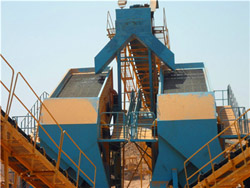
Friction and wear of liner and grinding ball in iron ore ball mill
Grinding balls are an indispensable grinding medium in vertical grinding mills, grinding ore powder to target size. Some were severely worn and unrounded by iron ore from Anshan, China, during grinding operation in the vertical grinding mill (VTM An iron ore concentrate sample was ground separately in a pilot-scale HPGR mill in multiple passes and a dry open-circuit ball mill to increase the specific surface area of particles. Grinding iron ore concentrate by using HPGR and ball mills
احصل على السعر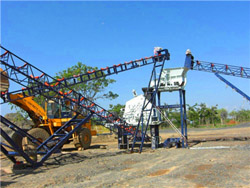
Optimization of Solids Concentration in Iron Ore
Fitting the population balance model of batch grinding to data from a 25.4 cm mill in size reduction of an iron ore from Brazil The present work analyzes the application of the UFRJ mechanistic ball mill model to grinding of iron ore pellet feed in an industrial grinding circuit. In order to Mechanistic modeling and simulation of grinding iron ore
احصل على السعر
Investigation on Iron Ore Grinding based on Particle Size Distribution
The new approach is adapted to identify the retention time (RT) of the iron ore in the mill, and the total RT taken for the blend sample in the Bond’s ball mill is December 2019 PDF On Oct 18, 2020, Seyed Hamzeh Amiri and others published The effects of iron ore concentrate grinding methods (HPGR and Ball mill) on green pellet The effects of iron ore concentrate grinding methods (HPGR and Ball
احصل على السعر
Development of a Novel Grinding Process to Iron Ore
Modern iron ore pelletizing process operations may be divided into two main process sections: feedstock preparation and agglomeration processes. In most Ball milling (BM) and High-pressure grinding rolls (HPGR) are commonly employed for grinding iron ore concentrate [18], [19], [20]. In BM, the particle size was Mechanism of magnetite iron ore concentrate morphology
احصل على السعر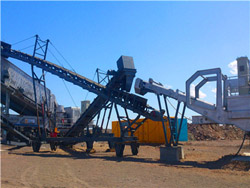
Impact of ball filling rate and stirrer tip speed on milling iron ore
They found that the stirred mill was more beneficial for grinding P80 10–30 μm minerals to liberate more valuable minerals and the grade of iron concentrate was Ball mills are progressively used to grind the ores for particle size reduction and to liberate valuable minerals from the ores. The grinding of ore is a highly energy Estimation of Grinding Time for Desired Particle Size
احصل على السعر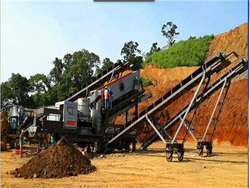
Potential of High-Pressure Grinding Roll (HPGR) for Size
cess parameters during grinding of hard banded hematite quartzite iron ore (BHQ) in HPGR. 2 Materials and Methods A banded iron ore (BHQ) sample from Odisha was used in this study. The bulk sample was crushed to below 20 mm size and was thoroughly mixed, and representative sample was collected by standard conning and Investigation on the particle size and shape of iron ore pellet feed using ball mill and HPGR 909 areas of 500–1600 cm2 g-1.The concentrate must therefore be re-ground in order toInvestigation on the particle size and shape of iron ore
احصل على السعر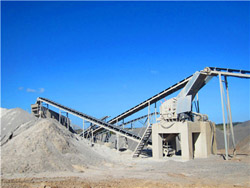
Estimation of Grinding Time for Desired Particle Size
Ball mills are progressively used to grind the ores for particle size reduction and to liberate valuable minerals from the ores. The grinding of ore is a highly energy-intensive process [1,2,3,4].In this process, the size of the particle obtained depends on the energy consumption of the ball mill.The modification of magnetic properties of siderite ore by microwave energy resulted in increasing the efficiency of their magnetic separation. Pre-treatment in a microwave oven with maximum power of 900 W of weakly paramagnetic ore (25.1% Fe, 9.6% SiO 2) was realized with the samples (100 g) of iron spathic ore of particle size Iron ore grindability improvement by microwave pre-treatment
احصل على السعر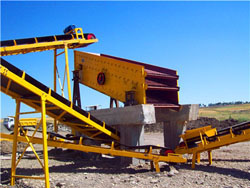
Grinding iron ore concentrate by using HPGR and ball mills
X-MOL. Grinding iron ore concentrate by using HPGR and ball mills and their effects on pelletizing and reduction stages a pilot-scale study. Canadian Metallurgical Quarterly ( IF 0.9 ) Pub Date: ,DOI: 10.1080/00084433.2022.2052522. Seyed Hamzeh Amiri 1,Mohsen Izadi-Yazdan Abadi 2.Currently Autogenous (AG)/Semi-Autogenous (SAG)/Ball mill technology dominates comminution circuit design where grinding to relatively fine sizes is required, eg. the gold, copper, nickel, platinum, silver, lead, zinc and low grade iron ore sectors. High Pressure Grinding Rolls (HPGR) have been found to be more energy efficient than Helping to reduce mining industry carbon emissions: A step
احصل على السعر
(PDF) Effect of wet ball milling on copper ore flotation by
