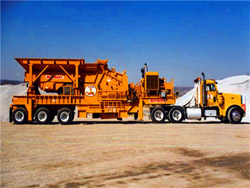
Workpiece reciprocating movement aided wire electrochemical machining
Based on the principle of electrochemical anodic dissolution at the atomic format, electrochemical machining (ECM) is a machining process to corrode the EDM process involves the erosion of workpiece through spark which includes melting and vaporization, material transformation from tool, repeatedly Surface modification during electrical discharge machining process
احصل على السعر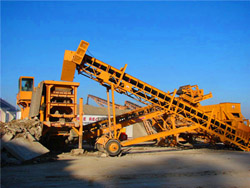
The state of the art of electrical discharge drilling: a review
Electrical discharge machining (EDM) is one of the most widely used non-conventional methods to machine electrically conductive materials in the manufacturing 2 天之前In electrical discharge machining (EDM) process, electric discharge is used to form high localised temperature. Therefore, the material is removed from the workpiece Unravelling the analysis of electrical discharge machining process
احصل على السعر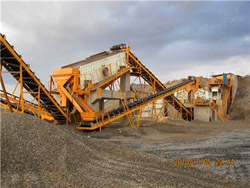
Electrical Discharge Machining an overview ScienceDirect
Electrical Discharge Machining (EDM) is a machining technique through which the surface of a metal workpiece is formed by discharges occurring in the gap between the tool, which The improvements introduced later allowed the extension of this machining technology to obtain more complex ruled surfaces with increasingly high (PDF) Wire Electrical Discharge Machining—A Review
احصل على السعر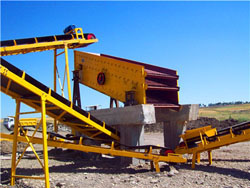
Free Full-Text Wire Electrical Discharge Machining—A Review
To obtain specific benefits, both the EDM process (machining accuracy) and ECM process (quality of the surface integrity), a successive machining by wire Of late, the research fraternity has set significant benchmarks in machining of ceramics. In this paper, a comprehensive review of the electric discharge machining An overview of electric discharge machining of ceramics and
احصل على السعر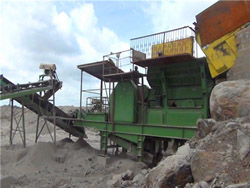
Study on removal of recast layer of NiTi shape memory alloy machined
In this paper, a magnetic field-assisted WEDM-ECM complex process (MF-assisted WEDM-ECM) is proposed to solve the problems of traditional low-speed wire The workpiece was beforehand machined by an ordinary three-axis controlled machining center, which had a 1 μm resolution of each translational axis and then was set on a vacuum chuck that was mounted JMMP Free Full-Text An Efficient Ultraprecision
احصل على السعر
Manufacturing technologies toward extreme precision
Mechanical machining is further divided into cutting methods, such as turning, milling, drilling, etc, and abrasive machining methods, such as grinding, lapping, and polishing. Additive manufacturing is a process by which a workpiece is constructed by depositing material in layers such that it becomes a predesigned shape.Electrical discharge machining (EDM) can use soft tool electrodes to process hard workpieces to achieve “soft against hard”, because it directly uses electrical energy and thermal energy to remove Parameters Optimization of Electrical Discharge
احصل على السعر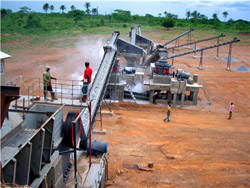
Aluminum Machining Ardel Engineering and Manufacturing
Aluminum Machining. Machining is a subtractive manufacturing process, meaning it removes material from a workpiece to create the desired part or product. It is highly versatile, accommodating a wide range of metal and non-metal substrates. One of the most common materials used in machining operations is aluminum.Abstract. Chemical machining (CM) is an advanced machining technique that is used to selectively remove material from workpiece using strong chemical reagent known as etchant. The corrosion process is utilised to remove material from the needed area of the workpiece. The material removal in chemical machining process takes place by Chemical Cutting Process SpringerLink
احصل على السعر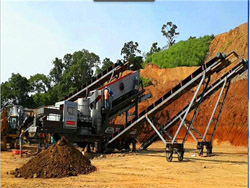
All About Wire EDM Machining: Definition, Application, and
Wire electrical discharge machining (wire EDM) is a process that works by continuously feeding a wire electrode under tension on a vertical axis. Discharge voltage is applied through the wire, crosses via a dielectric liquid, and strikes the grounded workpiece. The workpiece is moved in an X-Y plane to trace a cut pattern through the material.Sivaprakasam et al. [] experimentally studied the possibility of obtaining super surface polish at the nano level, smaller kerf width, and high material removal rate in machining titanium alloy (Ti–6Al–4V) with the Micro-WEDM process.They concluded that when the discharge voltage rises, the value of Ra rises, and then it falls. It has been Performance evaluation of electric discharge machining of
