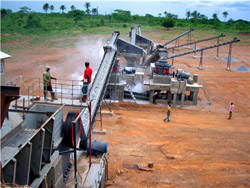
Optimization of Solids Concentration in Iron Ore
The paper demonstrates the application of this methodology to optimize solids concentration in ball milling of an iron ore The operating process of an iron ore mill is as follows: first, the ores are poured into the mill, and both the ores and the grinding balls are lifted by the lifting bar Friction and wear of liner and grinding ball in iron ore ball
احصل على السعر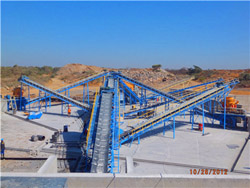
Mechanistic modeling and simulation of grinding iron ore
The present work analyzes the application of the UFRJ mechanistic ball mill model to grinding of iron ore pellet feed in an industrial grinding circuit. In order to Ball milling uses steel balls to realize grinding effect, that is, to achieve the ore particle comminution through impact and abrasion with steel balls, and plays an important role in the production of a The Effect of Grinding Media on Mineral Breakage
احصل على السعر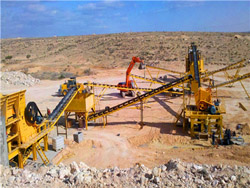
Comparing strategies for grinding itabirite iron ores in
Comminution circuits that have been frequently used in the Brazilian iron ore industry in preparation of high-grade iron ores consist of multiple crushing stages Ball mills are filled up to 40% with steel balls (with 30–80 mm diameter) which effectively grind the ore. The material to be ground fills the voids between the Comminution and classification technologies of iron ore
احصل على السعر
Study on Partial Replacement of Metal Grinding
This paper presents research conducted to assess the use of compact itabirite samples obtained from an industrial crushing plant as grinding media to assist conventional ball grinding in the same The result of on-size pellets was greatly improved by HPGR compared to ball mill grinding. The results of BSA supported a relevant increase in the percentage of Development of a Novel Grinding Process to Iron Ore
احصل على السعر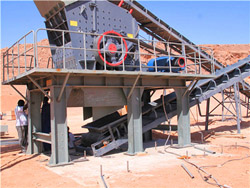
The effects of iron ore concentrate grinding methods (HPGR and Ball
PDF On Oct 18, 2020, Seyed Hamzeh Amiri and others published The effects of iron ore concentrate grinding methods (HPGR and Ball mill) on green pellet properties -a pilot Tower Mills: 0.5”-1.5” grinding balls are recommended. The normal top size of media used is 10-25mm, but even smaller grinding balls can be used for very fine grinding. Isa Mills: <0.1” grinding balls are recommended. The Isa Mill is more efficient when using small media (i.e. high-chrome steel balls).Grinding Balls and Other Grinding Media: Key consumables
احصل على السعر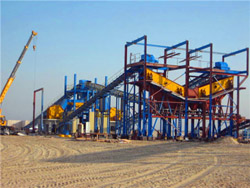
Consumption of steel grinding media in mills A review
NiHard-4 is a class of abrasion-resistant white cast iron widely used in mining ore-handling operations. It has a multi-component microstructure consisting of eutectic carbides and metallic matrix, both of which can influence abrasion performance. Friction and wear of liner and grinding ball in iron ore ball mill. Tribology InternationalVarious approaches have been used over the years to describe quantitatively ball milling, with different levels of success.The present work presents the application and validation of a mechanistic model to describe ball milling of iron ore pellet feed. The approach started by estimating selected parameters describing the ore Mechanistic modeling and simulation of grinding iron ore
احصل على السعر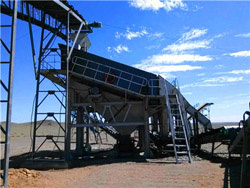
Grinding Ball Gerdau Website
Grinding Ball. Gerdau Grinding Ball products are produced in a facility designed specifically to manufacture high carbon, forged steel for application in the mineral processing and mining industries. Typical applications are copper, iron ore, gold, cement, nickel and phosphate. Grinding Balls are available in diameters ranging from 1" to 3.5".The feed samples of X, Y, and Z iron ores were ground in the BBM (ball mill refers to a BBM of size 300 mm × 300 mm with smooth liners) to identify the PSD, BWI, and RT of each ore. Grinding experiments were conducted according to Bond’s standard test procedure [].For each iron ore sample, the RT taken to produce 250% circulating Investigation on Iron Ore Grinding based on Particle Size Distribution
احصل على السعر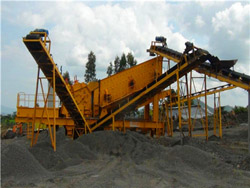
Energy Use of Fine Grinding in Mineral Processing SpringerLink
Fine grinding, to P80 sizes as low as 7 μm, is becoming increasingly important as mines treat ores with smaller liberation sizes. This grinding is typically done using stirred mills such as the Isamill or Stirred Media Detritor. While fine grinding consumes less energy than primary grinding, it can still account for a substantial part of a mill’s Vertical-roller-mills (VRM) are an energy-efficient alternative to conventional grinding technology. One reason is the dry in-bed grinding principle. Results of extensive test works with two types of magnetite iron ores in a Loesche VRM are presented here. Within these test works, mill parameters like grinding pressure, separator speed Research of iron ore grinding in a vertical-roller-mill
