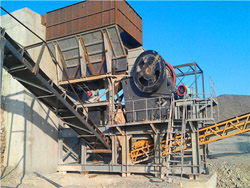
The cement plant of tomorrow ScienceDirect
The stability of the continuous production process in cement plants has a big influence on its energy efficiency. Due to varying material or fuel properties, the The cement manufacturing process mainly includes four steps: resource extraction, raw material preparation, clinker calcination, cement grinding 17,18, and fossil Modernizing cement manufacturing in China leads to
احصل على السعر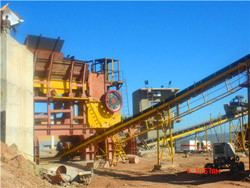
Carbon Capture in the Cement Industry: Technologies,
For application at cement plants, partial oxy-fuel combustion, amine scrubbing, and calcium looping are the most developed (TRL 6 being the pilot system demonstrated in relevant The Cement Plant Operations Handbook is a concise, practical guide to cement manufacturing and is the standard reference used by plant operations personnel The Cement Plant Operations Handbook International
احصل على السعر
Digitization and the future of the cement plant McKinsey
Our vision: The leading cement plant of 2030. The cement plant of the future achieves considerably lower operating costs and higher asset value through higher 96 行The key mass and energy flows processed through each main plant systems (e.g. cement plant, carbon capture unit, CO 2 conditioning, air separation unit, power plant Cement Plant an overview ScienceDirect Topics
احصل على السعر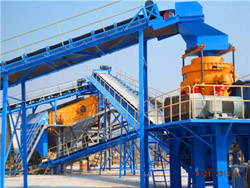
Cement plant performance optimization Benchmarking,
Collection of operational data. Analysis of process performance and site constraints. Plant modeling. Usage of obtained process models and operational data to Production Planning Using Day-Ahead Prices in a Cement Plant. Turgay Emir, Mehmet Güray Güler, in Exergetic, Energetic and Environmental Dimensions, 2018. Abstract. Cement Production an overview ScienceDirect Topics
احصل على السعر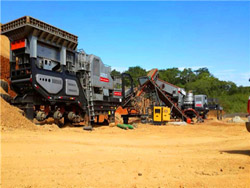
Advanced process control for the cement industry
process experts designs solutions specifically for cement applications. With more than 40 years of plant automation experience, FLSmidth has installed over 700 control systems and 450 laboratory systems and understands the needs of today’s cement plants. FLSmidth is a world leader in building and maintaining cement plants, andThe cement grinding unit manufactured by our company merges drying, grinding, powder classifying, dust collecting and cement packing into a single. It can not only grind cement clinker but also process cement admixture, such as gypsum, fly ash, furnace slag, coal gangue, etc., realizing a stable, high-quality and automated cement production.Cement Grinding Unit Clinker Grinder AGICO Cement
احصل على السعر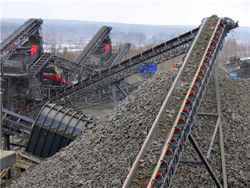
Cement Plant an overview ScienceDirect Topics
The key mass and energy flows processed through each main plant systems (e.g. cement plant, carbon capture unit, CO 2 conditioning, The original process at the Ramla cement plant to produce cement from limestone, which is the base material of cement, was a so-called wet line process. The original wet line had a capacity of 1,800 TPD (Tons6. System 800xA configuration provided at 6500tpd case Star cement plant, Ras Al-Khaima, UAE A typical configuration of an implemented 800xA and Minerals Library control system is the Star Cement plant. It has Profibus based field instrumentation, other electrical interfaces as well as third party OPC interfaces. Please refer to Figure 6 New trends in Process Automation for the cement
احصل على السعر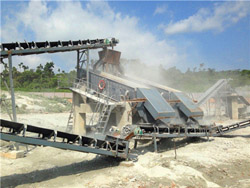
Cement plant performance optimization Benchmarking,
performance and energy efficiency at cement plants using diagnostic, corrective and long-term continuous improvement activities. Cement FingerPrint ABB’s Cement FingerPrint is a process optimization and energy consulting service designed to capture, analyze and improve operational performance and energy efficiency of the Emergency power 12. Plant control systems 6. Cement milling process summary data 8. Typical equipment downtime 110 1. Storage of clinker and other components 2. Cement milling 3. Separators (classifiers) 4. Ball mill circuit control 5. Cement storage 6. Cement dispatch 7. Distribution 8.The Cement Plant Operations Handbook International
احصل على السعر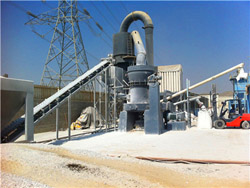
Atmosphere Free Full-Text An Integrated System