احصل على السعر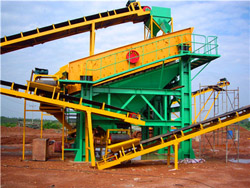
Optimization techniques for energy efficiency in machining
Metal working process is one of the main activities in mechanical manufacturing industry; it is considered as a major consumer of energy and natural resources. In material removal process, the selection of cutting parameters and cooling or cutting liquid is necessary to save energy and achieve energy efficiency as well as It helps to maintain an equilibrium between factors such as costs, product quality, and time. When comparing the 3, 4, and 5-axis machining capabilities, 5-axis CNC machining is not always suitable for all products despite being more effective than 4-axis CNC machining and 3-axis CNC machining. Also, Not all products eligible for 3-axisMulti-Axis Machining: Different Between 3, 4, and 5-Axis CNC Machining
احصل على السعر
Boring Machining Process: A Detailed Overview WayKen
The primary purpose of boring machining is to broaden or expand the hole in a workpiece. The process cannot create the initial hole; instead, it enlarges the hole at high precision. It is the go-to manufacturing technique for producing holes of specific diameters in a workpiece.It is also a versatile machining process, ideal for machining extremely hard metals and alloys, as well as odd shapes, small sizes, and deep holes. 11. Abrasive Jet Machining. This type of non Types of Machining Process: Classifications and
احصل على السعر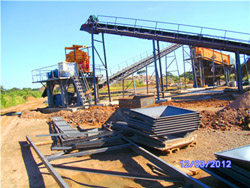
A systematic review on powder mixed electrical discharge machining
Electrical discharge machining (EDM) is extensively used to machine such a ‘difficult-to-machine’ and high strength and temperature resistant (HSTR) alloys. These materials are generally used in the die and mold making industries [ 3 ]. In 1770, physicist, Joseph Priestly discovered the erosive effect of electrical discharges on metals.Abstract. Nonconventional micromachining processes are developed to meet the manufacturing requirements of new materials and products where usual processes are found inadequate. Based on the type of energy used for material removal, the different micromachining processes are classified into thermal, mechanical, chemical and hybrid Non-conventional Micro-machining Processes SpringerLink
احصل على السعر
Prediction of temperature field in machined workpiece
The heat generated and accumulated on the machined surface of an Inconel 718 workpiece causes thermal damage during the cutting process. Surface-active media with high thermal conductivity coated on the workpiece to be machined may have the potential to reduce the generation of cutting heat. In this study, a theoretical model for 2 天之前The vertical machining center has been developing for more than 150 years. For years of development, the vertical machining center has become a multi-functional machine with high precision, high efficiency and so on. A vertical machining center is a machine tool which is ideal for complex metal processing. Therefore, it’s very popular amongWhat is a Vertical Machining Center (VMC)?
احصل على السعر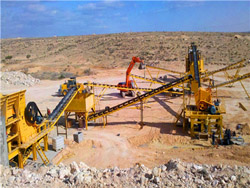
Machining Performance and Surface Integrity of AISI D2 Die
The aim of this study is to establish optimum machining conditions for EDSG of AISI D2 die steel through an experimental investigation using Taguchi Methodology. To achieve combined grinding and electrical discharge machining, metal matrix composite electrodes (Cu-SiCp) were processed through powder metallurgy route. PECM has several advantages in comparison to conventional electrochemical machining. The implementation of a pulsed electric current, instead a continuous current, leads to higher accuracy and process stability [].A further improvement is the combination of a pulsed electric current with an oscillating cathode to increase the Design of Pulsed Electrochemical Machining Processes Based
احصل على السعر
Surface texture and integrity of electrical discharged machined
Electrical discharge machining (EDM) is a non-conventional machining process, extensively applicable in the modern industry. Owing the non-contact nature of the process, any electrical conductive material can be machined in high quality, regardless its mechanical properties. Titanium alloys are commonly machined by EDM, as difficulties The recent times have seen an expanding enthusiasm for the novel uses of electrical discharge machining (EDM) method, with specific accentuation on the capability of this procedure for surface modification. Other than the disintegration of work material amid machining, the inborn idea of the procedure results in the expulsion of tool material too.Review on Surface Modifications of the Workpiece by Electric
احصل على السعر