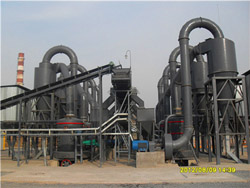
wet ball milling process c cao. TECHNICAL NOTES 8 GRINDING R.P.King Mineral Tech. TECHNICAL NOTES 8 GRINDING R.P.King.8 2.Overflow discharge Wet Figure 8.5 Effect of mill fillingContribute to sbmcrushers/sbmchina development by creating an account on .sbmchina/sbm wet ball milling process 2c cao.md at main
احصل على السعر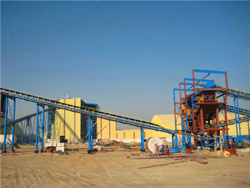
Wet ball milling of niobium by using ethanol, determination
In the wet milling technique, process control agents (lubricant or surfactant) such as: ethanol, stearic acid, methanol, hexane etc., are added to the It is found that the prolongation of ball-milling duration is beneficial to improve the cyclic CO 2 capture capability of wet ball-milled dolomite. The solid-to-liquid Stabilized CO2 capture performance of wet mechanically activated
احصل على السعر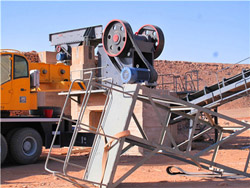
sbm/sbm wet ball milling process cao.md at main dihog/sbm
Contribute to dihog/sbm development by creating an account on .wet ball milling process 2c cao. ChemSusChem 2013,6,193 198. School of Chemical Sciences. Aug 28,2012.DOI: 10.1002 cssc.201200454.Mechanical Activation of CaO
احصل على السعر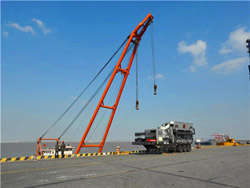
Wet ball milling of niobium by using ethanol,
This study investigates the eect of using ethanol as the process control agent during the wet ball milling of niobium (Nb). Dried nanocrystal Nb powders, of high As compared to the conventional dry-milling process, high loose structure and uniform distribution of sulfur can be obtained by adding ethanol during the ball Wet ball-milling synthesis of high performance sulfur-based composite
احصل على السعر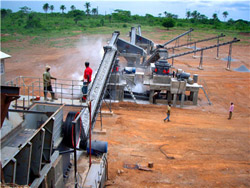
Recent advances in mechanochemical production of
Mechanical ball milling technology, which has emerged as an efficient and environmentally sound alternative to traditional method, can overcome this obstacle to Ball milling parameters have been studied on WC-10Co. • Dry and wet ball milling do not provide the same powder quality after milling. • Wet medium and low High-energy ball milling of WC-10Co: Effect of the milling
احصل على السعر
Suppressing Heavy Metal Leaching through Ball
A two-stage process with a water/solids ratio of 5 was adopted. At each stage, the solution was vibrated for 30 min on a horizontal water bath oscillator at 25 °C. Both the fly ash (FA) and the washed fly Here, we show that scalable production of monolayer nanosheets can be achieved by a facile ball-milling exfoliation method with the assistance of viscous polyethyleneimine (PEI) liquid. As aScalable high yield exfoliation for monolayer nanosheets
احصل على السعر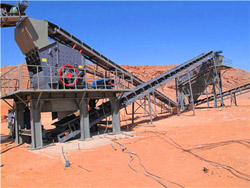
Comparison on structural modification of industrial lignin by wet ball
The ball-milling process was performed in a WL-IA planetary ball mill (Rishengjiuyuan Co., Ltd., Tianjing, China) equipped with four zirconia milling jar (500 ml for each one). Each jar was loaded with 30 g industrial lignin, 80 ml phosphoric acid (4%, w/v) and 30 zirconia balls ( φ = 10 mm) and milled at 400 rpm for 30 min.An improved method for mass production of good-quality graphene nanosheets (GNs) via ball milling pristine graphite with dry ice is presented. We also report the enhanced performance of these GNs as working electrode in lithium-ion batteries (LIBs). In this improved method, the decrease of necessary ball milling time from 48 to 24 h and One-step preparation of graphene nanosheets via ball milling
احصل على السعر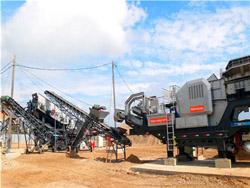
Physicochemical and structural characteristics of nano
Nano eggshell calcium (NEC) powder was prepared from biowaste chicken eggshells using wet ball milling. The characteristics of the NEC, including the zeta potential, micromorphology, elemental composition, particle size distribution, Ca 2+ concentration, and chemical structure, were investigated. According to the results, the optimum process This study investigates the effect of using ethanol as the process control agent during the wet ball milling of niobium (Nb). Dried nanocrystal Nb powders, of high purity, with particle sizesWet ball milling of niobium by using ethanol, determination
احصل على السعر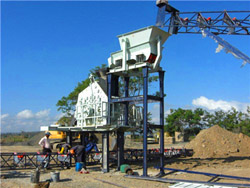
Novel synthesis of Mn RSC Publishing