In the cement production process, carbon dioxide (CO2), nitrogen oxides (NOx), sulphur dioxide (SO2), methane (CH4) and particulate matter (PM) were the major gases emitted. The cement production of GHGs depends on factors including the fuel used, the emission control system, the technology used, a plant’s geographic location 4.3.5 Technical Considerations for Biomass Integration in the Cement Process .. 49 4.3.6 Main Steps to Schematic of the AK System Process .. 21 Figure 24: Schematic of the Biomass Drying cement plants to reduce their operating costs and improve their carbon footprints. The reports provide a plethora ofINCREASING THE USE OF ALTERNATIVE FUELS AT
احصل على السعر
(PDF) Process Automation of Cement Plant ResearchGate
The “Kosovo Lignite Basin” with a length of 85 km from North to South, an East to West-extension of around 10km and more than 10,000 Mt inventory is one of the largest lignite deposits in Europe.Waste heat is mainly liberated from kiln preheater system, clinker cooler, and combustion exhaust gases. The amount of heat liberated from a cement plant to the surrounding may reach 40% of the energy consumed in the production process [12]. Power generation from waste heat recovery may provide about 20% of energy consumption in a Power generation in white cement plants from waste heat
احصل على السعر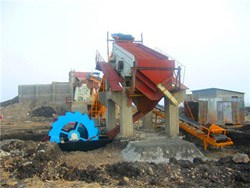
Cement industry solutions ABB
Global cement producer Votorantim Cimentos achieves multi-site digitalization with ABB industry-specific solutions. . ABB upgrades process control systems and cement grinding units in UAE for Experimental research on cement grate cooler system and numerical simulation of its clinker cooling process. Applied Thermal Engineering, 181, 115904. [Web of Science ®], [Google Scholar] Shao, W., Cui, Z., Wang, N., & Cheng, L. (2016). Numerical simulation of heat transfer process in cement grate cooler based on dynamic mesh technique.Full article: Evaluation of optimization techniques for
احصل على السعر
Pyroprocessing and Kiln Operation Indian Cement Review
Pyro-processing section is considered to be the heart of a cement plant as actual cement clinker production takes place in kilns. The size of a cement plant is determined based on the pyro-processing section and the sizes of all other equipment are determined to match pyro-processing. Cyclones are basic units in a preheater system.cement intergrinding and blending process and the corre-sponding plant concept, chosen at a specific site, depend on the cement type to be produced, with special importance of the grindability, humidity, and the abrasive behaviour of its compounds. Sometimes, those processes may be performed at the plants that are in separate Research Article Parametric Studies of Cement
احصل على السعر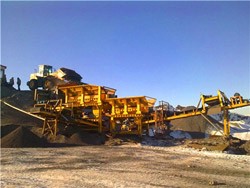
Heat Integration in a Cement Production IntechOpen
The author concluded that the energy consumption of the particular cement plant may be lowered by 30%. Thus, the features of the cement production process forced a methodology update to suggest feasible retrofit pathways with the objective of achieving the optimal temperature approach of the heat exchange system.A. Description of the plant. The studied plant belongs to Lafarge, which is a private French company; it is the sole shareholder of the cement plant in Algeria (Fig. 1) [].The company’s investment in Algeria in the first phase was to install a production line with an equivalent capacity of 2 million tons of cement per year, estimated at 260 million euros.Identification and Modeling of a Rotary Kiln in Cement Plant
احصل على السعر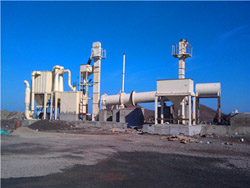
11.6 Portland Cement Manufacturing U.S.
produced in portland cement manufacturing plants. A diagram of the process, which encompasses production of both portland and masonry cement, is shown in Figure 11.6-1. As shown in the figure, the process can be divided into the following primary components: raw materials acquisition and handling, kiln feed preparation, pyro Grinding of clinker consumes power in the range of 2.5 kWh/ton of clinker produced. These and other pyroprocessing parameters make cement production costly. The pyroprocessing process in kilns and the grinding technologies therefore have to be optimized for best processing. This paper discusses the cement manufacturing and grinding A Review on Pyroprocessing Techniques for Selected Wastes
احصل على السعر
Guidebook for Using the Tool
4 for grinding,3 and a gravity (multi-outlet silo) dry system at 0.10 kWh/t raw meal for homogenization.4 Based on the above values, the overall best practice value for raw materials preparation is 12.05 kWh/t raw material. Ideally this value should take into account the differences in moisture content of the raw materials as well as the hardness of
احصل على السعر