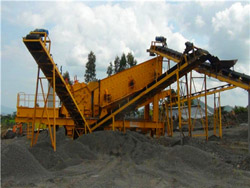
(PDF) Grinding in Ball Mills: Modeling and Process
PDF The paper presents an overview of the current methodology and practice in modeling and control of the grinding Ball milling is a simple, fast, cost-effective green technology with enormous potential. One of the most interesting applications of this technology in the eld of cellulose is the Ball milling: a green technology for the preparation and
احصل على السعر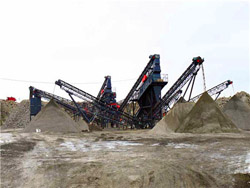
A Review of the Grinding Media in Ball Mills for Mineral
Grinding media play an important role in the comminution of mineral ores in these mills. This work reviews the application of balls in mineral processing as a ball mill into their objective limits respectively, while guaranteeing producing safely and stably. The grinding process is essentially a multi-input multi-output Intelligent optimal control system for ball mill grinding
احصل على السعر
Materials Development Using High-Energy Ball
High-energy ball milling (HEBM) of powders is a complex process involving mixing, morphology changes, generation and evolution of defects of the crystalline lattice, and formation of new phases. This Tumbling ball mills or ball mills are most widely used in both wet and dry systems, in batch and continuous operations, and on small and large scales. Grinding elements in ball mills Ball Mill an overview ScienceDirect Topics
احصل على السعر
[PDF] Grinding in Ball Mills: Modeling and Process Control
Abstract The paper presents an overview of the current methodology and practice in modeling and control of the grinding process in industrial ball mills. Basic The paper reviews the literature on the application of models based on distributed collision energy information to predict size reduction in tumbling mills, in particular ball mills, analyzing(PDF) A Review of Advanced Ball Mill Modelling
احصل على السعر
Grinding in Ball Mills: Modeling and Process Control
I. Introduction Grinding in ball mills is an important technological process applied to reduce the size of particles which may have different nature and a wide diversity of physical, If a ball mill contained only coarse particles, then 100% of the mill grinding volume and power draw would be applied to the grinding of coarse particles. In reality, the mill always contains fines: these fines are present in the ball mill feed and are produced as the particles pass through the mill.MODULE #5: FUNCTIONAL PERFOMANCE OF BALL
احصل على السعر
Methods and Applications in Mechanochemistry:
Mechanochemical bromination of naphthalene (1) is reported, with 1,3-dibromo-5,5-dimethylhydantoin (DBDMH) catalyzed by a FAU-type zeolite in a ball mill. The success of the bromination route in The ball mill modelling scheme using an ore- specific breakage distribution function in a multi-segment ball mill model has provided an adequate representation of industrial ball mill performance. Fur- ther work to extend this technique to ball mills less than 3.2 m in diameter and to mills operating at different process conditions is in progress.Modelling the performance of industrial ball mills using
احصل على السعر
Ball Mill; Principle, Working, and Construction » Pharmaguddu
Attrition: Reduced the size of the materials when they colloid by heavy weight (Ball). Construction: The ball mill grinder consists following Parts: Cylinder: cylinder is made of a hollow metal that moves about its horizontal axis. the cylinder can be made of porcelain, metal, and rubber. the length of the cylinder slightly higher than its diameter.Planetary ball mills are well known and used for particle size reduction on laboratory and pilot scales for decades while during the last few years the application of planetary ball mills has(PDF) Process Engineering with Planetary Ball Mills
احصل على السعر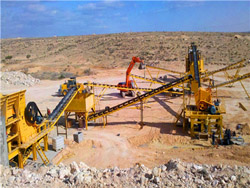
Analiza efektywności mielenia w młynach kulowym i
mm were replaced with 80 mm balls to reduce the amount of coarser particles in circulation. Larger balls reduced the number of particles coarser than 1 mm by about 5%. In case the feed to ball mill was equal to 1200 Mg/h, it resulted in a reduction of 60 Mg/h of the weight of coarse particles in circulation. It also enabled the processing of aAmorphous silica powder (SO-C1, Admatechs, Aichi, Japan) was used to prepare modified silica. The average diameter was 230 nm and a specific surface area of 16.2 m 2 /g measured using the Brunauer-Emmett-Teller method. Twenty grams of silica powder and 250 g of zirconia balls with a diameter of 5 mm were placed in a 250 ml Surface modification of silica powder by mild ball milling
