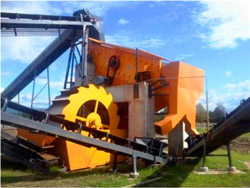
Specialized Methods of Internal Grinding Metal
One very interesting — perhaps the ultimate — example of the honing finishing process is a method called abrasive flow machining. Modeling of the cutting forces on the example of the internal grinding The mathematical model of the intragrinding process of non-circular holes is based on the Mathematical Model for the Internal Grinding Process of a
احصل على السعر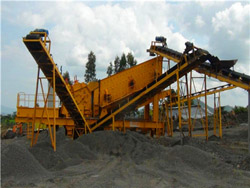
A comprehensive review on the grinding process:
Abstract. Grinding is a manufacturing process which significantly contributes in producing high precision and durable components required in numerous This study presents an internal gear grinding method with high grinding speed using a barrel-shaped grinding wheel by setting a large crossed-axes angle Grinding of internal gears by setting a large crossed-axes angle using
احصل على السعر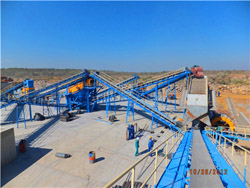
Design and evaluation of an internal-cooling grooved grinding wheel
To improve the grinding performance of superalloys, a bowl-type internal-cooling grinding wheel with a phyllotactic abrasive pattern has been developed. The 1 Introduction Cylindrical parts with deep holes are crucial in the aerospace field, which realized the significance of high precision machining of deep holes. In Modeling and Design Analysis of a Deep Hole Internal Grinding
احصل على السعر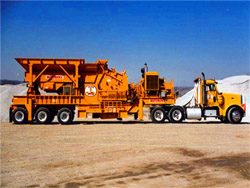
Grinding SpringerLink
Grinding is the predominate process while machining brittle materials such as glass, ceramics, or even diamond at high accuracy. The ability to machine those In internal grinding, two different processes are employed: grinding with axial supply; and grinding with radial supply (the beginning of each pass in insertion). Cutting Forces in Internal Grinding SpringerLink
احصل على السعر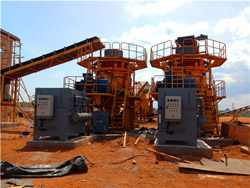
Grinding SpringerLink
Grinding is the predominate process while machining brittle materials such as glass, ceramics, or even diamond at high accuracy. The ability to machine those materials makes grinding also the first choice for finishing tasks. Examples are grinding of hardened bearing seats or machining engineering ceramics.This paper proposes a pressurized internal cooling grinding wheel with a removable abrasive ring to investigate the effects of flow channel structure and abrasive ring mounting position on grinding performance. A model was constructed to assess the flow and temperature fields of the grinding arc area, utilizing flow-solid heat transfer.Thermal Analysis of Grinding ScienceDirect
احصل على السعر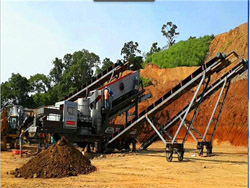
Advances in grinding tools and abrasives ScienceDirect
Grinding wheels with internal MWF supply aim to overcome the issue of providing MWF to the contact zone, especially for high contact lengths. Concepts for internal MWF supply are even more elaborate than concepts for sub-assembly. Examples of grinding wheels with grits arranged in grit lines from different authors; from left to right: grinding and also between internal and external gear grinding. In the case of continuous gear grinding, the tool is a worm grinding wheel as Grinding Machines, Table 2 Fourth level classification of grinding with rotating tools according to DIN 8589-11 (2003) as master for all three 3rd level grinding processes No. 4thGrinding Machines Springer
احصل على السعر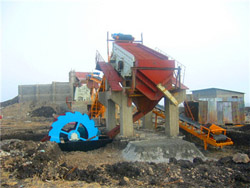
An internal cooling grinding wheel: From design to application
The flow field in the grinding area was solved and calculated in Fluent using oblique pattern C as an example. Internal cooling grinding was realized using a BT40-ER32–150 tool holder by the Haimer Tool Company and the as-fabricated internal cooling wheel. The upper end of the tool holder was connected to the machine tool Generally, the target cycle time to grind internal gears in mass production is less than 2 min. Depending on the gear specifications, the cycle time of conventional profile grinding is over 30 min in most cases. For example, continuous generating grinding of internal gears with barrel-shaped wheels at large crossed-axes angles (20-35°) isGrinding of internal gears by setting a large crossed-axes angle using
احصل على السعر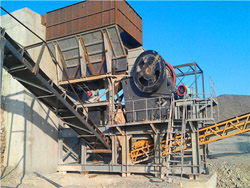
Prediction research for surface topography of internal grinding based
2.2 Analysis of the motion trajectory of internal grinding. It is well known that the surface topography of grinding is the result of the interaction between the grinding grains and the workpiece materials in the grinding arc area [].After the grinding wheel surface modeling and simulation, in order to realize the surface topography simulation of The cutting force is the main factor limiting the productivity of any metal-cutting operation. Among these operations, internal cutting is particularly sensitive to the magnitude and fluctuations of the cutting force on account of the system’s low rigidity; external grinding by a wheel, for example, is much less sensitive.Cutting Forces in Internal Grinding SpringerLink
