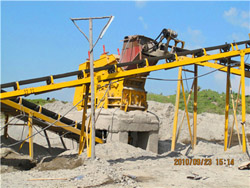
Raw Mix Preparation ABB
OptimizeIT Raw Mix Preparation. Raw mix preparation is the quality key control parameter upstream for stable, continuous manufacture of high qua- lity clinker and cement. Downstream quality and up to 5%. stable coating in the kiln with stable raw meal fed to The cement raw mill is the primary piece of equipment used in the modern cement industry for the raw meal production process. As a result, it is critical to investigate the Full article: Evaluation of optimization techniques for
احصل على السعر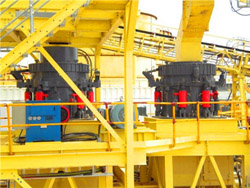
Evaluation of optimization techniques for predicting exergy
cement raw mill is the primary piece of equipment used in the modern cement industry for the raw meal production process. As a result, it is critical to investigate the exergy Raw material preparation (RM—a single block in Figure 2) is a subsystem, where the raw material feeds (Rm f —the material stream in Figure 2) Parametric Studies of Cement Production Processes
احصل على السعر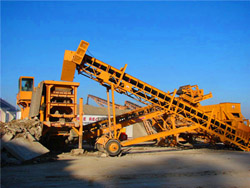
Quality in sample preparation Herzog Maschinenfabrik
HERZOG delivers a wide variety of sampling equipment for powder and lump material like, e.g., clinker or limestone. Usually, samplers are installed for the following material: Raw The preparation process of cement raw meal. Currently, there are four methods for determining the composition content of cement raw meal: the wet chemical method [ 6 ], X-ray fluorescence Processes Free Full-Text Rapid Analysis of Raw Meal
احصل على السعر
Automated sample preparation in a cement plant- Part I:
Raw meal analysis and given raw material chemistry are applied to calculate set points for each individual raw material belt feeder. The user simply defines his target chemistry for Indirect emissions from different cement producing stages were also estimated by using regional electricity emission factor. In raw meal preparation and Analysis on differences of carbon dioxide emission from
احصل على السعر
(PDF) Evaluation of optimization techniques for predicting exergy
In cement production, raw meal preparation and energy consumption are extremely important for cost reduction. However, few studies have examined the The cement production process includes raw meal preparation, clinker calcination, grinding and packaging, in which raw meal preparation has a tremendous Fast determination of oxides content in cement raw meal using
احصل على السعر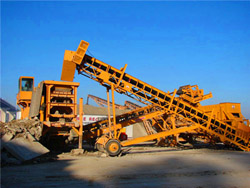
Effects of Preparation of Cement Raw Meal with Carbide Slag on
The results indicate that the exhaust gases emitted from the calcination process of raw meal prepared with carbide slag is mainly composed of CO2 and water vapor, and is free from harmful gases.Composite cements are the key to reducing your emissions. Simply by using 30% more environmentally friendly additives in your OPC mix reduces CO2 by 27%. Whether for bulk delivery or bagging, our MULTICOR mass flow meter makes the sustainable cement revolution possible by providing the precision automatic weighing and feeding that Cement processing equipment Schenck Process
احصل على السعر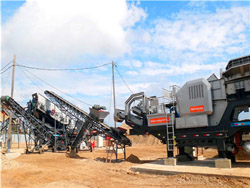
Modernizing cement manufacturing in China leads to substantial
India has state-of-the-art equipment for crushing, raw meal grinding, and finish grinding 53,54, leading to greater electricity savings. Fig. 4: CO 2 emissions and electricity use per ton ofIn recent years, the tube mill has gradually been replaced by roller mill and other equipment, became the main equipment of cement grinding in cement cement manufacturing plant. While in raw meal grinding, with the mature use of vertical mill and roller mill, the power consumption of grinding one ton raw meal has been reduced from Raw Material Preparation in Cement Manufacturing Plant AGICO
احصل على السعر
Parametric Studies of Cement Production Processes Hindawi
Raw material preparation (RM—a single block in Figure 2) is a subsystem, where the raw material feeds (Rm f —the material stream in Figure 2) are converted into the raw meal or raw-mix (Rm x).The proportioned raw material is dried, homogenized, and fine-grounded to the required size by the raw mill.The results show that approximately 2.48t, 4.69t, and 3.41t of materials are required to produce a ton of the product in raw material preparation, clinker production, and cement grinding stages(PDF) Analysis of material flow and consumption in cement production
احصل على السعر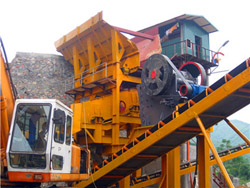
Monitoring Fineness of Raw Meal and Cement by Grain Size
Monitoring and controlling the grinding grade is an essential factor in maintaining cement quality and production efficiency. This must be done during the grinding process from raw material to raw meal, and also during fine grinding of burnt clinker with additional core components or additives. Energy consumption accounts for around half Engr Sajid Chaudhary. Cement is a powdery substance made by calcining lime and clay, mixed with water to form mortar or mixed with sand, gravel, and water to make concrete. Cement is made by grinding together a mixture of limestone and clay, which is then heated at a temperature of 1,450°C. What results is a granular substance called "clinker(PDF) Production of Cement Engr Sajid Chaudhary