احصل على السعر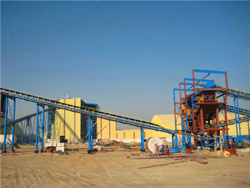
Ball-milling ResearchGate
Ball mill is crucial to numerous industries as an equipment for producing extremely crushed materials, e.g. cement, refractory materials, fertilizers, glass ceramic, ore dressing of ferrous asGrinding in ball mills is an important technological process applied to reduce the size of particles which may have different nature and a wide diversity of physical, mechanical and chemical characteristics. Typical examples are the various ores, minerals, limestone, etc. The applications of ball mills are ubiquitous in mineralGrinding in Ball Mills: Modeling and Process Control
احصل على السعر
(PDF) Calculation method and its application for
its application for energy consumption of ball mills in ceramic industry based on power feature deployment, Advances in Applied Ceramics, DOI: 10.1080/17436753.2020.1732621A ball mill also known as pebble mill or tumbling mill is a milling machine that consists of a hallow cylinder containing balls; mounted on a metallic frame such that it can be rotated along its longitudinal axis. Ball Mill: Operating principles, components, Uses,
احصل على السعر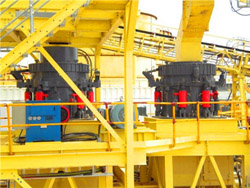
The Selection and Design of Mill Liners MillTraj
Figure 5. High–low wave ball mill liner Materials The selection of the material of construction is a function of the application, abrasivity of ore, size of mill, corrosion environment, size of balls, mill speed, etc. liner design and material of construction are integral and cannot be chosen in isolation.High-energy ball milling (HEBM) of powders is a complex process involving mixing, morphology changes, generation and evolution of defects of the crystalline lattice, and formation of new phases. This review is dedicated to the memory of our colleague, Prof. Michail A. Korchagin (1946–2021), and aims to highlight his works on the synthesis of Materials Development Using High-Energy Ball Milling: A
احصل على السعر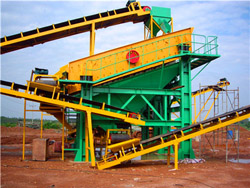
(PDF) Ball milling : A green technology for the preparation
Ball milling is a simple, fast, cost-effective green technology with enormous potential. One of the most interesting applications of this technology in the field of cellulose is the preparation1. The inputs of a coal ball mill are hot air, recycled air, raw coal, and unqualified powder. In the grinding process, the balls are thrown up by the rotating mill, and then fall striking the coals.Application of Fractional Fourier Transform for
احصل على السعر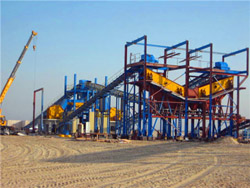
Ball mill Superior cement quality, More fl exibility, higher
The best ball mills, however, enable you to achieve the desired product quality quickly and e ciently, with minimum energy expenditure. That’s what the FLSmidth ball mill is designed to do with the added benefit of high flexibility. You decide whether to operate the mill in open or closed circuit, with or without a pre-grinder.Ball-mills are categorized into four types depending on the motion generated to produce momentum in grinding balls and act upon the material with various milling forces. These are planetary, tumbling, vibratory, and attrition mills. 3.1. Planetary ball mill. Planetary ball mills are simple and efficient in producing ground/pulverized material.Ball-milling: A sustainable and green approach for starch
احصل على السعر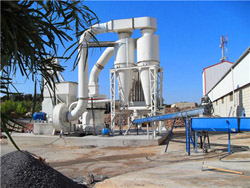
Parameter Optimization of Ball Milling Process for Silica
The results of signal-to-noise analysis obtained the optimum parameter values in a row are: 100 rpm for milling speed parameter, 15: 1 for BPR parameter and 120 minutes for time-miling parameter. The powder size experiment verification of the ball mill process optimization parameter is D50 : 14.99 µm. Export citation and abstract BibTeX RIS.Ball mills are commonly used in single stage fine grinding, regrinding, and as the second stage in two-stage grinding circuits. Ball mills are available in both wet and dry designs, depending on the application. Ball mills have been constructed with standard final product diameters ranging from 0.074 mm to 0.4 mm in diameter.Ball Mill Pharmacy Gyan Principle Construction Working Uses
احصل على السعر