
Batch-Type Ball Mill Institute of Minerals and Materials
Tender No.: IMMT/PA/05/2023 Date: 11.05.2023 INVITATION FOR ONLINE BIDS THROUGH E-TENDERING Director, CSIR-Institute of “Batch-Type Ball Balls for ball mills can be produced by die forging, rolling and casting methods. The rolling of balls can be realized as skew or cross rolling. This paper On some problems of producing grinding media by cross
احصل على السعر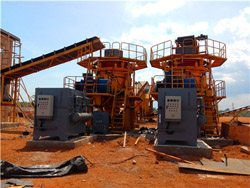
A Review of the Grinding Media in Ball Mills for Mineral
The ball mill is a rotating cylindrical vessel with grinding media inside, which is responsible for breaking the ore particles. Grinding media play an important role [An EOI is only a preliminary step to a formal tender process to understand and identify whether there are potential suppliers in the market that are interested in and capable of Supply of forged grinding media Oyu Tolgoi LLC
احصل على السعر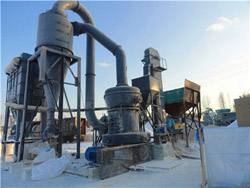
(PDF) Grinding in Ball Mills: Modeling and Process
The paper presents an overview of the current methodology and practice in modeling and control of the grinding process in industrial ball mills. Basic kinetic and energy models of the...The ball mill Ball milling is a mechanical technique widely used to grind powders into fine particles and blend materials. 18 Being an environmentally-friendly, cost-effective technique, it has found wide Ball milling: a green technology for the
احصل على السعر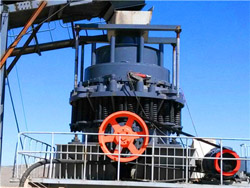
行星式球磨仪PM100--德国RETSCH(莱驰)研磨仪粉
The Planetary Ball Mill PM 100 is a powerful benchtop model with a single grinding station and an easy-to-use counterweight which compensates masses up to 8 kg. It allows for grinding up to 220 ml sample material Ball grinding can be carried out in either dry-operation or wet-operation. The former is widely used in coal-fired power plants and cement industry, and the latter is Ball Grinding Process SpringerLink
احصل على السعر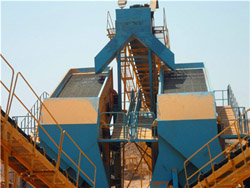
Ball Mill an overview ScienceDirect Topics
Ball mills give a controlled final grind and produce flotation feed of a uniform size. Ball mills tumble iron or steel balls with the ore. The balls are initially 5–10 cm diameter but Open Circuit Grinding. The object of this test was to determine the crushing efficiency of the ball-mill when operating in open circuit. The conditions were as follows: Feed rate, variable from 3 to 18 T. per hr. Ball load, 28,000 lb. of 5-, 4-, 3-, and 2½-in. balls. Speed, 19.7 r.p.m.Ball Mill Grinding Theory Crushing Motion/Action Inside
احصل على السعر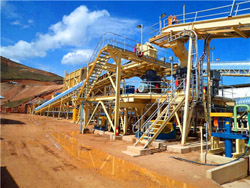
Supply of forged grinding media Oyu Tolgoi LLC
[An EOI is only a preliminary step to a formal tender process to understand and identify whether there are potential suppliers in the market that are interested in and capable of satisfying the procurement needs] Scope description: Supply of forged grinding media: 65mm Roll forged steel grinding media for BALL mill applicationCERAMIC LINED BALL MILL. Ball Mills can be supplied with either ceramic or rubber linings for wet or dry grinding, for continuous or batch type operation, in sizes from 15″ x 21″ to 8′ x 12′. High density ceramic linings of uniform hardness male possible thinner linings and greater and more effective grinding volume.Ball Mills 911 Metallurgist
احصل على السعر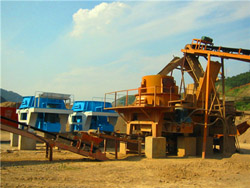
(PDF) SIZE REDUCTION BY GRINDING METHODS
Ball mills are used for wet grinding iron ore, g old/copper ore, nickel ore and other ores, as wel l as . lime/limestone for flue gas desulphurisat ion systems, coal and other raw materials.Isa Mills: <0.1” grinding balls are recommended. The Isa Mill is more efficient when using small media (i.e. high-chrome steel balls). Rotary Mills: Small cylpebs (<1”) are effective in ultra-fine wet regrinding operations. SAG Mills: 4”-6” forged-steel balls are recommended. Cast balls are not agood choice.Grinding Balls and Other Grinding Media: Key consumables
احصل على السعر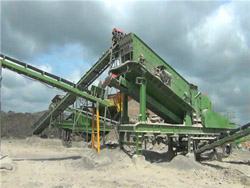
Energy-Efficient Technologies in Cement Grinding IntechOpen
The energy consumption of the total grinding plant can be reduced by 20–30 % for cement clinker and 30–40 % for other raw materials. The overall grinding circuit efficiency and stability are improved. The maintenance cost of the ball mill is reduced as the lifetime of grinding media and partition grates is extended. 2.5.C. Obry. Karl-Heinrich Zysk. Vertical roller mills are the mills traditionally used for processing granulated blastfurnace slag and for grinding composite cements. From the energy aspect they areCements ground in the vertical roller mill fulfil the quality
