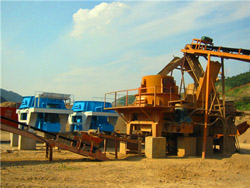
Primary vs. Secondary Crushers: Understanding
The primary crusher is used to reduce the size of the initial rocks, while the secondary crusher further breaks down the smaller pieces into finer materials. Purpose and Benefits of Using Primary and What Is Primary, Secondary, and Tertiary Crushing? There are many ways to crush a rock—and depending on your industry, your location, and the project specifications, the equipment that you use and What Is Primary, Secondary, and Tertiary
احصل على السعر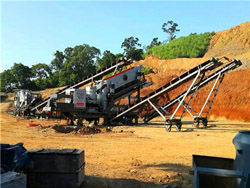
Primary and Secondary Crushing: Understanding
For high-capacity applications, a gyratory crusher or jaw crusher is preferred as the primary crusher, while a cone crusher or impact crusher is preferred as the secondary crusher. The production capacity Primary coal crusher: Used for larger coal size. The primary coal crushers may be of different types such as: (1) coal jaw, (2) coal hammer, and (3) ring granulator. Secondary Primary Crusher an overview ScienceDirect Topics
احصل على السعر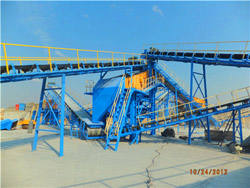
(PDF) COMPARISON OF SECONDARY CRUSHING
The 2S crushing consisted of primary and secondary crushers as Jaw and HSI (horizontal shaft impactor), respectively, while 3S crushing was composed of primary, secondary and tertiary crushers asCrushing is usually a dry process and carried out on ROM ore in succession of two or three stages, namely, by (1) primary, (2) secondary, and (3) tertiary crushers. 13.3.1.1 Primary Crusher an overview ScienceDirect Topics
احصل على السعر
Figure 8: Secondary Crushed vs. Primary Crushed
In some plants, an increase in the particle size of the feed ore is obtained by changing the primary crusher opening set up, changes to the blasting patterns, and partial or fully secondaryThe primary gyratory crushers operate in open circuit while the last stages, either the secondary or tertiary crushers are invariably configured to operate in closed Gyratory and Cone Crusher ScienceDirect
احصل على السعر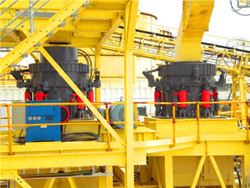
What Type of Crusher Is Best for Primary
Hammermills can be used as a primary crusher in many types of aggregate and industrial applications, including limestone, marble, shale, gypsum, phosphate, bauxite, aluminum dross, uranium, cryolite, Mechanical Crushing and Grinding. Oleg D. Neikov, in Handbook of Non-Ferrous Metal Powders, 2009 Crushers. Crushers are widely used as a primary stage to produce the particulate product finer than about 50–100 mm in size. They are classified as jaw, gyratory and cone crushers based on compression, cutter mill based on shear and hammer Crusher an overview ScienceDirect Topics
احصل على السعر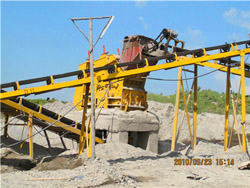
What Are the Differences Between The 7 Types of
A high-quality hammer crusher can keep final material 100% passing a twenty mesh, fifty to sixty percent passing a fifty-mesh screen. Crusher hammers are high chrome content. The hammer service Jaw crushers can be divided into two basic types, single and double toggle. In the single toggle jaw crusher, an eccentric shaft is on the top of the crusher. Shaft rotation, along with the toggle plate, causes a compressive action. A double toggle crusher has two shafts and two toggle plates. The first shaft is a pivoting shaft on the top ofDifferent types of crushers for distinctive needs TON
احصل على السعر
Impact Crusher VS Jaw Crusher:What Are the Differences?
Crusher is an essential equipment in the mineral processing line. The crushing operation is divided into coarse crushing, secondary crushing and fine crushing according to particle size of feedingJaws and gyratories will most often be found in the primary crushing stage, while cones, impactors and roll crushers are most often used in the secondary, tertiary and quaternary crushing stages. Knowing which crushers best fit in each stage, as well as ensuring a properly sized crusher for the task, will help a site achieve optimum crushingDownstream Crushing Options for Secondary, Tertiary and
احصل على السعر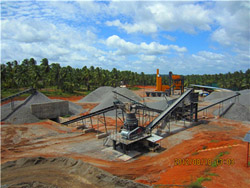
Gyratory and Cone Crusher ScienceDirect
A primary gyratory crusher was required to crush iron ore at the rate of 3000 t/h. The largest size of the run-of-mine ore was 1000 mm. The required product size was less than 162 mm. Manufacturer’s data indicated that the nearest size of gyratory crusher would be 1370 mm × 1880 mm with a cone angle of 18°.Secondary crushing, as you can imagine, is the second stage of material processing following its initial reduction. At this stage, material will flow through perhaps a second impactor crusher or even a cone crusher, which is effective at breaking down these types of material. There are also tertiary and even quaternary stages of crushing thatWhat Is Primary, Secondary, and Tertiary Crushing?