Mn 3 (PO 4) 2 3H 2 O precursor was synthesized by a novel precipitation process using ethanol as initiator, and was lithiated to LiMnPO 4 /C composite via a combination of wet ball-milling and heat treatment. The as-synthesized precursor was plate-shaped with nanosize thickness. After heat treatment of the ball-milled mixture of Mn 3 (PO 4) 2 3H 2 Ball mill effectively enlarged the SSA of the biochars (Table 1).After ball milling, the SSA of the biochars increased by 1.67–2.41 times. Among the ball milled samples, CN600-O and CN600-N had higher SSA than CN600-BM, indicating that H 2 O 2 and NH 4 OH are effective modifiers for biochar. Similar observation was reported by Xu Ball milling biochar with ammonia hydroxide or hydrogen peroxide
احصل على السعر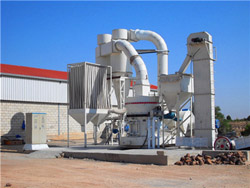
wet ball milling process c cao. TECHNICAL NOTES 8 GRINDING R.P.King Mineral Tech. TECHNICAL NOTES 8 GRINDING R.P.King.8 2.Overflow discharge Wet Figure 8.5 Effect of mill fillingAbstract. In order to improve the dispersibility, thermal stability and pH adaptability of organic pigments in water, submicrometer copper phthalocyanine (CuPc)/SiO 2 composite particles (CPs) were prepared through a simple one-pot wet ball-milling process under acidic conditions without using any organic surfactant. In the as-obtained CPs, the surface of Preparation of copper phthalocyanine/SiO RSC Publishing
احصل على السعر
Ball milling: a green technology for the
The use of ball milling to obtain cellulose nanocrystals was also explored by the group of Yu, who extracted CNCs from ball-milled wood via a multi-step process. 40 Douglas-Fir wood chips were firstly hammer-milled to wood The breakage and liberation of minerals are the key to fluidized mining for minerals. In the ball milling process, steel balls function as not only a grinding action implementer but also energy carrier to The Effect of Grinding Media on Mineral Breakage
احصل على السعر
Mechanochemical remediation of soil contaminated with
Mechanochemical method was proposed for the remediation of soil contaminated with heavy metals (HMs, Cu, Pb, and Cd) and persistent organic pollutants (POPs, PBDEs and PCBs) through ball milling with nanoscale Zero-valent Iron (nZVI)-CaO-Ca 3 (PO 4) 2 (NCC). The mechanical energy supplied by ball milling and NCC The ball-milling of materials is a mechanical grinding method that has different effects on treated materials, and can be used for the direct synthesis of organometal halide perovskite (OHP) crystals. Herein, the effect of such a process, extended over a large temporal window, is related to the properties of referential three-dimensional (3D) MAPbI3 (MA = Applied Sciences Free Full-Text The Effect of Extended Ball-Milling
احصل على السعر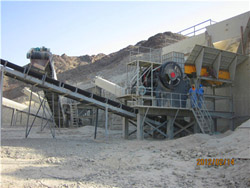
Optimization of Formulation and Operating Parameters for
Wet ball milling (WBM) technique is regarded as one of the most successful top-down nanosizing techniques. It is an aqueous grinding process, which reduces the drug particle size to nanoscale by high-speed friction, collision, and extrusion between grinding beads [ 15 18 ].The procedure of preparation is as follows: take a certain amount of TiO 2 powder and put it into the agate ball milling tank in a ratio of 1 to 10 between TiO 2 powder and agate ball, and then add a certain amount of WO 3 and H 2 O. After ball milling for 12 h at the speed of 300 rpm, remove and dry the wet powder in air below 110 °C.The preparation of coupled WO3/TiO2 photocatalyst by ball milling
احصل على السعر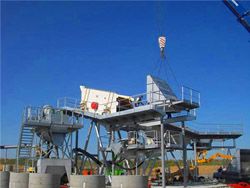
(PDF) Influence of Media Geometry on Wet Grinding of a Planetary Ball Mill
Small balls lead to a higher milling energy and faster particle size reduction, while larger balls lead to a lower milling energy and slower particle size reduction. For example, in a mill with aMilling was performed under the condition of a wet ball milling process. For the milling process, 40.12 g of the as-received Nb powder were loaded into two separateWet ball milling of niobium by using ethanol,
احصل على السعر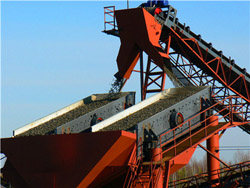
Effects of wet ball milling on lead stabilization and particle
The quantities of Pb in the milled ash, milled solution, milling ball, and milling jar were analyzed to determine the partitioning of Pb after the milling process. The experimental results show that 93.11% of Pb was in the milled ash, 2.60% on the milling balls, 0.17% on the inner surface of the milling jar, and Pb remaining in the milledFurthermore, the optimal conditions for the ball-milling process to induce efficient mechanical exfoliation of boron were determined to be 450 rpm, 6 hours, and 1 g (450 rpm_6 h_1 g), whichBall milling of eggshell waste as a green and ResearchGate
احصل على السعر