
Introduction: Overview of the global iron ore industry
Its production is expected to grow to about 115 Mt/a in 2020. The largest iron ore producer in Russia is Metalloinvest, producing about 40.4 Mt of iron ore For the iron ore with a Fe content of 24.91%, a pilot-scale study of pre-concentration, suspension magnetization roasting, grinding, and low-intensity magnetic separation was conducted, and an iron Novel Technology for Comprehensive Utilization
احصل على السعر
A new approach for recovering iron from iron ore tailings
, Yanjun Li a b Add to Mendeley https://doi/10.1016/j.powtec.2019.11.076 Get rights and content • A new approach for Hematite and magnetite iron ores are the most prominent raw materials for iron and steel production. Most of the high-grade hematite iron ores are typically Comminution and classification technologies of iron ore
احصل على السعر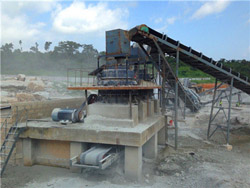
Driving investments in ore beneficiation and scrap upgrading
Upgrading an iron ore concentrate to reach a lower gangue content of compounds such as silicates and alumina may include further comminution, a Abstract. Iron ore tailings (IOTs) are a form of solid waste produced during the beneficiation process of iron ore concentrate. In this paper, iron recovery from IOTs was studied at different points during a Minerals Free Full-Text Recovering Iron from
احصل على السعر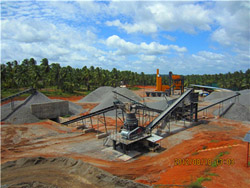
Metals Free Full-Text The Effect of
The work is focused on studying the influence of the ratio of concentrate to iron ore on the phase composition of the iron ore agglomerate. The concentrate has significantly higher iron content than In this study, to improve iron recovery from low-grade iron ores, preconcentration was performed, followed by two separation processes, namely, reverse Improved iron recovery from low-grade iron ore by efficient
احصل على السعر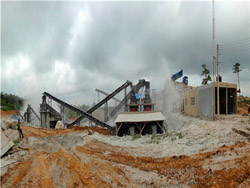
Mechanism of magnetite iron ore concentrate morphology
It can be found that 82 wt% of the iron ore concentrate is composed of magnetite and 11 wt% of hematite, while SiO 2, MgO, CaO, and Al 2 O 3 are present as the main gangues in iron ore concentrate. Total Fe agrees well with reported values in literature (65.5–71.1 wt%) [12], [27], [32], [35].After being treated by the above joint processes, a flotation concentrate with an iron grade of 59.50% and a phosphorus of 0.317% was obtained. The iron recovery and flotation concentrate yield of the total process were 75.39% and 57.52%, respectively. Best set of optimal recovery and iron ore grade acquired are 87.44% and 72.46% withImproved iron recovery from low-grade iron ore by efficient
احصل على السعر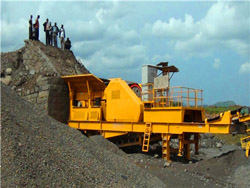
Controlling the rheology of iron ore slurries and tailings with
Section snippets Experimental. The iron ore mineral slurry was sourced from a mine in Pilbara region of Western Australia. The particle size distribution of this slurry measured by a Mastersizer Microplus is as follow: D 10 = 0.28 μm, D 50 = 4.01 μm, D 90 = 76.39 μm, volume means size D[4,3] = 23.82 μm and surface area mean size D[3,2] = The iron ore is first crushed into a powder, mixed with additives and a binder, and rolled into green pellets (10–15 mm in diameter) that are sintered to pellets in a furnace during pelletizing of iron ore [10,11]. The green pellets are thermally treated in the grate and rotary kiln to increase the mechanical strength [12–14].Interaction between iron ore and magnesium additives
احصل على السعر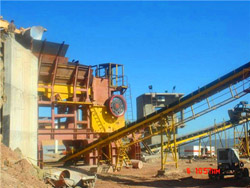
Effect of basicity on the reduction swelling properties of iron ore
The influence mechanism of basicity on the reduction swelling index (RSI) of iron ore briquettes was investigated using the SEM analysis and Factsage 7.3 thermodynamic calculations based on the addition of pure CaO to Bayan Obo iron concentrate. The results revealed that the solid solution of Ca 2+ in the FeO lattice increased with the basicity of Changes in the gradual RSI of pellets prepared from the Bayan Obo iron ore concentrate. 56 (This table is referenced with permission from Taylor & Francis, Ironmaking & Steelmaking, 2021.).(PDF) Kinetics of Reduction in Stages of Pellets Prepared
احصل على السعر
The Relationship Between Mining and Sintering Thermo
The only source of primary iron is iron ore, but before all that iron ore can be turned into steel, it must go through the sintering process. Sinter is created by mixing iron ore concentrate with several additives such as limestone and silica to control the chemistry and then igniting it at 1200°C in a continuous belt-fed furnace.The Sino Iron project started its first full year of commercial operation in 2017 produced and exported approximately 17 million wet metric tons of iron ore concentrate (Citic 2018 Annual Report). In 2018, Sino Iron shipped more than 19 million wet metric tons to CITIC’s special steel plants and other Chinese and Asian steel mills (Citic Comminution and classification technologies of iron ore
