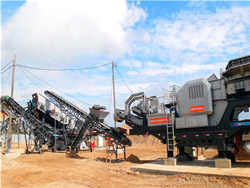
Size recovery curves of minerals in industrial spirals for processing
Spiral concentrators are used in the iron ore industry to separate heavy iron oxide carrier particles from the light silica ones. Losses of iron occur mainly in the Spirals are gravity concentrators used for the concentration of coal, iron oxide ore and heavy minerals. As in any (PDF) Size recovery curves of minerals in industrial spirals
احصل على السعر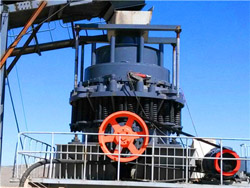
World leader in fine iron ore beneficiation Mineral Technologies
Magnetic beneficiation of fine iron ore, Brazil Optimising metallurgical recovery and grade for fine iron ore Helping to deliver your project vision, we provide core services from The Kirondal iron ore plant of Essar Steel Limited has successfully applied the spiral technique for the beneficiation of iron ore slimes to achieve a pellet feed concentrate. There are other gravity Existing and New Processes for Beneficiation of Indian
احصل على السعر
Vertical mill simulation applied to iron ores ScienceDirect
Abstract. The application of vertical mills in regrind circuits is consolidated. This type of mill is now attracting interest in primary grinding applications, due to its Spirals are widely used in mineral processing as a method for preconcentration and have proven to be metallurgically efficient and cost effective. Spirals have a wide application, WASH WATER OPTIMIZATION ON AN IRON ORE SPIRAL
احصل على السعر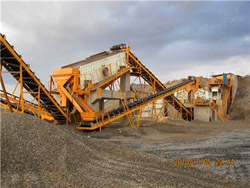
Iron Ore Processing, General SpringerLink
Currently, there are four main types of iron ore deposits, depending on the mineralogy and geology of the ore deposits. These are magnetite, titanomagnetite, The paper demonstrates the application of this methodology to optimize solids concentration in ball milling of an iron ore from Brazil. The wet grinding experiments were conducted in bench Optimization of Solids Concentration in Iron Ore Ball
احصل على السعر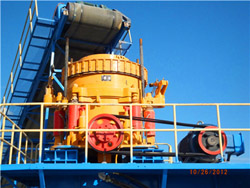
(PDF) Iron ore pelletization ResearchGate
Arrium Australia 0.810 0.810 0.440. 440 Iron Ore. The pelletizing process involves the preparation of ra w materials; the proportioning. and mixing of raw materials; the formation, preheating, and10.2.4 Operation of Vertical Mills. Vertical stirred mills are usually charged with media occupying 80% of the mill volume which is in sharp contrast to tumbling mills that are seldom charged more than 40% of their volumes to allow space for the tumbling action to develop. The stirred mills are charged with a media size of 10–12 mm andStirred Mill an overview ScienceDirect Topics
احصل على السعر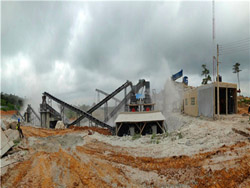
The Use of Process Analysis and Simulation to Identify
The processing of iron ore to recover the valuable iron oxide minerals is commonly carried out using spiral concentrators that separate valuable minerals from non-valuable ones on the basis of the specific gravity of Rake Classifier. The Rake Classifier is designed for either open or closed circuit operation. It is made in two types, type “C” for light duty and type “D” for heavy duty. The mechanism and tank of both units are of sturdiest construction to meet the need for 24 hour a day service. Both type “C” and type “D” Rake ClassifiersTypes of Classifiers in Mineral Processing 911 Metallurgist
احصل على السعر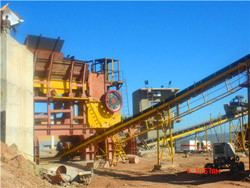
(PDF) ORE SEPARATION BY CLASSIFICATION ResearchGate
Abstract. The ores that are mined from deposits contain the valuable minerals attached to and enclosed in lumps of waste rock. The processing like crushing will disintegrate and unlock the valuesThis research is aimed at the up-gradation of indigenous Pakistani iron ore, i.e., Dilband iron ore (hematite), by utilizing common metallurgical processes. First, the magnetic properties of the ore were determined. Initially, the iron ore samples contained 34 wt. % Fe in addition to other gangue materials. Therefore, the ore was subjected to a Beneficiation of Low-Grade Dilband Iron Ore by Reduction
احصل على السعر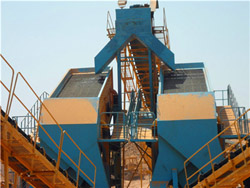
What Is A Spiral In Milling Iron Ore
Gravity Spiral Concentrator Working Principle. Mar 26, 2016The Humphreys Spiral has been successfully applied to recovery of chromite from chrome sands, rutile, ilmenite, and zircon from sand deposits, tantalum minerals and lepidolite from their ores, gravity concentration of base metal ores and in the cleaning of fine coal.Experiments were carried out using a spiral concentrator test rig containing feed conditioner, centrifugal pump and a spiral concentrator with feed to spiral and recirculation. Time samples of concentrate and tails were collected, weighed, dried analysed. Regression equations were developed for Concentrate yield, grade and Modeling and Optimisation of Spiral Concentrator for
