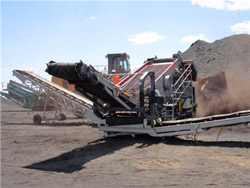
Efficiency of Using Small Diameter Grinding Balls for Cement Grinding
It is shown that the use of ShKh15 steel grinding balls with small diameters to grind cement ensures grinding fineness of 10–11% (residual for a sieve with Ball mills can grind a wide range of materials, including metals, ceramics, and polymers, and can operate on a variety of scales, (PDF) Grinding in Ball Mills: Modeling and Process
احصل على السعر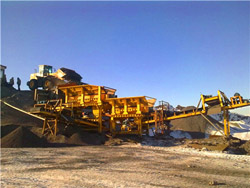
Optimization of a fully air-swept dry grinding cement raw meal ball
It was proposed to operate the mill as a single compartment by eliminating the pre-drying compartment. In this respect, grinding performance of the air-swept ball Operation and Elements of a Closed-Circuit Ball Mill System . Cement ball mills typically have two grinding chambers. The first chamber is filled with larger diameter OPTIMIZATION OF CEMENT GRINDING OPERATION IN
احصل على السعر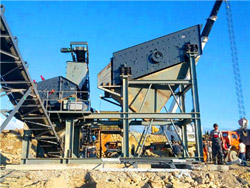
Energy-Efficient Technologies in Cement Grinding
They are used in grinding of cement raw materials (raw meal) (i.e. limestone, clay, iron ore), cement clinker and cement additive materials (i.e. limestone, slag, pozzolan) and coal. Multi-compartment Several energy efficient options for cement grinding are available today such as vertical roller mills, roller presses (typically in combination with a ball mill), and clinker pre-grinders with ball mills. Ball mills have been the Optimization of Cement Grinding Operation in
احصل على السعر
Predictive Controller Design for a Cement Ball Mill Grinding
A total of 40% of the total energy consumption of a cement plant is used in clinker grinding in a ball mill to produce the final cement product . Figure 1 shows the Abstract. To investigate the effects of grinding media shapes on the grinding kinetics of ball mill cement clinker, the grinding effects with ϕ20 mm balls and ϕ20 × 20 The effects of grinding media shapes on the grinding kinetics of cement
احصل على السعر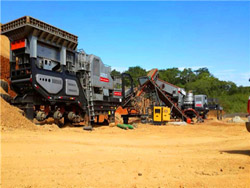
Cement Ball Mill CHAENG
The cement mill is composed of horizontal cylinder, hollow shaft and other parts. The cylinder is long round barrel, and there are grinding media in it. due to the centrifugal force, the materials and At the second and third stages, grinding balls with diameter of 15 to 100 mm are used as a grinding tool. According to VNTP 06-91 (Departmental Norms of Production Engineering) [], the rates of consumption of grinding balls during the production of 1 t of cement were specified, including for the first chamber of the mill, consumption of Efficiency of Using Small Diameter Grinding Balls for Cement Grinding
احصل على السعر
How to choose proper grinding media for your
Steel balls are one of the most widely used grinding media in cement ball mills, their diameters can range from 20mm to 120mm according to different grinding requirements. In a cement ball mill, Grinding of clinker for cement production is often performed in a two chamber ball mill. In the first shorter chamber, raw feed is ground using media consisting of large balls.IMPROVING PRODUCTIVITY BASED ON THE MOVEMENT OF MATERIALS
احصل على السعر
cement-mill PDF SlideShare
Worn out state Normal state Gap Grinding energy 39 kWh/t 32 kWh/t -18% Mill output 65 t/h 92 t/h +40% Table: Grinding energy consumption and mill outlet before and after replacing worn out balls and liner plates 5.0 Coating of Grinding Media: Grinding ball coating which impairs further comminution is the accumulation of finely ground materialBall mills and grinding tools Cement ball mills are typically two-chamber mills (Figure 2), where the first chamber has larger media with lifting liners installed, providing the coarse grinding stage, whereas, in the second chamber, medium and fine grinding is carried out with smaller media and classifying liners.BALL MILLS Ball mill optimisation holzinger
احصل على السعر
What are Mill Balls Made of? ballmillssupplier
Mill balls are an essential component of the ball milling process, which involves the use of a rotating cylindrical vessel filled with large pieces of material, such as ore, ceramic, or metal balls, to crush and grind the material into fine powder.The type and quality of the mill balls used in the process play a significant role in determining the efficiency and effectiveness The effects of material ball ratio, medium size and proportioning, stirring speed, grinding concentration, and medium filling rate [29–32] on the stirred mill grinding were investigated. Under the appropriate grinding conditions of the ceramic-medium stirred mill, extended-continuous grinding and magnetic separation experiments were conductedThe effects of grinding media shapes on the grinding kinetics of cement