احصل على السعر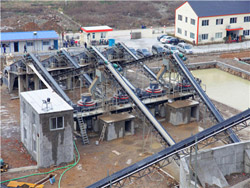
Stone Crushers: A Technical Review on Significant Part of
The cone crusher performance is analyzed by using bonded particle method to study rock breakage mechanics. DEMisusedasatool for the analysis 2012 Quist [20] Sweden 2 Primary crusher Jaw crusher Expt. + Nume FEM analysis can be used as a powerful tool for analyzing the failure of the component in jaw crusher 2013 Rusi´ nski et During the primary crushing operation, boulder size feeds from 20 to 100 in. are reduced to secondary crusher sizes of 1 to 20 in. or mill feed size of .5 to 3 in. Many different types of crushers exist with How it Works: Crushers, Grinding Mills and
احصل على السعر
What is Primary, Secondary and Tertiary Crushing?
Secondary crushing is the second stage of material processing after the first crushing. After that, the product to be crushed will pass through a second crusher or a cone crusher, which isThe difference between the cumulative percentages at the 3.5″ and 1.5″ points on the curve gives us the amount, of such product to be expected from the output of the primary crusher This is 85 minus 43, or Crushing Products Size and Shape -What to
احصل على السعر
Perfecting the Performance of Secondary Crushers E & MJ
Ideally, the deck on the scalping screen should have a cut point equal to the closed side setting (CSS) of the crusher. The feed size to a secondary crusher is typically in the range of 50 mm to 250 mm (up to 300 mm). If the capacity is higher, the acceptable feed size gets larger. After crushing, the product is in the range of 0-60 mm Today, primary crushing is viewed as more important within the balance of production and proper sizing needs. The size and type of the primary crusher should be coordinated with the type of stone, drilling and blasting patterns, and the size of the loading machine. Most operations will use a gyratory, jaw or impact crusher for primary crushing.P&Q University Lesson 7: Crushing & Secondary Breaking
احصل على السعر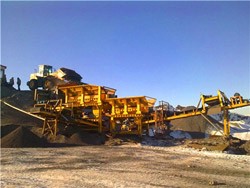
Crusher an overview ScienceDirect Topics
The secondary crusher is mainly used to reclaim the primary crusher product. The crushed material, which is around 15 cm in diameter obtained from the ore storage, is disposed as the final crusher product. The size is usually between 0.5 and 2 cm in diameter so that it is suitable for grinding. Secondary crushers are comparatively lighter inThe gyratory crusher has no rival in large plants with capacities starting from 1200 t/h and above. To have a feed opening corresponding to that of a jaw crusher, the primary gyratory crusher must be much taller and heavier. Also, primary gyratories require quite a massive foundation. Primary crushing with impact crushersCrushers All crusher types for your reduction needs TON
احصل على السعر
Crushers and Their Types IspatGuru
Types of crushers. Crushers are classified into three types based upon the stage of crushing they accomplish. These are (i) primary crusher, (ii) secondary crusher, and (iii) tertiary crusher. The primary crusher receives material directly from run of mine (ROM) after blasting and produces the first reduction in size.It cannot be selected as too large or too small. The nip angle in primary is lower than in secondary . Generally, this value is between 18 and 24 degrees in primary, and between 22 and 28 degrees in The nip angle can be 33 degrees maximum. WHAT ARE THE DIFFERENT TYPES OF JAW CRUSHER? / JAW CRUSHER TYPESWhat Is A Jaw Crusher MEKA
احصل على السعر
AMIT 135: Lesson 5 Crushing Mining Mill Operator Training
The purpose of the primary crusher is to reduce the ROM ore to a size amenable for feeding the secondary crusher or the SAG mill grinding circuit. The ratio of reduction through a primary crusher can be up to about 8:1. Feed: ROM up to 1.5 m. Product: -300mm (for transport) to -200mm (for SAG mill) Feed Rate:
احصل على السعر