The examined parameters include grinding time, ball load, and solid weight percentage. The collected fractal dimensions for particles ranged from 1 to 2, which is according to the principle ofBall mill is an energy-intensive device for grinding and breaking iron ore particles, which is extensively used in mineral, cement, chemical, and other industries.1–4 In the field of mineral processing, a portion of the energy is converted into heat that will raise the milling tem-perature and breakage characteristics of iron ore willAdvances in Mechanical Engineering 2021, Vol. 13(3) 1–9
احصل على السعر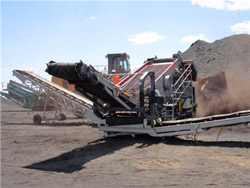
A Review of the Grinding Media in Ball Mills for Mineral
The ball mill is a rotating cylindrical vessel with grinding media inside, which is responsible for breaking the ore particles. Grinding media play an important role in the comminution of mineral ores in these mills. This work reviews the application of balls in mineral processing as a function of the materials used to manufacture them and the Peng Y X, Li T Q, Zhu Z C, et al. Discrete element method simulations of load behavior with mono-sized iron ore particles in a ball mill. Yao F S. Application of large tower mill in cyanide fine grinding of gold concentrate. Gold 离散元法在磨矿设备及参数优化研究中的应用现状 USTB
احصل على السعر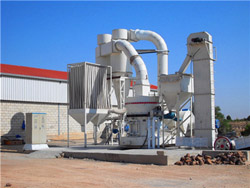
Investigation on the particle size and shape of iron ore pellet
An effect of a grinding method, that is ball mill and high pressure grinding rolls (HPGR), on the particle size, specific surface area and particle shape of an iron ore concentrate was studied. The particle size distribution was meticulously examined by The present work analyzes the application of the UFRJ mechanistic ball mill model to grinding of iron ore pellet feed in an industrial grinding circuit. In order to address the challenge of applying the model to a reasonably fine feed, selected model parameters were back-calculated on the basis of batch grinding tests. The model is then Mechanistic modeling and simulation of grinding iron ore
احصل على السعر
Stirred Mill an overview ScienceDirect Topics
The attrition mill agitator rotates at speeds ranging from 60 rpm for production units to 300 rpm for laboratory units and uses media that range from 3 to 6 mm while ball mills use large grinding media, usually 12 mm or larger, and run at low rotational speeds of 10–50 rpm. Power input to attrition mills is used to agitate the medium, not toThis work assesses the potential suitability of autogenous (AG) and semi-autogenous (SAG) milling through an extensive pilot plant campaign carried out with itabirite iron ores. The effects of ore type, feed size distribution, circuit configuration (open or closed-circuit and two-stage or single-stage), mode of grinding (AG or SAG), ball loadComparing strategies for grinding itabirite iron ores in
احصل على السعر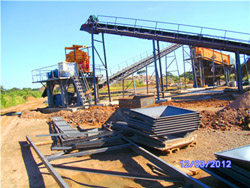
Investigation of iron ores based on the bond grindability test
The present investigation involves the identify the physical properties of three different types of iron ores by using Bond ball mill. The result shows that the maximum Bond work index of 14 KWhAn effect of a grinding method, that is ball mill and high pressure grinding rolls (HPGR), on the particle size, specific surface area and particle shape of an iron ore concentrate was studied.(PDF) Physicochemical Problems of Mineral Processing
احصل على السعر
Study on Quantitative Separation Method of Grinding
Based on batch grinding method and normalization idea, a conical ball mill is used and a quantitative separation method of grinding characteristics of multi-component complex ore is proposed. The results show that the feed sizes of polymetallic complex ore have an obvious influence on the particle size distribution of intermediate grinding The wear on the liners is generated in the grinding zone and the fracture zone, where the liners experience wear caused by grinding balls and iron ore powders. In addition, under the wet-milling condition, there is a slurry generated during the milling. Moreover, the generation of powder or slurry results in severe and complicated wear Friction and wear of liner and grinding ball in iron ore ball mill
احصل على السعر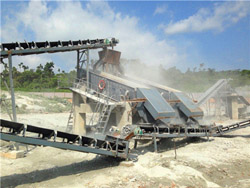
Mechanistic modeling and simulation of a batch vertical stirred mill
Under the optimum grinding parameters, an iron concentrate with an iron grade of 68.18% and an iron recovery rate of 94.17% were obtained by two-stage magnetic separation. The successful case of ceramic medium stirring mill replacing two-stage ball grinding provides a feasible solution for energy conservation and consumption reduction The present work analyzes the application of the UFRJ mechanistic ball mill model to grinding of iron ore pellet feed in an industrial grinding circuit. In order to address the challenge of applying the model to a reasonably fine feed, selected model parameters were back-calculated on the basis of batch grinding tests. The model is then Mechanistic modeling and simulation of grinding iron ore
احصل على السعر