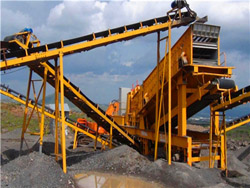
The influence of suspension properties on ultra-fine grinding
The mills traditionally used for wet ultra-fine grinding are high-speed stirred ball mills. The aim of the research was to investigate the influence of the solid (limestone) The effect of ball size and interstitial filling on the performance of dry ball mill grinding was investigated for a limestone-type brecciated uranium ore. The optimum Optimization of Ball Mill Grinding of a Limestone-Type
احصل على السعر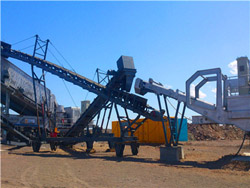
Energy-Model and Life Cycle-Model for Grinding
search work was the examination of main grinding parameters of the limestone particles to determine an empiric energy-model. Dry and wet grinding The size reduction is achieved by attrition, abrasion, and impact between the ore itself and between the ore particles and grinding media [8]. According to Swart et A Technical and Economic Comparison of Ball Mill Limestone
احصل على السعر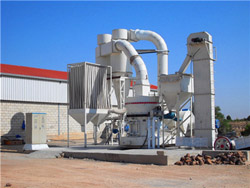
Optimization of Ball Mill Grinding of a Limestone-Type
the performance of dry ball mill grinding was investigated for a limestone-type brecciated uranium ore. The optimum grinding was obtained with the combination of Grinding to below 40 μm in GIS mills or ball mills is usually not recommended. In their product literature, TON give 40 μm as the lower end of the Energy Use of Fine Grinding in Mineral Processing SpringerLink
احصل على السعر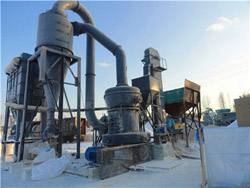
A study of the grinding of magnetite/limestone mixture in a
The grinding of magnetite/limestone mixtures were investigated. • The experimental data were simulated by the population balance model. • The simulated data The majority of pulverised coal boilers use flue gas treatment processes involving limestones that is prepared using horizontal tumbling mills such as ball mills for A new model between the Bond and Hardgrove grindability
احصل على السعر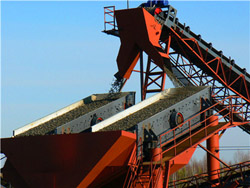
A study of the grinding of magnetite/limestone mixture in a
A pilot-scale grinding technology of ceramic medium stirred mill was proposed in this study. Based on the specific productivity and grinding efficiency, the appropriate grinding parameters were ascertained as follows: material ball ratio of 0.7, ceramic ball medium size ratio (10 mm: 15 mm: 20 mm = 3:2:5), stirring speed of 110 Dry and wet grinding experiments have been carried out with a Bond mill and a laboratory stirred ball mill. During the grinding processes, the grinding time and the filling ratio have been adjusted.Energy-Model and Life Cycle-Model for Grinding Processes of Limestone
احصل على السعر
Energy Use of Fine Grinding in Mineral Processing SpringerLink
Fine grinding, to P80 sizes as low as 7 μm, is becoming increasingly important as mines treat ores with smaller liberation sizes. This grinding is typically done using stirred mills such as the Isamill or Stirred Media Detritor. While fine grinding consumes less energy than primary grinding, it can still account for a substantial part of a mill’s The sequence to evaluate the vertical roller mills consisted of a laboratory jaw crusher, a rod mill and two ball mill stages with differing grinding media. The dimensions and settings of the laboratory mills are given in Table 1 and are illustrated in details in (Boehm and Flachberger, 2006). The jaw crusher used is a standard jaw crusherAn energy based comparison of vertical roller mills and tumbling mills
احصل على السعر
Particle size distribution and structural changes in limestone ground
In this study approximately 8 kg of limestone blocks originated from the country rocks of the Brejuí scheelite mine located in the district of Currais Novos (Rio Grande do Norte, Brazil) were used.Sample preparation occurred in two rounds as follows. The blocks were crushed with jaw and roll crushers until all particles being < 1.7 mm.The SikaGrind® FOR VERTICAL ROLLER MILLS 7 SikaGrind® FOR PORTLAND-LIMESTONE CEMENT Limestone is much easier to grind than clinker. The common intergrinding of limestone and clinker in classical ball mills is there-fore producing a cement of very high surface. The higher the limestone content, the higher the negative CEMENT SikaGrind® FOR VERTICAL ROLLER MILLS
احصل على السعر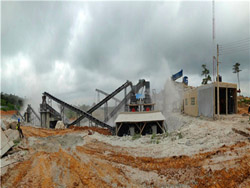
(PDF) Grinding in Ball Mills: Modeling and Process Control
A ball mill is a type of grinder widely utilized in the process of mechanochemical catalytic degradation. It consists of one or more rotating cylinders partially filled with grinding balls (madeA pilot-scale Loesche VRM was used to determine the power required to grind 100 t/h of the same limestone as used at Kusile (work index of 12 kWh/t) with a top size of 19 mm to a 85% and 95% passing 45 µm product. A significant power saving of 39.2% was observed for the dry VRM compared to the wet ball mill (37.7% for the circuit).A Technical and Economic Comparison of Ball Mill Limestone
