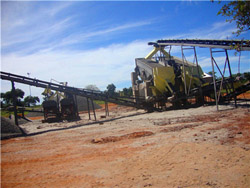
(PDF) Design and Evaluation of Crushing Hammer
January 2019 Authors: Mohamed Ibrahim Faculty of Agriculture Cairo University Abstract and Figures A grain size reduction hammer mill for New grinding mills do not look much different than older mills either. The design process has changed dramatically with computers though. A typical FEA of a grinding mill that would take about 3 hours on How grinding mill design changed over the last 30
احصل على السعر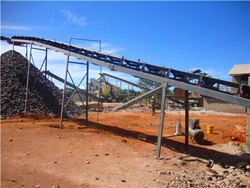
Practical modern techniques for the design of comminution
A number of modern techniques suitable for the design of crushing and grinding circuits are described. The methods are based on extensive use of mathematical models of Schematic of design hammer mill 1-Main frame ,2-Single phase Electrical motor 1 k Watt, 3-Hammer mill housing The crushing (PDF) DESIGN AND EVALUATE OF A SMALL
احصل على السعر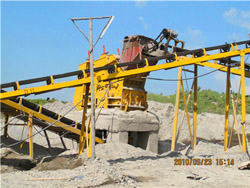
DESIGN AND EVALUATION OF CRUSHING HAMMER
The objective of the present work is to design, fabricate and evaluate low-cost hammer mill during crushing grains and besting its performance with geometric A NEW DESIGN FOR FINE CRUSHING MILLS A. A. Kaminskii UDC 621.926.8 Crushing of materials is one of the principal processes in the technology of A new design for fine crushing mills Springer
احصل على السعر
Comminution Circuit Design and Simulation for the
generation of crushing circuits, with HPGR for tertiary crushing, are starting to replace SAG circuits in hard-rock mining. • Presents a structured methodology for This paper looks at the benefits and problems of total secondary crushing of mill feed and advocates partial secondary crushing as a means of improving grinding efficiency for PROCESS DESIGN AND IMPLEMENTATION TECHNIQUES FOR SECONDARY CRUSHING
احصل على السعر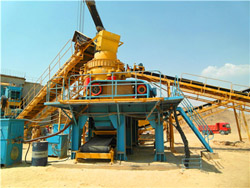
Scale-up procedure for continuous grinding mill design
Scale-up of mills is critical to the design and operation of industrial grinding circuits. This paper presented a scale-up model based on the discrete element method Grinding Mills. Barry A. Wills, James A. Finch FRSC, FCIM, P.Eng., in Wills' Mineral Processing Technology (Eighth Edition), 2016. 7.5.2 Circuit Operation. Grinding circuits Grinding Mill an overview ScienceDirect Topics
احصل على السعر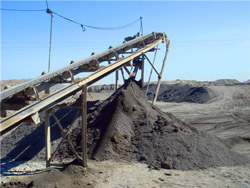
(PDF) Design and Evaluation of Crushing Hammer
A grain size reduction hammer mill for crushing corn (Zea mays L.) was designed depending on variety characteristics and by using computer aided design “ANSYS” software. Suitability ofIn addition, the shape, relative motion, and form of rollers on outer rings and solid plate provide good conditions for moving the load in the preparation, grinding, and ejection space of the product, subject to crushing, uniform, gentle runs of loads, deformations and displacements to a given product dimension, for example, below 10 µmA study of operating parameters of a roller mill with a new design
احصل على السعر
Sustainability Free Full-Text Optimization Issues
Our paper presents the hammer mill working process optimization problem destined for milling energetic biomass (MiscanthusGiganteus and Salix Viminalis). For the study, functional and The present literature review explores the energy-efficient ultrafine grinding of particles using stirred mills. The review provides an overview of the different techniques for size reduction and the impact of energy requirements on the choice of stirred mills. It also discusses the factors, including the design, operating parameters, and feed material Energy-Efficient Advanced Ultrafine Grinding of Particles
احصل على السعر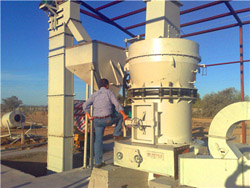
Comminution and classification technologies of iron ore
The grinding occurs under exposure of mechanical forces that break the structure by overcoming of the interior bonding forces of solid matters. There are many different types of grinding mills that process many types of materials. 8.3.2.1. Tumbling mills. The term “tumbling mill” encompasses many different grinding devices used in the industry.HPGR crushing may provide a profitable alternative or addition to a grinding circuit allowing the crushed pebbles to be bled to the subsequent downstream ball mill grinding and beneficiation(PDF) PEBBLE CRUSHING BY HPGR ResearchGate
احصل على السعر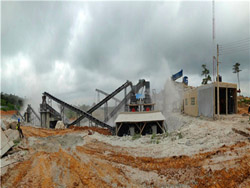
Energy-Efficient Technologies in Cement Grinding IntechOpen
