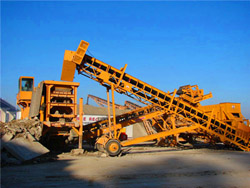
BALL MILLS Ball mill optimisation holzinger
Ball mill optimisation As grinding accounts for a sizeable share in a cement plant’s power consumption, optimisation of grinding equipment such as ball mills can The main operating costs in tumbling mills are power, grinding media, and liners. In SAG and ball milling circuits, depending on the abrasiveness of the ore being (PDF) Reducing the Cost of Grinding Media Consumption
احصل على السعر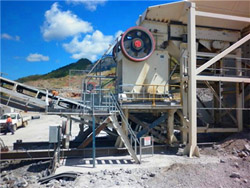
(PDF) Grinding Media in Ball Mills-A Review
Grinding Media in Ball Mills-A Review CC BY 4.0 Authors: Nyasha Matsanga Willie Nheta Ngonidzashe Chimwani Comminution is a very important and result-determining step in mineral processing....Several authors have developed simplified tests to predict ball mill’s energy consumption, typically using the Bond Ball Mill Work Index (BBMWI) as a reference. One Mine operating costs and the potential impacts of energy and grinding
احصل على السعر
Consumption of steel grinding media in mills A review
Grinding circuit operators have long been aware of the significant impact of grinding media consumption on the cost of grinding. Comminution accounts for an Ab surface area of ball or sphere, m 2 Ai abrasion index, Alball surface area of grinding ball in laboratory mill, m 2 Arball surface area of grinding ball in industrial Consumption of steel grinding media in mills A review
احصل على السعر
(PDF) Grinding in Ball Mills: Modeling and Process
A ball mill is a type of grinder widely utilized in the process of mechanochemical catalytic degradation. It consists of one or more rotating cylinders partially filled with grinding...The ball mill Ball milling is a mechanical technique widely used to grind powders into fine particles and blend materials. 18 Being an environmentally-friendly, cost-effective technique, it has found wide Ball milling: a green technology for the
احصل على السعر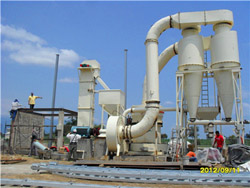
A parametric cost model for mineral grinding mills
The objective of this work was to develop a set of cost functions for major grinding mill equipment. These cost models were developed using two relatively different @article{osti_5719847, title = {Cost optimization of stirred ball mill grinding}, author = {Schultz, C W and Mehta, R K}, abstractNote = {On going research at the University of Alabama has shown that stirred ball mill grinding is the highest cost unit operation in the beneficiation of Eastern Oil Shales. Minimization of that cost is critical if oils derived by Cost optimization of stirred ball mill grinding OSTI.GOV
احصل على السعر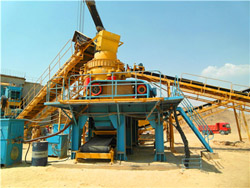
Consumption of steel grinding media in mills A review
Likewise, Hebbar (2011) has studied the grinding wear behaviour of austempered ductile iron as media material in the comminution of Kudremukh haematite iron ore in a ball mill. The grinding experiments were conducted under different pH conditions, i.e. pH = 7.0 and pH = 8.5, while keeping other parameters fixed, at a mill speed of 74 The drawback of attritor mills is the extremely high degree of wear during operation on the mill bodies, which increases the overall cost of mill operation and causes contamination of the biomass Kim et al. showed that a large amount of energy was needed by the planetary ball mill for grinding rice straw compared to the attrition mill. TheBall milling as an important pretreatment technique in
احصل على السعر
(PDF) Grinding in Ball Mills: Modeling and Process Control
A ball mill is a type of grinder widely utilized in the process of mechanochemical catalytic degradation. It consists of one or more rotating cylinders partially filled with grinding balls (madeThe energy consumption of the total grinding plant can be reduced by 20–30 % for cement clinker and 30–40 % for other raw materials. The overall grinding circuit efficiency and stability are improved. The maintenance cost of the ball mill is reduced as the lifetime of grinding media and partition grates is extended. 2.5.Energy-Efficient Technologies in Cement Grinding IntechOpen
احصل على السعر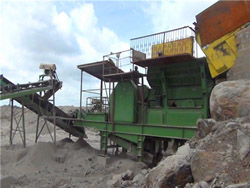
(PDF) Energy Efficient Ball Mill Circuit ResearchGate
The samples, once broken, can be used subsequently for Bond ball mill work index or batch grinding tests, therefore limiting overall sample requirements.The test generates an index (DWi) that canIsa Mills: <0.1” grinding balls are recommended. The Isa Mill is more efficient when using small media (i.e. high-chrome steel balls). Rotary Mills: Small cylpebs (<1”) are effective in ultra-fine wet regrinding operations. SAG Mills: 4”-6” forged-steel balls are recommended. Cast balls are not agood choice.Grinding Balls and Other Grinding Media: Key consumables
احصل على السعر
Ball milling: a green technology for the preparation and
The ball mill Ball milling is a mechanical technique widely used to grind powders into ne particles and blend materials.18 Being an environmentally-friendly, cost-effective technique, it has found wide application in industry all over the world. Since this mini-review mainly focuses on the conditions applied for the prep-A ball mill capable of producing 30 tons per hour is likely to fall into the medium to large size category. Based on historical data, a rough estimate for a ball mill with a 30-ton-per-hour outputHow much does a ball mill with an output of 30 tons per hour cost?