احصل على السعر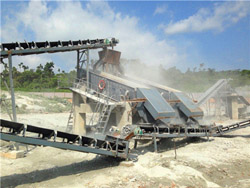
Iron Ore Company of Canada
Milling process. The crushed ore iron content is increased in Labrador City from 38% to a two-thirds ratio by a grinding process. A sequence of four wet mills feeds into a gravity spiral plant to increase the grade. The concentrate production capacity is approximately 23.3 million tonnes per year. PelletizingCrushing, a form of comminution, one of the unit operations of mineral processing. In the field of extractive metallurgy, mineral processing is the process of separating commercially valuable minerals from their ores. [1] Depending on the processes used in each instance, it is often also known as ore dressing or ore milling .Mineral processing
احصل على السعر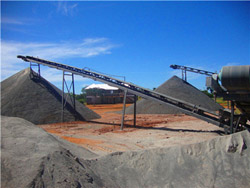
(PDF) Energy conservation and consumption reduction in grinding
milling iron ore by wet stirred mill: analysis and prediction of the particle size distribution, Powder Technol. 378 (2021) 12 18 . [19] X. Zhang, Y. Qin, J. Jin, Y. Li, P. Gao, High-ef ciencyГлавная > Spiral Milling Iron Ore > У нас есть лучший сервис Существуют различные виды горного оборудования с зелеными строительными материалами, вы можете связаться с нашими клиентами в режиме онлайнSpiral Milling Iron Ore
احصل على السعر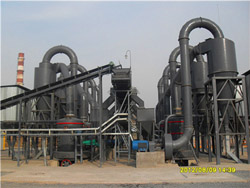
Application of response surface methodology for modeling and
Hence, in search of an alternative source of iron ores, the steel industries are forced to use low-grade ores. The large amount of iron ore slimes accumulated in slime ponds at mine sites alsoThe process Comminution involves size reduction and size-wise classification called as screening/ separation. Milling is one of the most important industrial processes. The electric power(PDF) SIZE REDUCTION BY GRINDING METHODS ResearchGate
احصل على السعر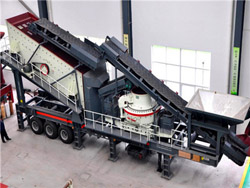
Factors Affect Spiral Classifier Effect
The classifying area in the trough is the decisive factor affects the capacity and partition size of the spiral classifier. Increasing the width of trough, raising the height of overflow weir or reduce the dip angle can all increase the classifying area. The width of classifying trough is decided by the spiral diameter and it should be aboutThe ratio in the output from the three main pelletizing technologies changes depending on practical circumstances, such as iron ore reserves, iron ore types, market demand, and required investment. The ratio for grate-kiln pellets has increased to 55.33% in 2011 from 7.21% in 2000, while the ratio for shaft furnace pellets has dropped to 42.05% Iron ore pelletization ScienceDirect
احصل على السعر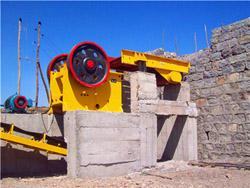
Beneficiation an overview ScienceDirect Topics
11.5.3.1 Beneficiation. Mineral beneficiation begins with crushing and grinding of mined ore for near-complete separation of ore and gangue minerals as well as between ore minerals. Each processing step is designed to increase the grade (concentration) of the valuable components of the original ore.Abstract. The application of vertical mills in regrind circuits is consolidated. This type of mill is now attracting interest in primary grinding applications, due to its higher efficiency when compared to ball mills, which are usually used at this stage. In this study, a coarse sample of iron ore was tested in a pilot scale grinding circuitVertical mill simulation applied to iron ores ScienceDirect
احصل على السعر
HIGH PRESSURE GRINDING ROLLS—A PROMISING AND COST
crushing in semiauotogenous milling, iron ore grinding and final disintegration. High pressure grinding rolls offer solution to a number of key problems in mineral dressing. Majority of ore bodies contain lower grade ore that is harder or difficult-to-process as against previous time; therefore high productivity processing plants need minimi-Fig 3 Types of processing ores. The wet processing (Fig 4) is normally practiced for low / medium grade (60 % Fe to 63 % Fe) hematite iron ore. The wet process consists of multi-stage crushing followed by different stages of washing in the form of scrubbing and / or screening, and classification etc., but the advantage is only partial Beneficiation of Iron Ores IspatGuru
احصل على السعر