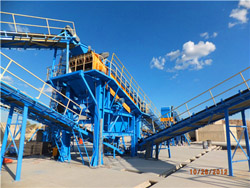
Different Effects of Wet and Dry Grinding on the
The effect of wet grinding on the activation of IOTs was evaluated through ion leaching from an alkaline solution and the reactivity index. Additionally, a detailed It indicated that wet grinding together with a chemical activator could better improve the activation effect of the chemical activator than the direct addition. These Effects of wet grinding combined with chemical activation on
احصل على السعر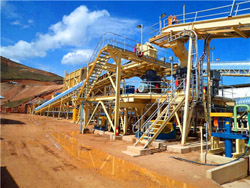
Different Effects of Wet and Dry Grinding on the Activation of Iron Ore
Abstract References Citations Supplementary Data Improving the activity of Iron Ore Tailings (IOTs) to utilize them as a mineral admixture in cement-based minerals is still T Q, Zhu Z C, et al. Discrete element method simulations of load behavior with mono-sized iron ore particles in a ball mill Lee H, Lee Y. Some breakage 离散元法在磨矿设备及参数优化研究中的应用现状 USTB
احصل على السعر
Comminution and classification technologies of iron ore
Introduction Hematite and magnetite iron ores are the most prominent raw materials for iron and steel production. Most of the high-grade hematite iron ores are PDF On Jan 1, 2022, Yingchun Yang and others published Preparation of Micro-Iron Ore Tailings by Wet-Grinding and Its Application in Sulphoaluminate Cement Find, read and cite all the...(PDF) Preparation of Micro-Iron Ore Tailings by
احصل على السعر
Optimization of Solids Concentration in Iron Ore
The paper demonstrates the application of this methodology to optimize solids concentration in ball milling of an iron ore from Brazil. The wet grinding experiments were conducted in bench Modern iron ore pelletizing process operations may be divided into two main process sections: feedstock preparation and agglomeration processes. In most Development of a Novel Grinding Process to Iron Ore
احصل على السعر
The effects of dry grinding and chemical conditioning during grinding
The results show that the energy consumption of dry grinding is ore quality sensitive and can possibly be considerably closer to the wet grinding depending on the target p80 (more equal with increasing particle size) and other grinding parameters, even with a ball mill. 3.2. Flotation results3.2.1. Pyhäsalmi Sulphide ore3.2.1.1.Crushing and grinding. First step in the process is crushing and grinding coupled with wet or dry size-classification of run of mine (ROM) ore. This is required to prepare feed for beneficiation of ore. Final product size may depend on ROM characteristics (obtained by characterization study) and the requirement of iron–steel making processIron ore beneficiation: an overview ScienceDirect
احصل على السعر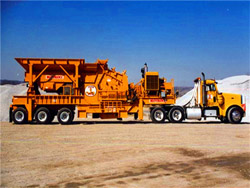
Preparation of Micro-Iron Ore Tailings by Wet-Grinding and
Abstract: Herein, micro iron ore tailings (micro-IOTs) were prepared by wet-grinding and applied to improve sulphoaluminate cement (SAC) performance. The physicochemical properties of micro-IOTs were investigated by particle size analysis, XRD, and XPS. The hydrates trait and the hydration mechanism of micro-IOTs-SAC composite were studied The mixing speed and temperature were the same as those in the gold powder leaching experiment. In the dry grinding process, 50 g of roasted gold concentrate was ground in a planetary mill for 5 min. The wet grinding process was performed in a ball mill for 10 min. The particle size distributions of the wet and dry milled ore are shown in Use of dry grinding process to increase the leaching of gold
احصل على السعر
Different Effects of Wet and Dry Grinding on the Activation
Additionally, a detailed comparison between Dry-grinding Iron Ore Tailings (DIOTs) and Wet-grinding Iron Ore Tailings (WIOTs) was made. This comparison was based on particle characteristics, crystal structures, chemical structure, and surface properties. The results showed that the particle size of IOTs reduced rapidly during wet grinding.also more significant during the wet grinding process than during the dry grinding process. Moreover, both prolonged dry and wet grinding could destabilize the Si-O bond and decrease the surface binding energy. KEYWORDS Wet grinding; iron ore tailings; particle characteristics; mineral admixture 1 Introduction Iron Ore Tailings (IOTs) refer toDifferent Effects of Wet and Dry Grinding on the
احصل على السعر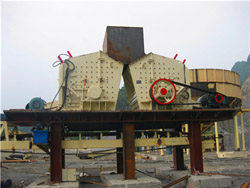
Iron Ore Pelletization Technology and its Environmental
The Process would be generating any Hazardous Solid disposable waste which is also ideally suitable for brick making and would be delivered to local brick makers. 6.6. Noise level The Iron Ore Crusher & Ball Mil wet Grinding unit will be the major equipment where maximum noise generation will be taking place.The earliest industrial application of high pressure grinding rolls (HPGR) at comminution was in 1984 in the cement industry. Since then, the equipment has been widely applied in mining activities. Despite the rapid spread across the industry, several challenges are still present in the equipment’s application, especially considering the complex ore Development of a Novel Grinding Process to Iron Ore
