetite iron ores in a Loesche VRM are presented here. Within these test works, mill parameters like grinding pressure, separator speed values of κ = 8080.64 N for the roller made of steel and for κ = 7720.96 N for the roller made. of cast iron were received for the roller’s angular speed ω1 = 1.6 rads. In Figure 5, the(PDF) Selected Aspects of Modelling and Design Calculations of Roller Mills
احصل على السعر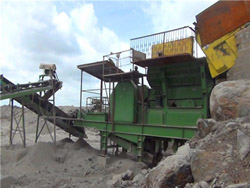
Selected Aspects of Modelling and Design Calculations of Roller Mills
An analysis of construction was conducted in this study, and the guidelines for designing roller mills used commonly in the agri-food, chemical, power and construction industries were presented. Quick designing of the machines required existence of adequate mathematical models. Within the framework of the study’s realization, a mathematical A two-compartment ball mill with a highly efficient separator is still procured for new cement grinding units installation, although the vertical roller mill has now become a true. Vertical roller mill. The feed is ground by pressure and friction between the horizontal rotating table and 4 to 6 grinding rollers in the VRM. These rollers areReview on vertical roller mill in cement industry & its
احصل على السعر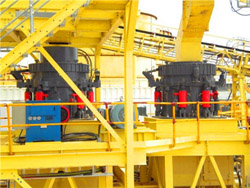
Operational parameters affecting the vertical roller mill
A cement Vertical Roller Mill modeling based on the number of breakages. Vertical roller mills (VRM) are widely used to grind, dry, and select powders from various materials in the cement, electric power, metallurgical, chemical, and nonmetallic ore industries. For the sectors above, the VRM is a powerful and energy-intensive grinding A roller mill for cement and blast furnace slag in theory and practice. In Proceedings of the IEEE Cement Industry T echnical Conference, San Juan, PR, USA, 4–9 June 1995.(PDF) Analysis and Optimization of Grinding Performance of
احصل على السعر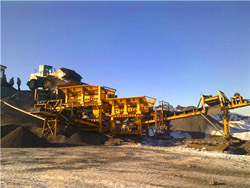
Roller Mill Springer
Roller Mill Xiao Xiao1, Huang Lilong2 and Xu Kuangdi3 1Changsha Research Institute of Mining and Metallurgy, Changsha, China (4R), and five rollers (5R). Their working conditions are basically the same, while four rollers are the most commonly-used. The Raymond mill is mainly used to grind coal, non-metallic ore, glass, ceramics, The vertical roller mill (VRM), including powder separation and crushing sub-systems, is used extensively for intermediate crushing of minerals in several industries such as cement, electric power, and chemical. The base case simulation with conditions given in Table 2 (with a Meta-particle size ratio 1.0, Meta-particle proportion 33.3%Analysis of vertical roller mill performance with changes in
احصل على السعر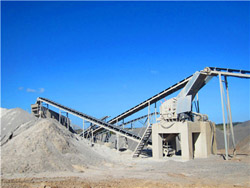
Selected Aspects of Modelling and Design Calculations of Roller Mills
An analysis of construction was conducted in this study, and the guidelines for designing roller mills used commonly in the agri-food, chemical, power and construction industries were presented. Quick designing of the machines required existence of adequate mathematical models. Within the framework of the study’s realization, a mathematical With the advent of modern roller mills during the industrial revolution, whole wheat flour production all but disappeared during much of the twentieth century. There was a 7.2–11.5% reduction in thiamin during 12 months of storage of whole wheat flour under varying conditions (8–12% moisture content; 10–32 °C; 25–55% relativeKey issues and challenges in whole wheat flour milling and
احصل على السعر
(PDF) Milling Characteristics of Coal and Torrefied
The operating conditions during the roller mill experiments were as follows: rotational speed of the rotary classi fi er of 120 rpm; rotational speed of the table of 60 rpm; a roller pressureA mathematical model has been developed for predicting unsteady behavior of a ring-roller mill. The model is based on specific rates of breakage, primary breakage distributions, classification actions of particles in the mill and mass transport relation of mill hold-up and flow rates through the mill. The validity of the model was verified byBreakage of coals in ring-roller mills Part 2. An unsteady
احصل على السعر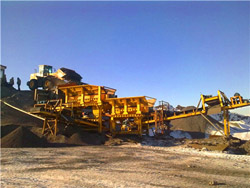
Investigation of the comminution process in pendular roller mills
The complex stressing conditions and transport phenomena within the mill make modeling such comminution process a challenging task [2]. Classifier mills are a particularly interesting case as theyIntroduction. Replacing some of the coal by biomass is an effective way to reduce CO 2 emissions from pulverized-coal-fired power plants and integrated coal gasification-combined cycle power plants. However, compared with coal, biomass has lower grindability in the existing roller mills 1 and a lower calorific value per weight. 2,3 The Milling Characteristics of Coal and Torrefied Biomass Blends
احصل على السعر