احصل على السعر
A Review on Pyroprocessing Techniques for Selected Wastes
Raw material preparation is an electricity-intensive production step requiring about 25 to 35 Ball mills have been used as the main grinding equipment for finished cement production for over 100 “Reactivity of calcined cement raw meals for carbonation,” Powder Technology, vol. 354, pp. 338–347, 2019. View at: PublisherThe results indicate that the exhaust gases emitted from the calcination process of raw meal prepared with carbide slag is mainly composed of CO2 and water vapor, and is free from harmful gases. However, a lot of water in carbide slag during the pre-heat and decomposition process under high temperature would accelerate the corrosion of Effects of Preparation of Cement Raw Meal with Carbide Slag
احصل على السعر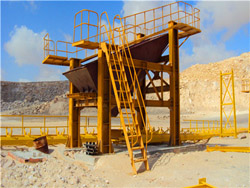
Automated sample preparation in a cement plant- Part I: From
Raw meal analysis and given raw material chemistry are applied to calculate set points for each individual raw material belt feeder. The user simply defines his target chemistry for the raw meal by using the cement moduli LSF Lime Saturation Factor),SM (Silica Modulus) and AM (Alumina Modulus). Further constraints likeWhile, in the wet process, crushed raw meals are sent in wet grinding mills where a lot of water is added, these get ground to a fine, thin paste. Homogenizing silo is a device used to mix raw meals by compressed air to get uniform chemical composition and fineness. It is the last homogenizing step in the line of the raw meal preparation processes.Cement Manufacturing Plant Cement Plant AGICO EPC Cement
احصل على السعر
Dry Process Of Cement Manufacturing Dry Cement
The new dry-process of cement manufacturing technology makes good use of the limestone resources discarded in the traditional mining method and applies the pre decomposition technology, suspension preheating Cement Raw Meal Preparation Production For different materials, the choice of equipment is not the same, we provide clients with a variety of professional cement equipment. Cement CrushersCement Manufacturing Equipment for Sale AGICO Cement
احصل على السعر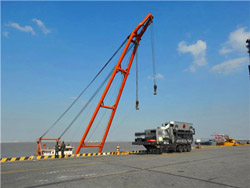
Feasibility study on utilization of copper tailings as raw meal and
(1) 20.31 wt% copper tailings as raw meal and 15 wt% copper tailings as addition was used to prepare copper tailings ordinary Portland cement. 35.31 wt% copper tailings were converted into low-cost and low-carbon cement that meets PO 42.5 grade.(2) Copper tailings cement was evaluated in terms of environmental and economic aspects.Materials preparation and sintering. At first, the raw meal of commercial type I Portland cement was intended to use for clinkerization by only microwave technique with a microwave furnace (CEM, MAS7000, USA, 900 W, max temp. 1200 °C). This furnace has a limitation of a maximum temperature of 1150 °C which was used for the microwave Development of microwave-assisted sintering of Portland cement raw meal
احصل على السعر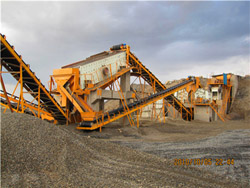
Know All About Cement Manufacturing Process in India mycem cement
Raw material preparation / raw mix preparation. Crushing. Homogenization. Proportioning of raw materials. Grinding. In preheater the temperature of raw meal rises to 900oC to 1000oC and nearly 90% Calcinations Heidelberg Cement offers insights into modern techniques and industry-leading practices. mycem Cement .1.1 Oxygen control. The oxygen at the calciner outlet is controlled through the calciner draft, in the same way as the oxygen at kiln inlet is controlled by the kiln draft. A normal target value for the oxygen after calciner (bottom cyclone exit) is 1 1.5 %.Kiln Control and Operation INFINITY FOR CEMENT EQUIPMENT
احصل على السعر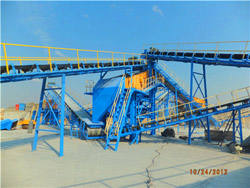
High temperature cement raw meal flowability ScienceDirect
Section snippets Equipment. For the purpose of investigating the flowability of cement raw meal at temperatures up to 850 °C, a monoaxial shear tester was constructed from high temperature resistant steel.The monoaxial shear test cell was chosen due to its simple geometry, compatibility with an existing muffle furnace, and low cost [3], Fig.1 Near infrared spectrum of cement raw meal Table 1 Test set cement raw meal sample composition Oxide Subset No Max/% Min/% Avg/% SiO 2 Calibration set 80 13.79 11.37 12.77 Validation set 16 13.36 11.94 12.97 Al 2 O 3 Calibration set 80 3.44 2.52 3.01 Validation set 16 3.25 2.6 3.12 Fe 2 O 3 Calibration set 80 2.12 1.78 2.01 Validation setRapid Detection of Cement Raw Meal Composition Based on
احصل على السعر