احصل على السعر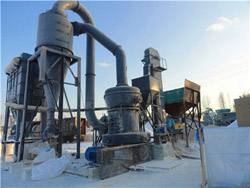
Shift to green steel challenges future of Australian iron ore
Those two nations are particularly relevant for iron ore’s future; China is the world’s biggest steel maker, and India plans to double its steel industry by 2030, albeit with the help of aRanking Iron ore, concentrate, not iron pyrites, agglomerated ranks 4013th in the Product Complexity Index (PCI). Description Iron ore and concentrate are two types of raw materials used to produce steel. Iron ore is a mixture of iron oxides and silicates. Concentrate is a higher quality type of ore that contains less than 63% iron.Iron ore, concentrate, not iron pyrites, agglomerated
احصل على السعر
Kinetics of Reduction in Stages of Pellets Prepared from the
To explore the reduction swelling process of pellets prepared from the Bayan Obo iron ore concentrate, based on the iron oxide reduction theory of pellets, the reduction of pellets prepared from the Bayan Obo iron ore concentrate was analyzed by thermogravimetric experiments and kinetic calculations in three stages. The reason for Iron ore pellets are produced from the iron ore concentrate by pelletizing and sintering and are used as the feedstock for the blast furnace process. Metinvest offers a range of iron ore pellets for the blast furnace process, such as non-fluxed pellets produced by Central GOK with a basicity of 0.1. and 65.5% iron content, non-fluxed pelletsPellet, iron ore concentrste, sintered iron ore: buy from
احصل على السعر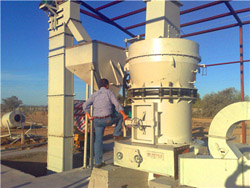
Integrated Production and Distribution Planning for the
ore material into the iron ore concentrate. Also, in order to meet the demand of dierent ore concentrate products from back-end customers in the supply chain, the front-end mining production and mineral processing/dressing production should be coordinated. It is dierent from theThe transformation from traditional iron- and steelmaking technologies to green H2-based new technologies will require an improvement in the quality and purity of iron ore burden materials. Iron ore pellets are essential inputs for producing direct reduced iron (DRI), but the conventional binders, used in iron ore pelletizing, introduce gangue Sustainability Free Full-Text Developing Iron Ore Pellets
احصل على السعر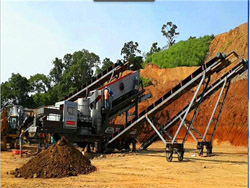
Innovative methodology for comprehensive utilization of iron ore
According to statistics, the annual emission of iron ore tailings is 130 million tons, while every 1 ton of iron ore concentrate should discharge 2.5–3 tons iron ore tailings. Assuming the tailings contain an average of 11% iron, there are 1.41 million tons of metallic iron losses in the tailings [11]. Therefore, the recovery and utilizationBHJ ore, which is known to be a difficult-to-treat iron ore, can be upgraded to a concentrate having 66% Fe at an iron recovery of 72% using reduction roasting-magnetic separation . There are some other reports of successful application of reduction roasting process for low-grade Indian iron ores [ 20 ].Existing and New Processes for Beneficiation of Indian Iron
احصل على السعر
Iron ore facts natural-resources.canada.ca
Iron ore is a combination of minerals from which metallic iron can be extracted on an economic basis. Key facts. In 2021, Canada was the seventh-largest producer of iron ore in the world. Canadian mine production of iron ore in concentrate and pellets was 57.5 million tonnes in 2021, a 2% decrease compared to 2020.Iron ore concentrate pellets are traditionally hardened at high temperatures in horizontal grates and grate-kiln furnaces. However, heat induration requires tremendous quantities of energy to produce high-quality pellets, and is consequently expensive. Cold bonding is a low-temperature alternative to heat induration. Pellets can be cold bonded Cold Bonding of Iron Ore Concentrate Pellets Semantic
احصل على السعر
Characterization and Beneficiation of Dry Iron Ore
Current industrial practice of processing of iron ore fines in India does not involve much beneficiation. However, few plants in India are treating fines during washing, classification, and jigging process [4]. In other parts of the world, iron ore fines are beneficiated for magnetite- and hematite-rich iron ore in * P. Dixit prashant.dixitTable 1 lists the chemical composition of the iron ores and limestone used in the present study. The ores were sourced from different mines around the world with distinct chemical compositions and geological characteristics. Ore 1 was a typical Brazilian hematite ore containing relatively high Fe and low SiO 2 and LOI1000 contents. Ore 2 was an Effect of ore types on high temperature sintering
احصل على السعر