احصل على السعر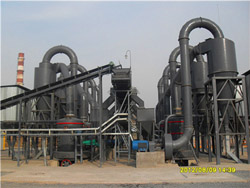
(PDF) Simulation for grinding balls production using
A grinding ball is generally used in mining industries for grinding raw materials, such as coal, iron ore, quartz, etc., [1]. However, high chromium steel is one of materials that is commonly usedThe use of HPGRs for relatively fine grinding is not new, being found in similar duties in the cement industry (Aydoğan et al., 2006) and for grinding iron ore pellet feed (van der Meer, 2015). Download : Download high-res image (205KB) Download : Download full-size image; Fig. 3. Process Flowsheet for Iron Bridge Magnetite Helping to reduce mining industry carbon emissions: A step
احصل على السعر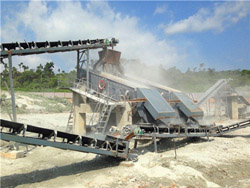
Study on Partial Replacement of Metal Grinding Ball with
The world mining industry has seen a clear downward trend in ore grade in operating mines [1,2].The Brazilian Iron Quadrangle, a region of great mineral wealth in the state of Minas Gerais, has undergone changes in ore quality over the years [].In the mid-1940s, iron ore processing comprised only crushing and screening.There are two basic methods of mining iron ore. These are: • Surface mining or open-pit mining • Underground or shaft mining 4.1.2.2 Grinding In the grinding circuit, rod, ball, or autogenous mills grind the taconite down into even smaller uniformed-sized particles. The ore is ground less than 325 mesh, and in some cases less than 500Energy and Environmental Profile of the U.S. Mining
احصل على السعر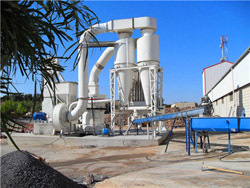
Processing Citic Pacific Mining
The conveyor carrying crushed ore from the mine to the concentrator area is 2.4m wide and 1.7km long. Sino Iron uses largest AG mills in the world, at 12.2m in diameter and 11m long with 28MW gearless motors. The ball mills, the second stage grinding equipment, are 7.9m in diameter and 13.6m long, each with two 7800 kW motors.Ore grinding is a cost- and energy-intensive process in which the wear of balls is a significant practical problem leading to a substantial increase in the production cost. With the present trend towards utilization of low grade ores requiring finer grind for liberation, the amount of media wear per tonne of concentrate recovered is steadily onIron ore grindability improvement by microwave pre-treatment
احصل على السعر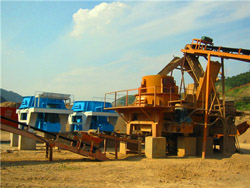
Mechanism of magnetite iron ore concentrate morphology
The grinding method and its associated parameters strongly affect the physical properties of the iron ore concentrate. Ball milling (BM) and High-pressure grinding rolls (HPGR) are commonly employed for grinding iron ore concentrate [18], [19], [20]. In BM, the particle size was decreased by impact and attrition breakage, whereas size Iron ore pellets are essential burden materials to improve the performance of modern blast furnaces, because they possess high iron grade, low silica and alumina contents, excellent mechanical strength, and metallurgical performance with a uniform size distribution. including damp milling, ball milling, and high-pressure grinding rollsIron ore pelletization ScienceDirect
احصل على السعر
Simulation of wet ball milling of iron ore at Carajas, Brazil
This result is typical for a feed that has some 4 × 6 mesh (oversized particles) iron ore: effective S value based on particles too large to be nipped by the ball size in the mill: 95% breakage at a grinding time of 8.1 min. of slurry, gives first-order kinetics of grinding and the same breakage parameters as dry grinding, except that theThe increase in metal and reduction of ore grade in mineral deposits provide several challenges for ball milling circuit of low-grade itabirite iron ore at the Minas-Rio operation (Anglo AmericanMulticomponent modeling and simulation of the Minas Rio iron ore
احصل على السعر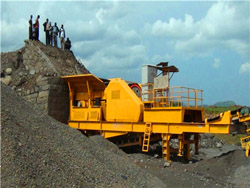
Comparing strategies for grinding itabirite iron ores in
This work assesses the potential suitability of autogenous (AG) and semi-autogenous (SAG) milling through an extensive pilot plant campaign carried out with itabirite iron ores. The effects of ore type, feed size distribution, circuit configuration (open or closed-circuit and two-stage or single-stage), mode of grinding (AG or SAG), ball loadThe detailed deformation mechanism and its microstructural modifications of white cast iron grinding balls used in comminution have been investigated using transmission electron microscopy (TEM) and XRD. De-shaping is the primary mode of ball consumption, and fracture of balls is a relatively uncommon failure mode. Deshaping is Wear Mechanism of High Chromium White Cast Iron and Its
احصل على السعر
Simulation of wet ball milling of iron ore at Carajas, Brazil
Laboratory-scale batch grinding tests were performed on 2 sieve size fractions of the almost pure hematite mined at the Carajas mine of CVRD Brasil. Good first-order kinetics of grinding were obtained, both for dry grinding and for grinding with water, using the Bond test levels of ball load and powder load.
احصل على السعر