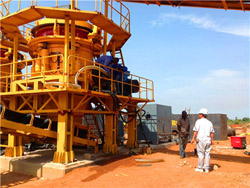
High Energy Planetary Ball Mill Grinding Machine
High-energy planetary ball mill is necessary equipment for mixing, fine grinding, sample preparing, nano-materials dispersing, new product developing and preparing small volume high-tech material production. Find here Ball Mills, Laboratory Grinding Mill manufacturers, suppliers & exporters in India. Get contact details & address of companies manufacturing and supplying Ball Mills, Laboratory Grinding Mill, Large Ball Mills Laboratory Grinding Mill Latest Price,
احصل على السعر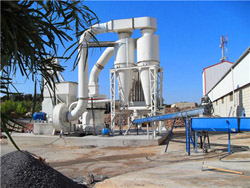
Planetary Ball Mill PM 100 RETSCH highest
The Planetary Ball Mill PM 100 is a powerful benchtop model with a single grinding station and an easy-to-use counterweight which compensates masses up to 8 kg. It allows for grinding up to 220 ml sample material Ball nose end mill grinding; Ball grinding mill; Microtech engineeeeing 5 kw to 50 kw chocolate ball mill, ca Ball mills; Laboratory ball mill; Mild steel 250 kg batch ball mill; Ball Mills Manufacturers & Suppliers in India
احصل على السعر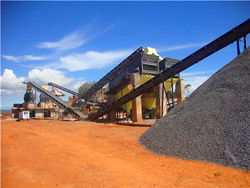
High-Energy Ball Milling an overview ScienceDirect Topics
High-energy ball milling is a ball milling process in which a powder mixture placed in a ball mill is subjected to high-energy collisions from the balls. High-energy ball milling, also Standard Features of Planetary Ball Mill BM 1200+. Stable revolving speed of the gear transmission ensures the consistency and repeatability of the experiment. Planetary Planetary Ball Mill BM 1200+ Top Quality Grinder Machine.
احصل على السعر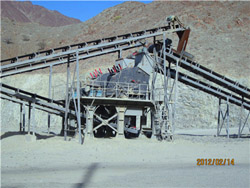
Ball Mill RETSCH powerful grinding and homogenization
High Energy Ball Mills Sample volumes up to 2 x 45 ml Final fineness*: 0.08 µm Easy, ergonomic handling Three different types of mills (ball movement) To the product range A similar result of formation of nanocrystalline Al 2 NbTi 3 V 2 Zr was reported only when high energy ball milling was conducted [Citation 110]. Increased configurational entropy (by increasing the number of components in the alloy) does not appear to accelerate formation of homogeneous phases. Bull Mater Sci. (India). Full article: Mechanical alloying: a critical review
احصل على السعر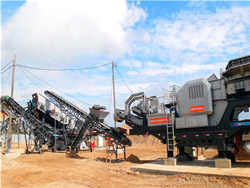
HIGH ENERGY BALL MILL Labindia Analytical
LABINDIA's High Energy Ball Mill MM1600 is a multi-functional bench-top ball mill specially designed for fast preparation of ultra-fine sample with high sample throughput capable of handling 6-384 samples simultaneously in modern laboratory applications, specially for Dry, Wet and Cryogenic grinding can process multiple small sample volumes.Grinds, Mixes, This study presents the utilization of mill scale waste, which has attracted much attention due to its high content of magnetite (Fe3O4). This work focuses on the extraction of Fe3O4 from mill scale waste via magnetic separation, and ball milling was used to fabricate a microwave absorber. The extracted magnetic powder was ground-milled Materials Free Full-Text Structural, Electromagnetic and
احصل على السعر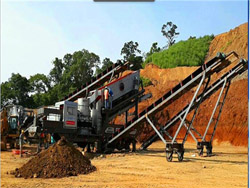
Ball milling as a mechanochemical technology for fabrication
Mechanochemical technique aims to strike a balance between defect formation via ball milling and size adjustment of a solid grain to nanoscale (<1000 nm) (Ullah et al., 2014).During the process, a high-energy mill is employed and a specific powder charge is placed along with a milling medium (Lin et al., 2017).The kinetic energy Nanotechnology-enhanced metals and alloys for orthopedic implants. Lei Yang, in Nanotechnology-Enhanced Orthopedic Materials, 2015. 2.1.2 High-energy ball milling. High-energy ball milling is a mechanical deformation process that is frequently used for producing nanocrystalline metals or alloys in powder form. This technique belongs to the High-Energy Ball Milling an overview ScienceDirect Topics
احصل على السعر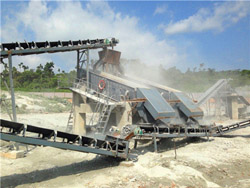
High-energy ball-milling constructing P-doped g-C
The P doping process was conducted out on high-energy ball-milling machine (Retsch, Emax) equipped with circulating cooling water system at 1000 rpm for 1 h. The final mPCN (“m” represents the mass ratio of NaH 2 PO 2 . 2H 2 O to g-C 3 N 4,m =0, 0.3, 0.5, 0.7, 0.9, 1.2 and 1.5) was obtained by washing with deionized water for severalThe purpose of this study was to investigate the effect of working volume in the high-energy ball-milling process on the breakage characteristics (i.e., particle size, morphology, and chemical composition) and adsorption performance of rice straw ash. This study was conducted to confirm working volume issue since this parameter has Working Volume in High-Energy Ball-Milling Process on