احصل على السعر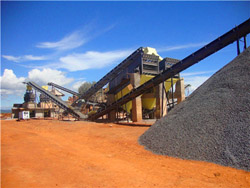
Ball mill abrasion test (BMAT): Method development and
Introduction. The ball mill abrasion test (BMAT) is an industrially-relevant multipurpose wear test method that enables tribologists and abrasion scientists to study the abrasive wear behaviour of materials for various service applications, particularly for grinding balls and mill liners, under conditions and contact mechanics very similar to the industrial An estimated consumption of steel grinding media of around 600,000 tons p.a. in the 1980s already gives an indication of the scale of the problem (Malghan, 1982). Likewise, in the cement industry, as mills are supplied for ever increasing capacities, the ball size distribution and wear exact a tremendous effect on the profitability of producingConsumption of steel grinding media in mills A review
احصل على السعر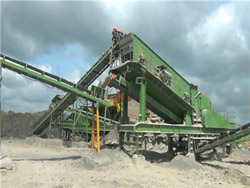
Grinding Media in Ball Mills-A Review ResearchGate
In ball mill operations, it is always helpful to optimise the grinding media system to min- imize the costs of the operation. In a research done by Yu et al. [16] to optimize grinding media systemThe grinding was performed in a dry state using a cryogenic grinder 6970EFM Freezer/Mill® (6970 EFM, SPEX SamplePrep, Metuchen, NJ, USA) which consisted of two stainless steel vessels, with each being able to hold four standard grinding vials. The mill was equipped with a totally enclosed liquid nitrogen (LN 2) auto-fill system, Choosing the right strategy: cryogrinding vs. ball milling comparing
احصل على السعر
(PDF) Autogenous and Semi-Autogenous Mills, 2015 Update
Mills of 44 ’ (13. 41 m) diameter with 32 MW (42,900 HP) and Ball Mills of 30’ (9.14 m) in d iameter and 28 MW (37,500 HP). Single grinding lines will process 200,000 mtpd of ore and more.Following are advantages of VRM over Ball Mills with reference to these issues: • Strong drying ability Inlet hot air from Kiln can dry materials with 20% water content. (max moisture 20% vs. 3% in ball mill) [15], [16]. • Big feed size The vertical roller mill can grind the material of particle size of 5% of the grinding roller diameter.Review on vertical roller mill in cement industry & its
احصل على السعر
Key issues and challenges in spice grinding ScienceDirect
Grinding is an age-old technique of particle size reduction to produce powders that can be used as intermediate or end products. Grinding aims to reduce the size of the particle by mechanical means such as impact, compression, shear, and cutting (Sahay and Singh, 1996).Hammer mill, plate mill, ball mill, pin mill, roller mill are The ball mill Ball milling is a mechanical technique widely used to grind powders into fine particles and blend materials. 18 Being an environmentally-friendly, cost-effective technique, it has found wide application in industry all over the world. Since this mini-review mainly focuses on the conditions applied for the preparation andBall milling: a green technology for the preparation and
احصل على السعر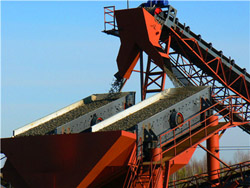
Mine operating costs and the potential impacts of energy and grinding
Potential cost savings measures. This study has found that in general the relative Mining and Milling costs of a given operation do not significantly differ, and generally fall within the range of 43:43:14 to 45:45:10 (Mine:Mill:G & A). In addition, G & A costs were found to be consistently lower than both Milling and Mining costs.Grinding iron ores in conventional ball mills involve a considerably high consumption of metallic media, resulting in high operating costs. In the case of compact itabirites, the high silica content increases such consumption, potentially exceeding the costs associated with electric power consumption in industrial operations. This paper presents Study on Partial Replacement of Metal Grinding Ball with
احصل على السعر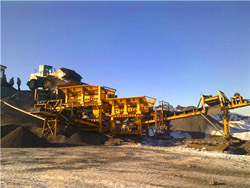
Methodologies for the evaluation of grinding media
Due recognition of the significant impact of the cost of grinding media on the overall economics of comminution facilities worldwide has created the need for reliable, practical methodologies to compare—over extended control periods—different operating conditions, arising from eventual changes in ore type, ball supplier or simply, a trial of
احصل على السعر