The energy consumption of the total grinding plant can be reduced by 20–30 % for cement clinker and 30–40 % for other raw materials. The overall grinding circuit efficiency and stability are improved. The maintenance cost of the ball mill is reduced as the lifetime of grinding media and partition grates is extended. 2.5.Cement production process typically involves: •. grinding limestone (and other raw materials to achieve the right chemical composition) to about 90% passing 90 μm in a dry circuit, •. making cement by the chemical reaction between the components of the ground mixture. This chemical reaction occurs at high temperature in a rotary kiln, •.Cement grinding optimisation ScienceDirect
احصل على السعر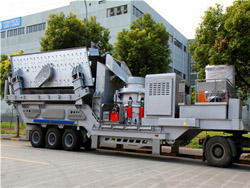
Analiza efektywności mielenia w młynach kulowym i
hindering the screening and crushing process as well as processing costs. An example of changes in existing technological systems resulting in lower costs is the Mount Isa processing plant [1]. The Mount Isa processing plant started working with a grinding system based on two-stage crushing in jaw crushers and grinding in rod mills.In the ball mill machine (Figure 5), the crushing process is due to steel or rubber balls placed inside a rotating cylindrical casing. As the cylinder rotates about its axis, the balls rotate to form an impact against the glass to crush it. Design of the Ball Mill Glass Crusher 4.1. Introduction The grinding process in the ball mill isFinite Element and Multibody Dynamics Analysis of a Ball Mill
احصل على السعر
Selected Aspects of Modelling and Design
An analysis of construction was conducted in this study, and the guidelines for designing roller mills used commonly in the agri-food, chemical, power and construction industries were presented. Quick These mills typically grind ROM ore in a single stage. A large example of such a mill was converted from a single-stage milling application to a semiautogenous-ball-mill-crushing (SABC) circuit, and the application is well described (Mainza et al., 2012). This section refers to high-aspect AG/SAG mills.Comminution Circuits for Gold Ore Processing ScienceDirect
احصل على السعر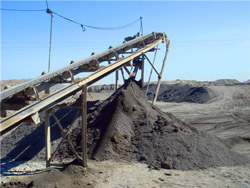
Analysis of vertical roller mill performance with changes in
The vertical roller mill (VRM), including powder separation and crushing sub-systems, is used extensively for intermediate crushing of minerals in several industries such as cement, electric power, and chemical. Compression crushing is also the main crushing mechanism in the VRM, but there is also shear force between grinding roller ment of grinding media which results in collisions is affected by mill design, mill speed, mill filling and grinding media properties[14]. The collision impact cause particle breakage due to the kinetic and potential energy of the grinding media. For a successful collision to happen, the grinding media should attain a minimum collision energyGrinding Media in Ball Mills-A Review Preprints
احصل على السعر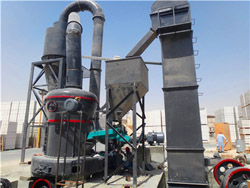
mill/sbm grindingcrushing mill design.md at main crush2022/mill
Contribute to crush2022/mill development by creating an account on .For a specific design of the rotating screw, the compression ratio is dependent on the channel depth. Apart from the compression ratio, the particle size is controlled by several other variables such as temperature, feed rate, rotation rate, and so forth. Grinding mill, rolling mill, rotary crushing millGrinding of Waste Rubber Rubber Recycling: Challenges
احصل على السعر
Design, Construction, and Operation of a High-Energy Mill
A high-energy mill was designed and built with the purpose of processing magnesium (Mg) powders. The main characteristics of the mill are grinding capacity of 1 kg and demolition elements of 10 kg; it has a distributed form to the interior ten blades of similar geometry, six of which are of the same size and four of them were increased in length in ME Elecmetal analyzes customer operations to determine the ideal combination of design and materials to achieve the optimal performance of their equipment. Whether it is an AG, SAG, ball, tower or rod mill, our innovative liner and alloy designs deliver proven performance, while minimizing costly downtime. We work closely with our customers on Grinding ME Elecmetal
احصل على السعر
Optimisation of secondary crushing stage before Single Stage SAG mill
SAG mill power consumption as a function of the proportion of -152 +25mm in the fresh feed for SAG mills of different diameters (after Casili A. and Silva N.,2015) Mill feed size distribution
احصل على السعر