احصل على السعر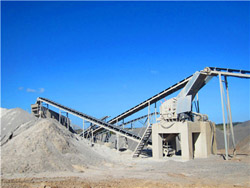
高能球磨法 搜狗百科
高能球磨法(high energy ball milling),又称机械力化学(mechanochemistry) 。一经出现,就成为制备超细材料的一种重要途径。传统上,新物质的生成、晶型转化或晶格变形都是通过高温(热能) 或化学变化来实现的。机械能直接参与或 This was followed by milling in a high-energy ball milling machine for 2 hours in DMSO and subsequent ultra-sonication for one hour to disintegrate the amorphous regions within the fibres. The resulting nanofibers had a diameter within 100 nm and were characterised by a range of techniques including dynamic light scattering, thermal gravimetricBall milling: a green technology for the preparation and
احصل على السعر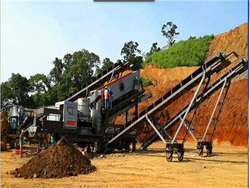
Ball milling: a green technology for the preparation and
The ball mill Ball milling is a mechanical technique widely used to grind powders into ne particles and blend materials.18 Being an environmentally-friendly, cost-effective technique, it has found wide application in industry all over the world. Since this mini-review mainly focuses on the conditions applied for the prep-Taguchi’s method was applied to investigate the effect of main high energy ball milling (HEBM) parameters: milling time (MT), ball to powder weight ratio (BPWR), and milling speed (MS) on the CaCO3 crystallite size. The settings of HEBM parameters were determined by using the L9 (33) orthogonal experiments array (OA). The as-received and Use of Taguchi method for high energy ball milling of CaCO3
احصل على السعر
Ball Mill RETSCH powerful grinding and homogenization
Planetary Ball Mills. Sample volumes up to 4 x 220 ml. Final fineness*: 0.1 µm. Extremely high centrifugal forces result in high energy input. Dry and wet grinding by impact and friction. To the product range. Ultrafine grinding with up to 76 g.The duration of ball milling greatly influences the characteristics of high-silicon–aluminum composite during the ball milling process. This study examines how the microstructure, thermal conductivity, and hardness of a high-silicon–aluminum composite are affected by different ball milling times. We exposed the powder to various durations of Materials Free Full-Text Effect of Ball Milling Time on the
احصل على السعر
Energies Free Full-Text Recent Advances in Ball-Milling
The choice among ball-milling machine types, high or low energy, should also be decided based on research/production focus, and details about ball-milling basics can be found in other references . This review focuses on the recent advances in ball-milled Si and related materials.High-energy ball milling ensures a high concentration of energy on the particles. The authors of [ 93,105 109 ] used a Retsch PM-200 mill with grinding bowls and balls made from yttrium oxide-stabilized zirconium dioxide to disintegrate nonstoichiometric titanium, vanadium, and niobium oxides containing tens of percent of High-energy ball milling of nonstoichiometric compounds
احصل على السعر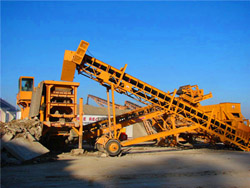
Metals Free Full-Text High-Energy Ball Milling and Spark
Nanocrystalline powder of the CoCrFeNiAl high-entropy alloy was produced by high-energy ball milling (HEBM) and consolidated by spark plasma sintering (SPS). Microstructure and crystal structure transformations occurring in the course of HEBM and SPS processes were explored by Scanning Electron Microscopy (SEM), Energy Dispersive Spectroscopy High-energy ball milling was found to enhance the dissolution of ilmenite in sulfuric acid [72]. Ilmenite was ball milled in both vacuum and air; a 54% dissolution was achieved for ilmenite milled for 10 hours in a vacuum and a 98% dissolution resulted from the ilmenite sample milled for 200 hours.Ball milling A green and sustainable technique for the preparation
احصل على السعر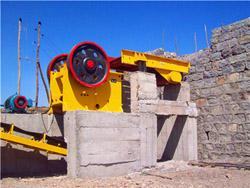
Synthesis of Nanofertilizers by Planetary Ball Milling
The main drawback of the high energy ball milling approach is the non-uniformity of the surface structure formed, i.e., not suitable for preparing uniformly shaped materials. The high energy ball milling devices are of three types namely: shaker mills, attrition mills, and planetary ball mills (Suryanarayana 2001). Shaker mills have a vial
احصل على السعر