احصل على السعر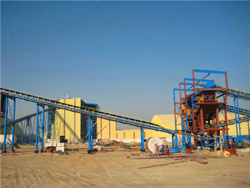
A study of precision grinding of micro-pitch internal thread
The grinding experiments of the PRSM nut samples in Section 2.1 were performed using the CNC internal thread grinding machine (SK7605, produced by Hanjiang Machine Tool Co., Ltd., China), as shown in Fig. 5.The grinding machine belongs to a four-axis numerically controlled machine tool, which uses the German Siemens 828D Unfortunately, examples highlighted in the literature regarding application of this method demonstrate that the aerosol has to be used pointwise in the MQL method, which limits its application considerably due to its requiring free access into the grinding zone (which occurs in processes such as grinding flat surfaces or external cylindricalanalysis of centrifugal MQL supply system potential in
احصل على السعر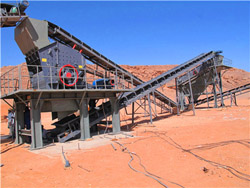
(PDF) The Design of an Infeed Cylindrical Grinding Cycle
systems, including surface grinding, cylindrical grinding, centerless grinding, shoe-centerless grinding, double disk grinding, etc. Inventions 2020,5,x FOR PEER REVIEW 3 of 23In this article, new research on the multi-objective optimization of the process parameters applied to enhance the efficiency in the shoe-type centerless grinding operation for the inner ring raceway of Metals Free Full-Text Multi-Objective
احصل على السعر
CNC Internal Grinder for Mass Production Okuma
A compact, high-speed internal grinder that makes a difference in high-performance production Photos in this brochure include optional specifications. CNC Internal Grinder for Mass Production. 0 0.9 1.5 2.22.4 3 5 2 4 6 kW 8 HK157 HK303 HK503 (3.7 kW) HK307 (7.5 kW) HK507(7.5 kW) 3 4 Grinding examplesThe most popular internal grinder is similar in operation to a boring operation in a lathe: The workpiece is held by a workholding device, usually a chuck or collet, and revolved by a motorized headstock. A separate motor head in the same direction as the workpiece revolves the grinding wheel. Typical examples of coated abrasives areChapter 17: Grinding Methods and Machines American
احصل على السعر
249 13 Grinding Springer
13.2.2.2 Internal cylindrical grinding Internal cylindrical grinding (Figure 13.10) corresponds to external cylindrical grinding in terms of its main criteria. The contact area between workpiece and wheel (Figure 13.11) is greater. The contact length l depends on depth of cut a and the diameter ratio between grind-ing wheel and workpiece.However, the traditional bearing raceway plunge internal grinding process is limited by the process system, and the machined ring is prone to grinding burn, and the OLS5100-3D measurement laser microscope are used to observe and detect the surface morphology of the processed sample. TH702 digital microhardness tester was used to Study on the surface quality of bearing raceway in
احصل على السعر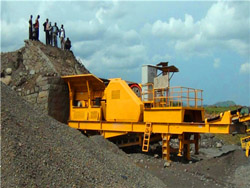
Grinding Machine: Parts, Working, Operations, & More [PDF]
These are the perfect examples of conventional abrasives. The cubic boron nitrite (hardness of 4000-5000) Diamond (hardness of 7000-8000) comes under the category of super abrasives. The Internal grinding operation means, grinding of internal holes or bores. Internal grinding is designed for grinding the surface of bores, whether plain orGrid to optimize cycle internal grinding processing using dynamic programming when taking into account restrictions on the number of switching’s innings 124 P.P. Pereverzev and A.V. Akintseva / Procedia Engineering 129 ( 2015 ) 121 – 126 According to the principle of optimality of the competing moves, you must choose the Automatic Cycles Multiparametric Optimization of Internal Grinding
احصل على السعر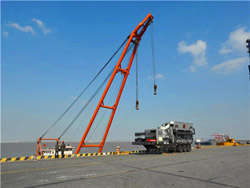
Grinding Processes SpringerLink
Grinding is an essential process in the manufacture of virtually all types of mechanical equipment and cutting tools. For example, the production of rolling element bearings, automotive components, power generation equipment, and computer and electronic components is critically dependent on grinding processes.Examples of high-speed grinding are described including crankshaft grinding and drill-flute grinding. Benefits include not only greatly increased removal rates but also reduced energy requirements to remove a volume of material. The development of these trends is described with references to key publications and underlying principles.Principles of Modern Grinding Technology ScienceDirect
احصل على السعر