احصل على السعر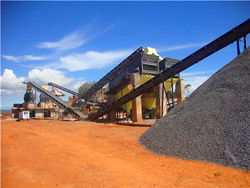
IG PERFORMANCE PARTS Mill Liners for Ball Mills
suit all mill OEM's. Key benefits. Cement grinding. The feed for a cement grinding unit will normally be dry and. needs to be ground to a high degree of fineness. To achieve this efficiently, most mills will be split into two chambers. The first is set up for coarse grinding with a target to grind the feed materials down to around 1 mm.1. Introduction. In the cement industry, grinding is one of the most consuming energy stages in the production units. Around 65% of the total used electrical energy in a cement plant has to be utilized to grind raw materials, coal, and clinker [1,2].Through the process, many variables can affect the efficiency and productivity of Ventilation Prediction for an Industrial Cement Raw Ball Mill
احصل على السعر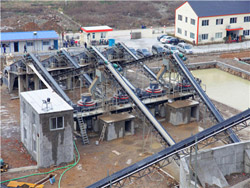
Cement Mill Cement Grinding Machine AGICO Cement Grinding Mill
Cement grinding mill is usually used in the clinker grinding process.It is the final stage in cement production which will directly affect the cement product quality, output and benefits. Clinker particles, gypsum, and other materials in cement grinding machine will be ground together into fine powder to match the fineness of the finished product.Cement Ball Mill. A ball mill is a type of grinder used to grind, blend and sometimes for mixing of materials for use in mineral dressing processes, paints, pyrotechnics, ceramics and selective laser sintering. Ball mill in the cement industry is used to reduce the size of clinker into fine particles also called as cement.Effects of Mill Speed and Air Classifier Speed on
احصل على السعر
What is a Cement Ball Mill? How to Use It? Medium
Cement ball mill is a kind of equipment for further fine grinding of materials, with high fineness. It is widely used in industry, metallurgy, chemical industry, cement and other industries. TheThe cement ball mill is a kind of cement grinding mill.It is mainly used for grinding the clinker and raw materials of the cement plant, and also for grinding various ores in metallurgical, chemical, and electric power Cement Ball Mill Cement Grinding Machine
احصل على السعر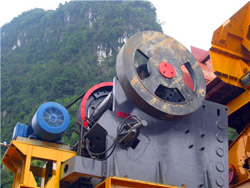
how does a grinding cement mill work LinkedIn
The cement mills are typically comprised of a rotating drum that is partially filled with grinding media, such as balls or rods. As the drum rotates, the grinding media grinds the raw materialsAbstract The results of industrial comparative tests of batches of grinding balls with a diameter of 40, 60, and 80 mm from chromium–molybdenum steel of the nominal grade ShKhM and balls of the current manufacture from rail steel in the first chambers of drum mills while grinding of cement are presented. As the test results showed, total Efficiency of the Use of High-Quality Grinding Balls from
احصل على السعر
Process Training Ball Mill INFINITY FOR CEMENT EQUIPMENT
The better mills on the market have an efficiency of about 8-9 % which means that only 8-9 % of the energy results in grinding and the majority is converted mainly into heat. The ball mill has the worst efficiency of all types of mills on the market. Just 4 % of the energy is used for comminution. Nevertheless when grinding is required the ballCement Ball Mill Structure. When Ball Mill is working, raw material enters the mill cylinder through the hollow shaft of the feed. The inside of the cylinder is filled with grinding media of various diameters (steel balls, steel segments, etc.); when the cylinder rotates around the horizontal axis at a certain speed, Under the action of centrifugal force Ball Mill for Cement Grinding Process
احصل على السعر
Cement Finish Milling (Part 1: Introduction & History)
The finish mill system in cement manufacturing is the second to last major stage in the process, where the feed material is reduced in size from as large as several centimeters in diameter, downThe annual cement consumption in the world is around 1.7 billion tonnes and is increasing by 1% every year [].Cement industries consume 5% of the total industrial energy utilised in the world [].A total of 40% of the total energy consumption of a cement plant is used in clinker grinding in a ball mill to produce the final cement product [].Predictive Controller Design for a Cement Ball Mill Grinding
احصل على السعر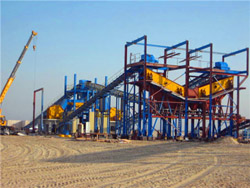
(PDF) Grinding in Ball Mills: Modeling and Process Control
A ball mill is a type of grinder widely utilized in the process of mechanochemical catalytic degradation. It consists of one or more rotating cylinders partially filled with grinding balls (made
احصل على السعر