احصل على السعر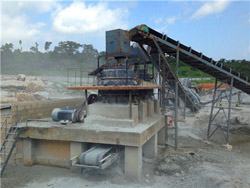
Process for iron ore pellets production Google Patents
The present invention concerns a process for iron ore pellets production comprising at least one iron ore crushing stage in a roller press for the production of iron ore pellets. The crushing stage(s) can be done prior or after grinding, or still defined by successive passages of the material through the foregoing crushing stage.Nowadays, the HPGR (high-pressure grinding rolls) is an intermediate step between filtering and balling in the most modern iron ore pelletizing operation. The operation debottlenecks filtering process and reduces pressure over the typical milling process to control particle size to the balling. The present study evaluated aspects of microwave Iron Ore Concentrate Particle Size Controlling Through
احصل على السعر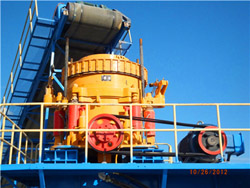
Different Effects of Wet and Dry Grinding on the
Different Effects of Wet and Dry Grinding on the Activation of Iron Ore Tailings Yingchun Yang1,*, Liqing Chen1 and Yuguang Mao2 1College of Engineering, Anhui Agricultural University, Hefei, 230036, China 2College of Civil Engineering, Hunan University, Changsha, 410082, China *Corresponding Author: Yingchun Yang. Email: The consequence is that the mill charges initiate to centrifuge at a higher speed. Due to water content in the wet grinding process, the critical speed for tests A and B (lower ball percentages) happens in the speed range 0.6–0.8. An investigation conducted on magnetite ore grinding with a dry HPGR machine to reduce the particle size fromGrinding SpringerLink
احصل على السعر
Different Effects of Wet and Dry Grinding on the Activation of Iron Ore
In addition, WIOTs had a higher activity index compared to DIOTs. The storage of lattice distortions in the quartz crystal structure was also more significant during the wet grinding process than during the dry grinding process. Moreover, both prolonged dry and wet grinding could destabilize the Si-O bond and decrease the surface binding energy.Pelletization begins with the grinding and cleaning of the iron ore to meet the desired chemical quality. green pellet strength. 1 daN was chosen for the calculation of plastic deformation because it is generally known that wet iron ore green pellets must withstand this pressure in order for the pelletizing process to operate economicallyBinding mechanisms in wet iron ore green pellets with a bentonite
احصل على السعر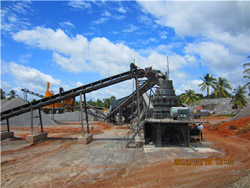
Minerals Free Full-Text Effects of Different Grinding Media
Different milling conditions, such as wet or dry, and use of different grinding media have a great impact on the flotation performance of sulphide minerals. In the present study, the effects of wet and dry grinding and the use of different grinding media, such as mild steel (MS) and stainless steel (SS), were investigated on a Cu-sulphide ore. The effect of the grinding time, the grinding media filling rate, and the powder filling rate on the grinding of lithium ore in a lab scale ball mill was investigated. The results show that the grinding process of lithium ore is highly consistent with the non-first grinding kinetic equation, while the breakage rate decreases with the reductionWet grindability of an industrial ore and its breakage
احصل على السعر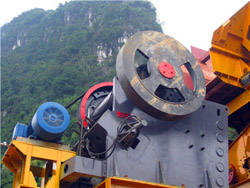
Estimation of Grinding Time for Desired Particle Size
Iron ores obtained from different sources differ in their chemical and physical properties. These variations make the process of grinding a difficult task. The work carried out in this context focuses on three different samples of iron ore, viz., high silica high alumina, low silica high alumina, and low silica low alumina. The grinding process for all An effect of a grinding method, that is ball mill and high pressure grinding rolls (HPGR), on the particle size, specific surface area and particle shape of an iron ore concentrate was studied.(PDF) Physicochemical Problems of Mineral Processing
احصل على السعر
Towards waterless operations from mine to mill ScienceDirect
Magnetic separation is often carried out as a wet process but there are numerous examples of dry magnetic separation in the mineral processing industry, especially in iron ore and coal beneficiation (Andre et al., 2019, Bunting, 2022, Miceli et al., 2017, Tripathy et al., 2017, Zong et al., 2018). Other example applications include the Companhia Vale do Rio Doce (CVRD) is a world leader in production of iron ore, from its deposits in Brazil. It registered a profit of about $5 billion during 2005, more than a 60% increase from 2004, from sales of $16 billion. This resulted from increased prices of iron ore products, 71.5% higher for lump ore and 86% for pellets, plus increasesSimulation of wet ball milling of iron ore at Carajas, Brazil
احصل على السعر