احصل على السعر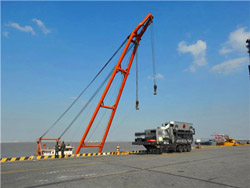
The effects on the grinding parameters of chemical,
On the other hand, the types of mills where the kinetic model was less applied were planetary ball mills (for mica and dolomite) (Matijašic and Glasnovic, 2009, Andrić et al., 2013), stirred ball mills (for quartz and nickel laterite) (Ma et al., 1998, Tong et al., 2013), and electromagnetic mill (for limestone) (Wołosiewicz-Głąb et alThe raw materials were ground from the big particle size to the smallest possible by using multistep grinding. In the laboratory, the common method to be used as the ball mill. This work aims to design a simple horizontal ball mill. Calcium carbonate material from limestone and eggshells powder was ground using the developed ball mill.The design and optimization process of ball mill to reduce
احصل على السعر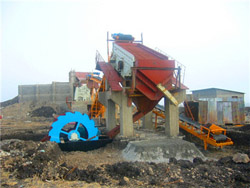
Scale-up procedure for continuous grinding mill design
The design production rate for the circuit is to be 100 TPH at 250% circulating load. For the scale-up design the following steps were required: (1) Perform batch grinding experiments in a reference ball mill. In this example limestone was stage crushed to minus 6.35 mm and screened to ob- tain an 8 10 mesh feed material.The Work Index is used when determining the size of the mill and grinding power required to produce the required ore throughput in a ball mill (Bond, 1961). Simulations and modeling of this testGrindability of binary ore blends in ball mills Request PDF
احصل على السعر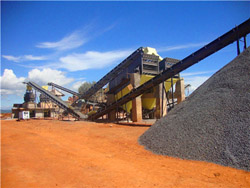
An analysis of the energy split for grinding coal/calcite
Above successful studies about energy split function in the mixture grinding are mainly conducted on a ball mill. However, for the mixture grinding in a ball-and-race mill (Cho and Peter, 1995) or a High Pressure Grinding Roller (HPGR) (Abouzeid and Fuerstenau, 2009), above mentioned mathematical models were not utilized because theGrinding: grind the purchased limestone fragments with particle size less than 20mm in the wet-type limestone ball mill. Classification: pump the limestone slurry flowing out of the ball mill into the classification device to pick out the qualified limestone powder and recycle the coarse ones to the ball mill.Suitable FGD limestone mill, low investment in power plants
احصل على السعر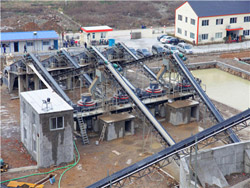
Experimental study on the grinding rate constant of solid materials
The mill used in this experiment is made of alumina with an inside diameter of 144 mm and an inner volume of 2100 cm 3, and the grinding ball is also made of alumina.Five ball diameters ranging between 3 and 30 mm were used, and feed size was varied in the order of 10 −3 to 10 −1 as a ratio of ball diameter. Feed sizes and ball The Gravimetric feeder feeds limestone to Wet ball mill system. The Wet Ball Mill system consists of Wet Ball Mill, Wet Ball Mill Lubrication system, Mill circuit tank with an agitator, Mill circuit Pump, Mill Hydro Quantity of Limestone Grinding Systems 2 sets (1 working + 1 standby) common system 2 Parameters Design Capacity of mill 87.TECHNICAL SPECIFICATION OF WET BALL MILL
احصل على السعر
Parameter effects on wet ultrafine grinding of limestone through slurry
Wet ultra-fine grinding of a limestone powder (< 100 μm) has been investigated in a stirred media mill with respect to the effect of slurry rheology.The grinding results obtained by various parameters (i.e., molecular weight of a dispersant, solids concentration, additive dosage, addition method and beads load) are evaluated in terms It is highly acknowledged for effective and quick grinding in several industries such as limestone, cement, coal, iron ore, chrome ore and many others. The major highlight in the mill is its fully automatic function with PLC control and instrumentation. We are manufacturer and supplier of ball mills since 1980. 400 installations worldwide withClosed and Open Circuits Ball Mill for Cement, Limestone,
احصل على السعر
A study of the grinding of magnetite/limestone mixture in a
Moreover, optimizing ball filling ratio and mill speed appropriately by the AR method, the residence time of feed in the grinding chamber could be reduced and the mass fraction of the desired size was improved during the grinding process [14, 15]. More recently, Chimwani et al. [16] investigated the influence of feed size on ball grinding. AsA limestone ball mill works by grinding materials into a fine powder in a drum that rotates. The drum is powered by a motor, and the motion of the drum causes the balls to lift and fall, grindinghow does a limestone ball mill working LinkedIn
احصل على السعر