احصل على السعر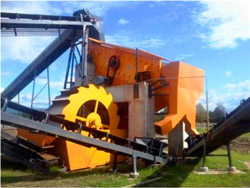
行星式球磨仪PM100--德国RETSCH(莱驰)研磨仪粉碎仪
Download. The Planetary Ball Mill PM 100 is a powerful benchtop model with a single grinding station and an easy-to-use counterweight which compensates masses up to 8 kg. It allows for grinding up to 220 ml sample material per batch. The extremely high centrifugal forces of Planetary Ball Mills result in very high pulverization energy andThe performance of grinding media in a ball mill is also measured in terms of its wear rate. Abrasive ores such as gold and copper produce high wear rates of about 120µm/hr [74]. The wear of(PDF) A comparison of wear rates of ball mill grinding media
احصل على السعر
Analiza efektywności mielenia w młynach kulowym i
located in Kazakhstan, two high-pressure grinding rolls for milling and only one ball mill grinding stage were used. The maximum particle size for roll presses in this plant is equal to 38 mm and it is the result of the fragmentation of the material in a cone crusher. The product crushed in the first roll pressThe result revealed that the energy required by a ball mill, high-pressure homogenizer and twin screw extruder were 232.5, 43.3, and 5 kWh/kg of biomass, respectively . Kim et al. showed that a large amount of energy was needed by the planetary ball mill for grinding rice straw compared to the attrition mill.Ball milling as an important pretreatment technique in
احصل على السعر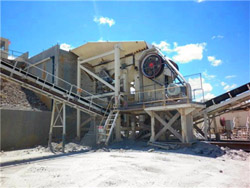
Effect of Slurry Concentration on the Ceramic Ball
Ceramic grinding, which in this paper is defined as a method of using ceramic materials as grinding media, is favored by many processing plants as an emerging high-efficiency and energy-saving The ball mill Ball milling is a mechanical technique widely used to grind powders into ne particles and blend materials.18 Being an environmentally-friendly, cost-effective technique, it has found wide application in industry all over the world. Since this mini-review mainly focuses on the conditions applied for the prep-Ball milling: a green technology for the preparation and
احصل على السعر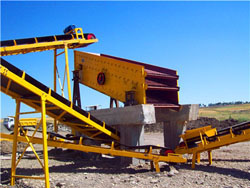
THE WEST BENGAL POWER DEVELOPMENT
Tender Ref. No. : 468B1SS13-14GT . 1.0 Kolaghat Thermal Power Station (KTPS) of The West Bengal Power Development Corporation Ltd. Grinding Ring set for Ball Mills and has adequate technical knowledge and has relevant experience. AND . ii. Has manufactured & supplied Grinding Ring & Ball set of 8.5 E (10) Coal Mills during Procurement Of Grinding Balls For Bbd 4772 Ball And Tube Mills Barauni Procurement Of Grinding Balls For Bbd 4772 Ball And Tube Mills Barauni Grinding Balls 50 Mm Pno Hy 6210903630.., sipat, Chhattisgarh Tenders. Bid Submission date : 11-06-2022. TDR : 32366991Procurement Of Grinding Balls For Bbd 4772 Ball An Tender
احصل على السعر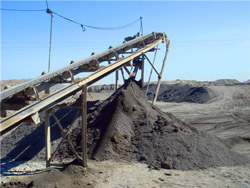
Planetary Ball Mill PM 100 RETSCH highest fineness
The Planetary Ball Mill PM 100 is a powerful benchtop model with a single grinding station and an easy-to-use counterweight which compensates masses up to 8 kg. It allows for grinding up to 220 ml sample material per batch. The extremely high centrifugal forces of Planetary Ball Mills result in very high pulverization energy and therefore shortThe semi-autogenous mill is a new type of grinding equipment with both crushing and grinding functions. It has the advantages of simple process flow, small investment, short construction cycle, and easy operation. It can directly grind raw materials or coarsely crushed materials to 0.074mm. The grinding ratio can reach 4000-5000, which is tenSemi Autogenous Mill SAG Mills For Sale AGICO
احصل على السعر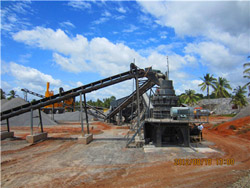
Ball Mill an overview ScienceDirect Topics
Mechanical Crushing and Grinding. Oleg D. Neikov, in Handbook of Non-Ferrous Metal Powders, 2009 Tumbling Ball Mills. Tumbling ball mills or ball mills are most widely used in both wet and dry systems, in batch and continuous operations, and on a small and large scale.. Grinding elements in ball mills travel at different velocities. Therefore, collision This paper presented a new method for producing grinding media for ball mills, based on the cross wedge rolling technique. It is a medium-throughput technique, i.e., its throughput is higher than in die forging but lower than in skew rolling. The paper investigates typical failure modes which may occur during the rolling process.On some problems of producing grinding media by cross
احصل على السعر